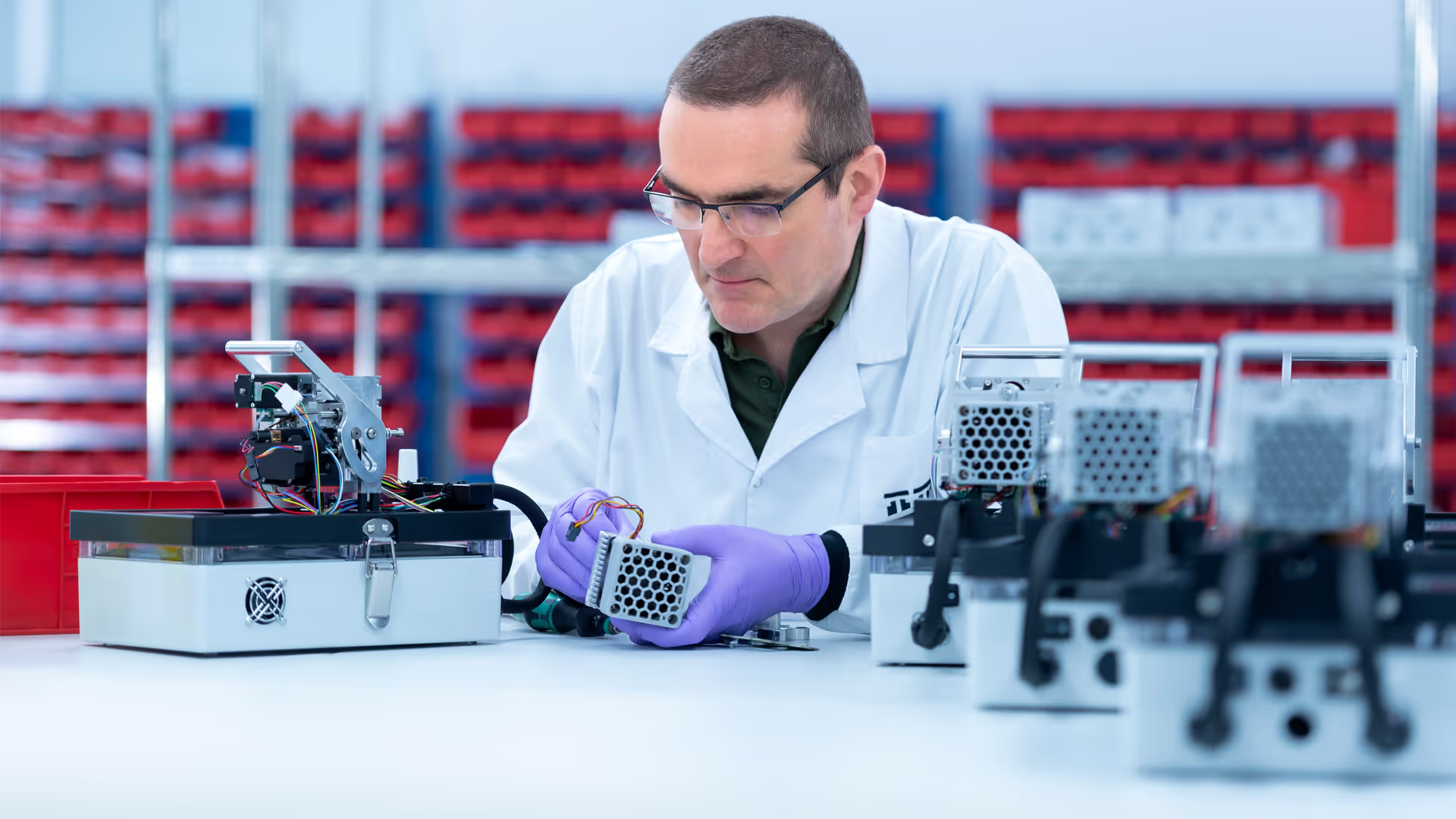
Medical device design and development
Transforming bold ideas into market-ready solutions.
Medical device development is a structured yet flexible journey - one that demands meticulous planning, a clear understanding of risks and trade-offs, and a focus on quality and regulatory compliance.
Success depends on a documented, strategic approach that aligns with standards such as ISO 13485 and FDA requirements.
With more than 35 years of experience, TTP has developed a proven process grounded in real-world delivery. Because every client is unique, we tailor the development process to your specific goals, whether that’s building functional prototypes to secure investment or scaling up to meet commercial demand. Every step is designed to fit your team’s needs and accelerate your path to market.
Phase 1: Discovery
Discovery is about articulating a clear commercial need, a desirable product vision, and a viable technical approach to achieve it. TTP’s Medical Device Development Consulting team uses a range of techniques to develop a broad understanding of your overall product needs. This includes ethnographic research, literature review, discussions with our Clinical Network and others. By considering patients, surgeons, payors, regulators, and others, we uncover what it takes for the product to get to market and succeed.
We then assess risk and challenge by constructing an early, end-to-end risk register. This includes techniques like formal comparison with existing products, product concept testing with users, and technical feasibility studies. Having assessed value, cost and risk, we help you make informed choices around a target product profile. This is often in the form of a generational product plan.
The TTP MedTech difference
Our team of medical device and drug delivery experts draws on decades of experience to identify risks when product concepts are still quite nebulous, which ensures more effective risk evaluation. This, in turn, makes it much less likely that your development will accidentally carry forward risks which are not commercially valuable. When Carbometrics partnered with TTP to explore how their biomimetic Glucose Binding Molecules (GBMs) could enable next-gen Continuous Glucose Monitoring (CGM) sensors, TTP developed and tested prototype sensing membranes, providing key data to model sensor behaviour, assess approaches and identify development challenges for commercialisation. Read the full case study.
"TTP played an essential role in assessing the feasibility of an exciting new Continuous Glucose Monitoring (CGM) concept discovered at Carbometrics Limited. The team are hugely experienced, professional and efficient. They are well versed in the immense challenges that pave the way from concept to product and we learned a huge amount working with them."
Andy Chapman, CEO and Co-founder of Carbometrics
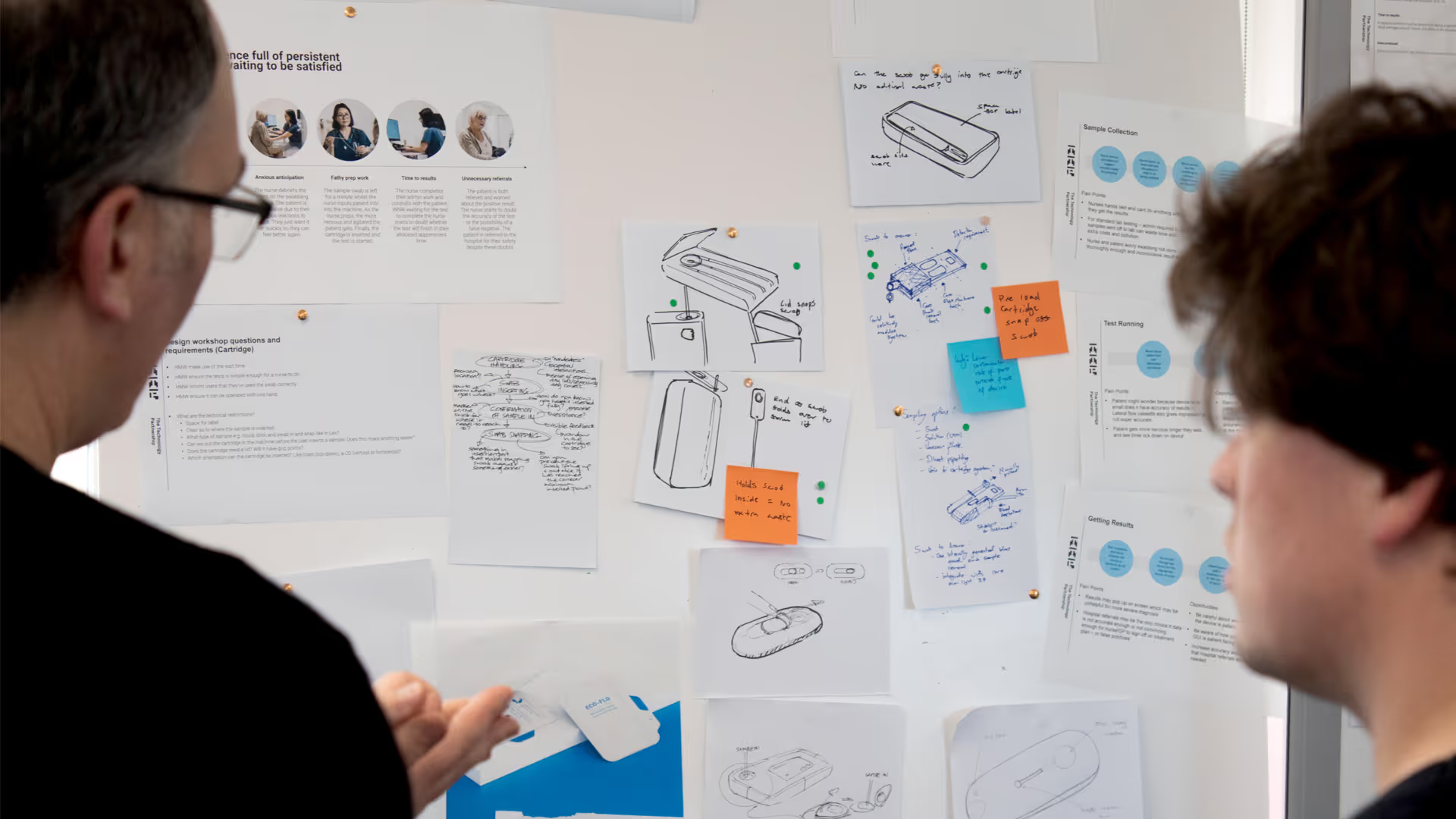
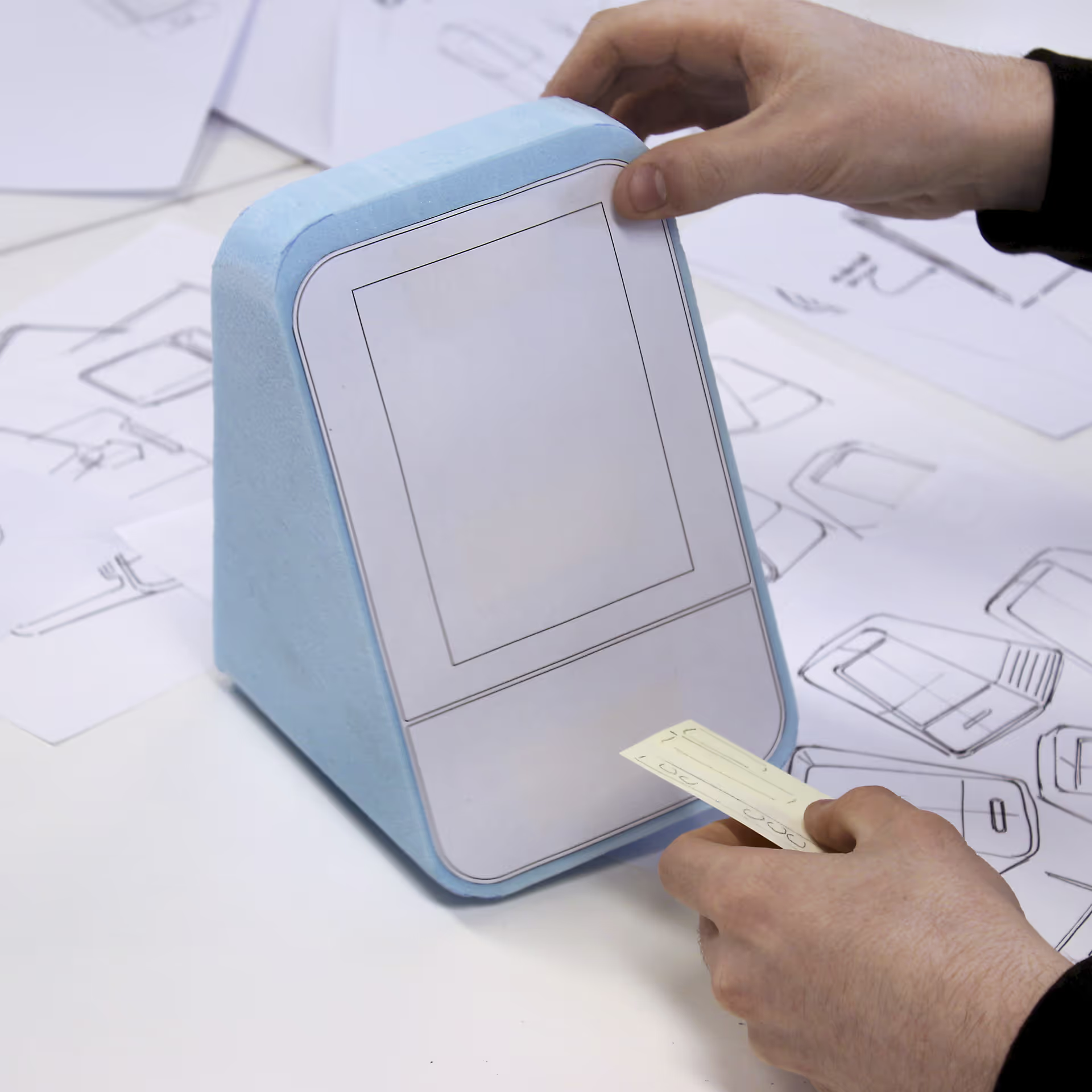
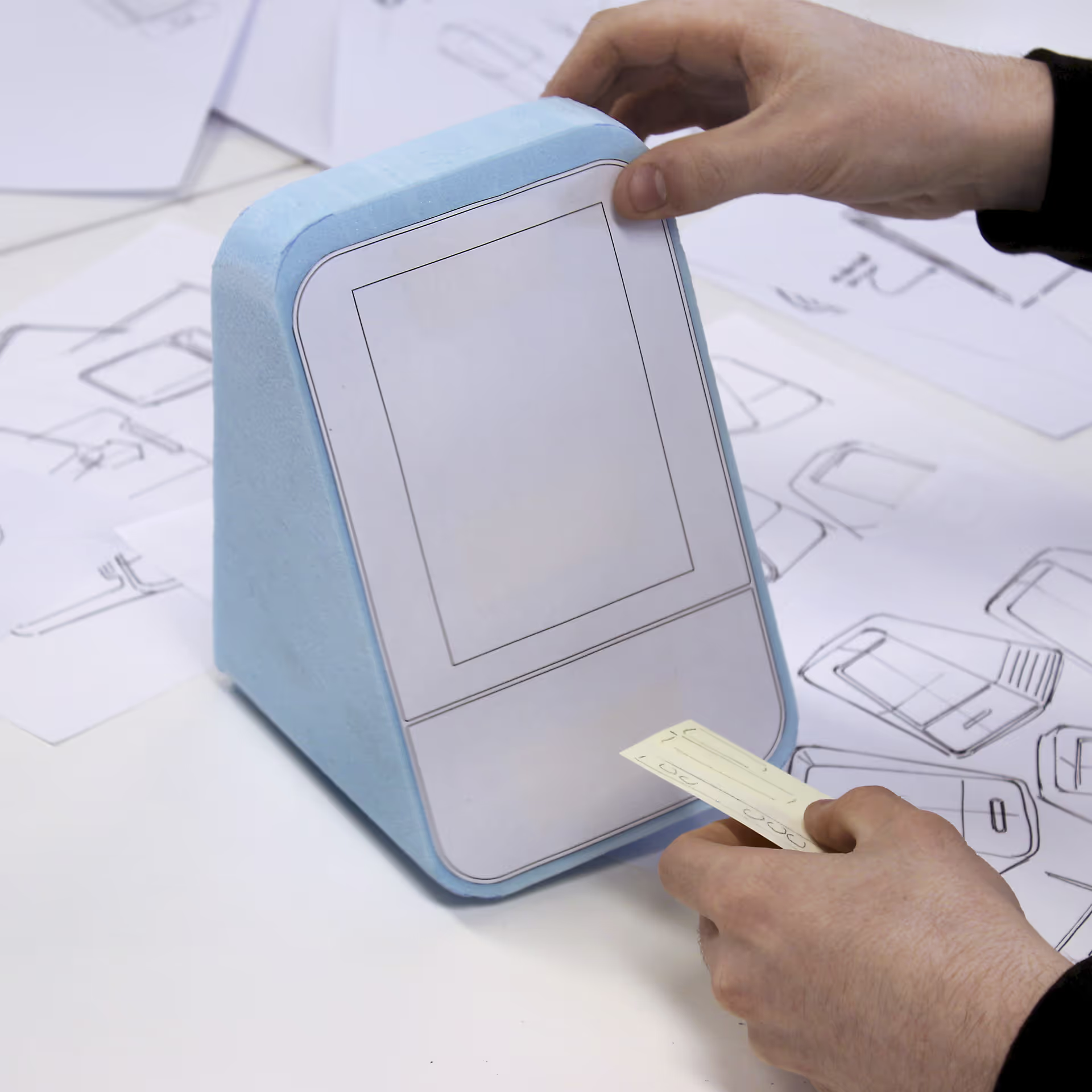
Phase 2: Concept Development
Concept Development involves deciding how all key product functions will be delivered. It also involves assessing and eliminating the risks associated with those choices. TTP refines and defines product requirements based on phase 1 in parallel with identifying robust solutions. We combine formative human factors studies with exploratory technical work so we can explore critical trade-offs with stakeholders effectively. This helps build confidence that technical success will lead to a delightful product.
On the design side, we emphasise derisking above all. We create design options and evaluate their capabilities – at module and system level. Evaluation is driven by risks – ranging from harms to users to manufacturability to cost of goods – using design FMEAs, direct experiment, finite element analysis, discussions with CMOs, and other techniques. By focusing on risks, we retain flexibility to fix issues easily until we have evidence of design performance.
The TTP MedTech difference
Through disciplined systems engineering approaches – again, enabled by vast experience – TTP mitigates the risk of “design lock-in”, in which a prematurely integrated and detailed design makes solving vital problems difficult. As an example, in response to a global flu pandemic threat in 2006, TTP partnered with Hovione to develop the TwinCaps® dry powder inhaler. By focusing on a single design concept and leveraging rapid prototyping, TTP accelerated the product’s development, leading to its launch, becoming a best-selling disposable inhaler. Read the case study.
"We’ve worked closely with TTP for years to develop a number of respiratory products, and have always been impressed by their inventiveness, lateral thinking and ability to deliver. Our partnership has shown the benefits of working together to design innovative and reliable technologies that can be quickly turned into manufacturable products."
Peter Villax, CEO, Hovione Technology
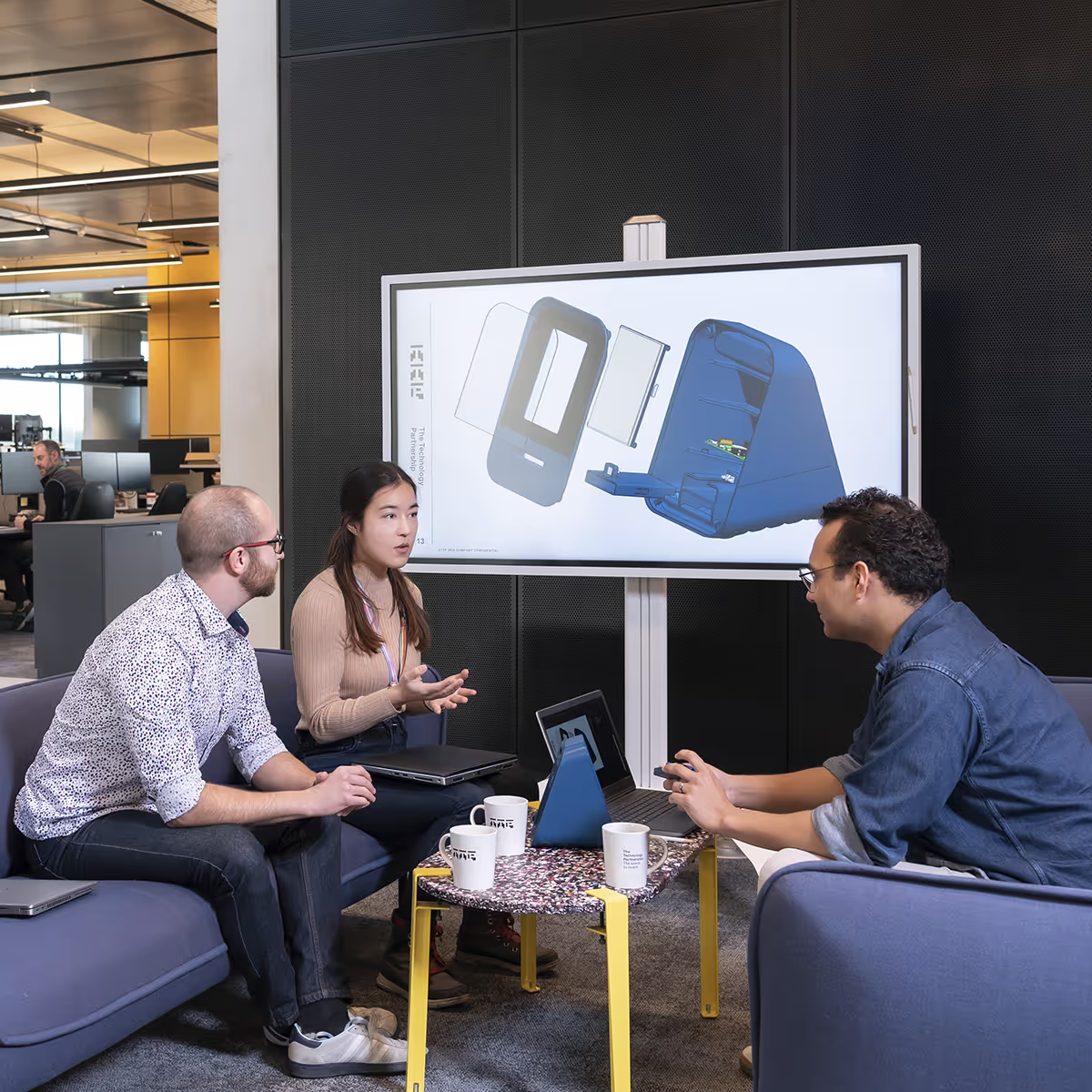
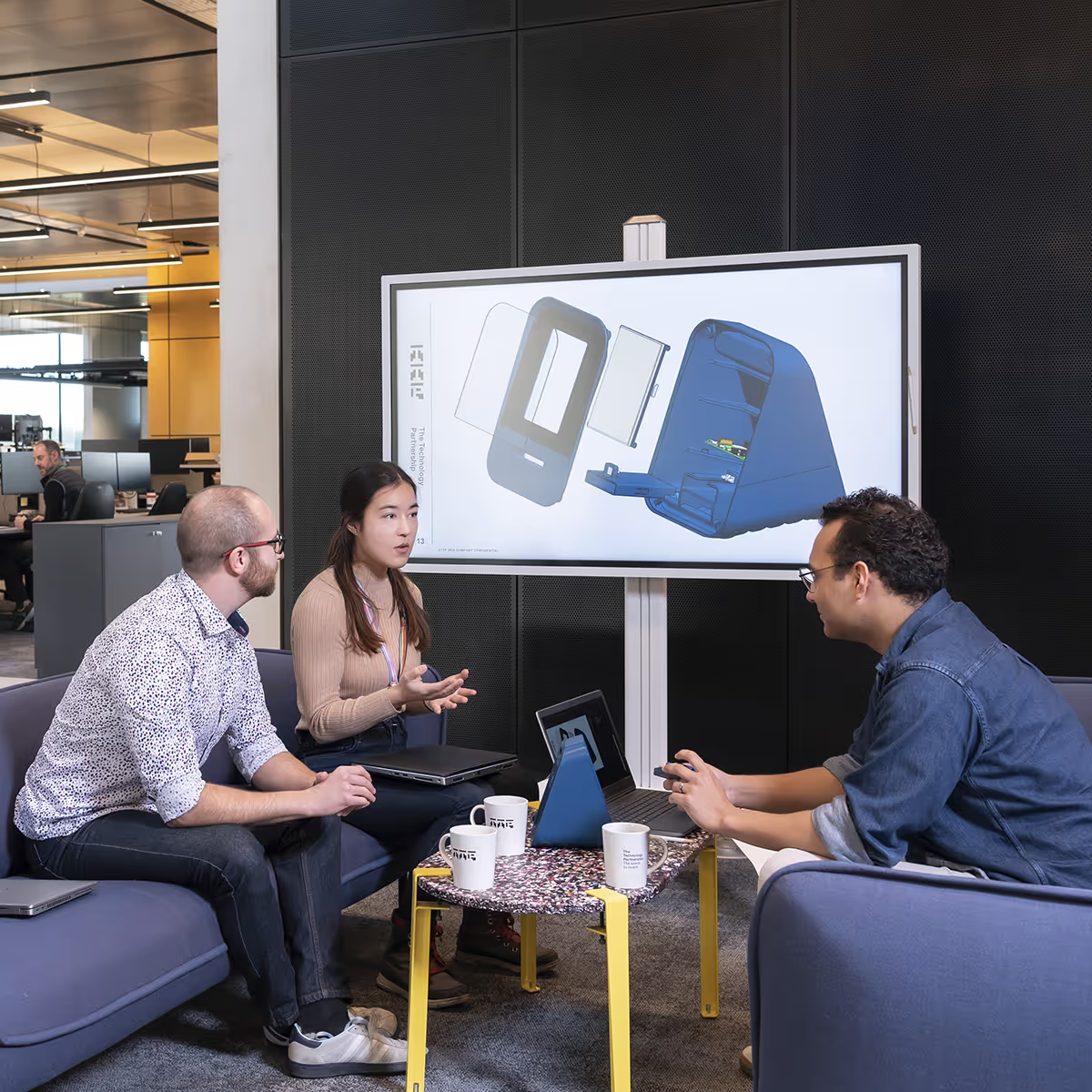
Phase 3: Detailed Design
Detailed Design takes you from evidence that an approach works to an integrated, packaged design - along with the means to produce it representatively. Building on the module-and-system designs from phase 2, this stage blends design integration with technical testing, formative human factors work, formal risk management, and discussion with contract manufacturing organisations (CMOs).
Starting broadly, these become increasingly detailed as the design progresses and requires more specific answers. Pilot-scale manufacturing and assembly processes are defined in parallel. This typically involves collaboration with other partners and follows your manufacturing strategy. The result is a representative product, ready for validation. Typically, the ISO 13485 Quality Management System (QMS)is present in all phases but becomes more prominent in Phase 3, as designs and data may be needed for regulatory submissions. Designed to adapt to your needs, TTP's QMS ensures everything is captured in a project quality agreement.
The TTP MedTech difference
TTP’s distinctive “progressive testing” approach mitigates risks early while design flexibility remains, extending into phase 3 to minimise surprises and ensure a smoother transition to late-stage design and manufacturing. With decades of experience, TTP delivers tailored solutions that anticipate challenges and maximise your device’s commercial and clinical impact. Find out how TTP transformed Serac Imaging Systems' prototype into a portable gamma-optical imaging device through wide expertise in physics, engineering, software and human factors. Read the case study.
“The team at TTP has done a fantastic job expediting the journey to commercialisation of our prototype. We are excited about the potential for Seracam to improve patients’ lives.”
Dr Paul Cload, Chief Marketing Officer at Serac Imaging Systems
Meet us at
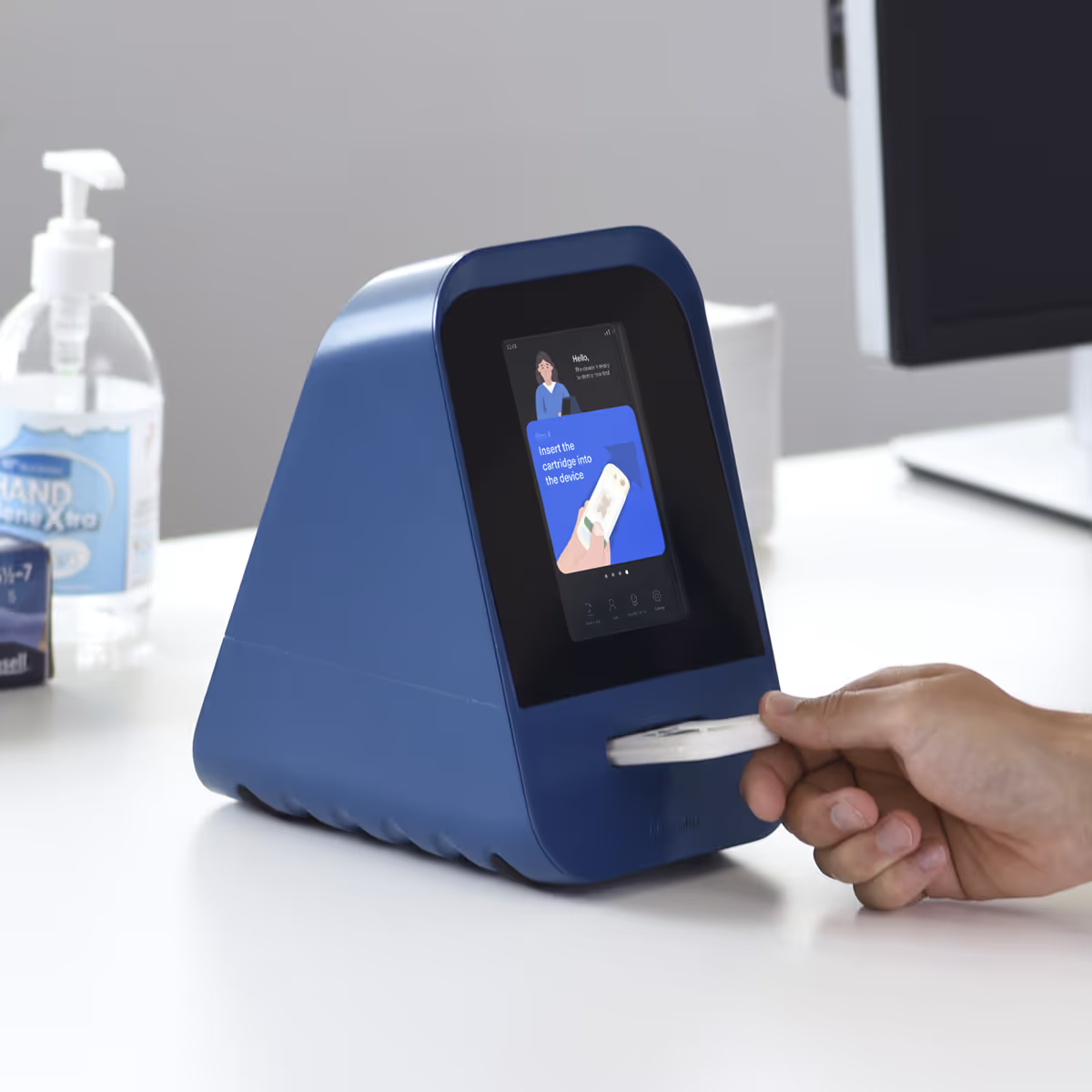
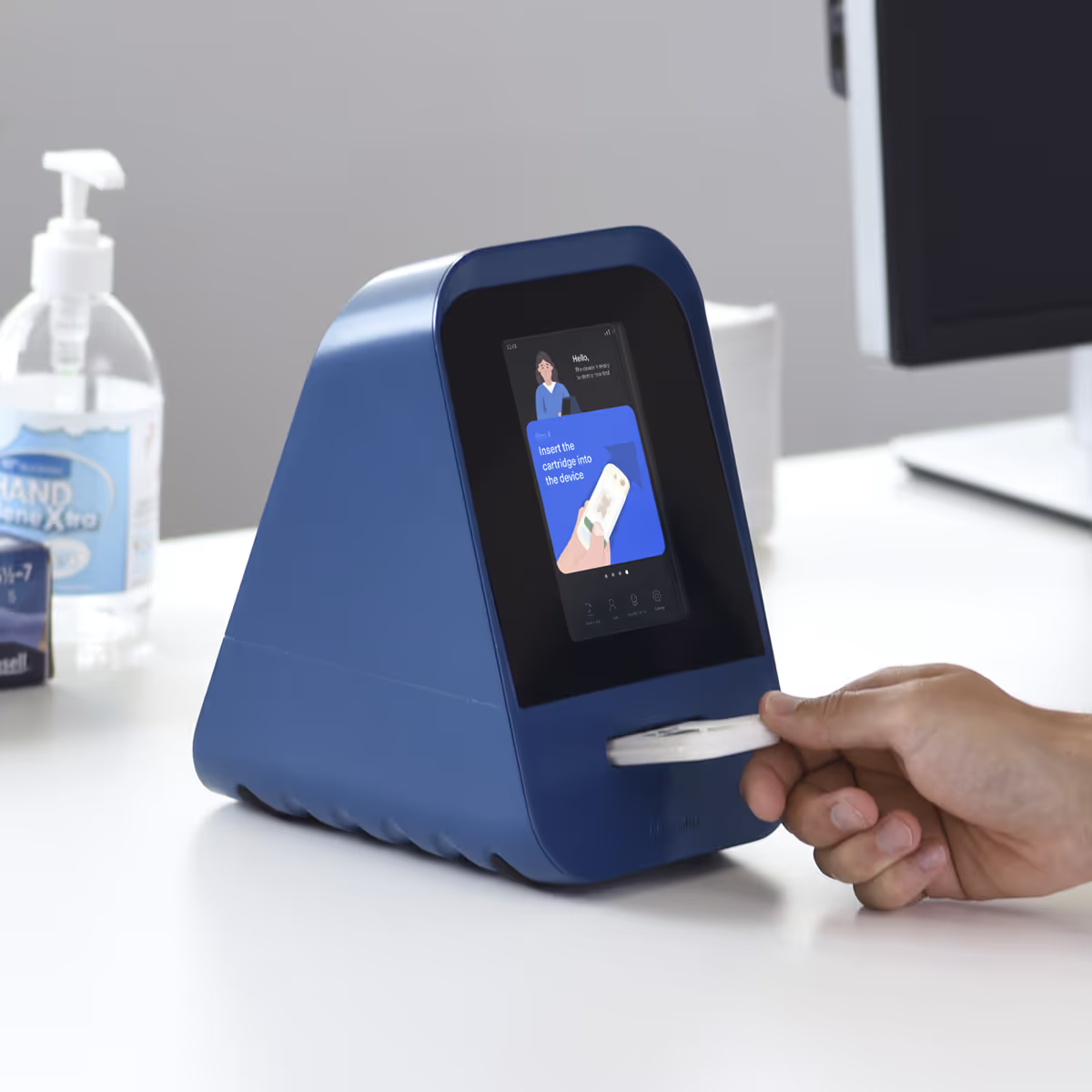
Phase 4: Design Verification
Design Verification formally tests all technical requirements on representative products to prove their capabilities. TTP's success in verification comes from our distinctive 'progressive testing' approach in Phase 3. By this stage, we already know how to test the requirements effectively and have confidence that the design meets them.
As a result, verification - supported by and compliant with the QMS - then becomes a formal demonstration built on evidenced confidence.
The TTP MedTech difference
Since verification testing is typically a strict and structured process in most organisations, with limited flexibility for making changes at this stage, fixing issues can be challenging and costly. TTP's expertise and approach throughout the entire development process help minimise risks and avoid last-minute trade-offs, making it easier for you to scale up and bring your product to market smoothly. Facing new dose counter regulations, TTP collaborated with AstraZeneca to design a reliable, top-mounted dose counter for the Symbicort® inhaler. Utilising first principles and progressive testing, TTP refined the design iteratively, ensuring it met all regulatory and performance criteria before formal verification, leading to FDA approval on the first submission and annual revenues exceeding $2 billion for AstraZeneca. Read the case study
"TTP have been an invaluable long-term partner for AstraZeneca. They have both the deep expertise and creativity to generate innovative concepts, and the horsepower to accelerate these through design and verification."
Dan Deaton Executive Director, Patient Experience and Innovation at Astra Zeneca
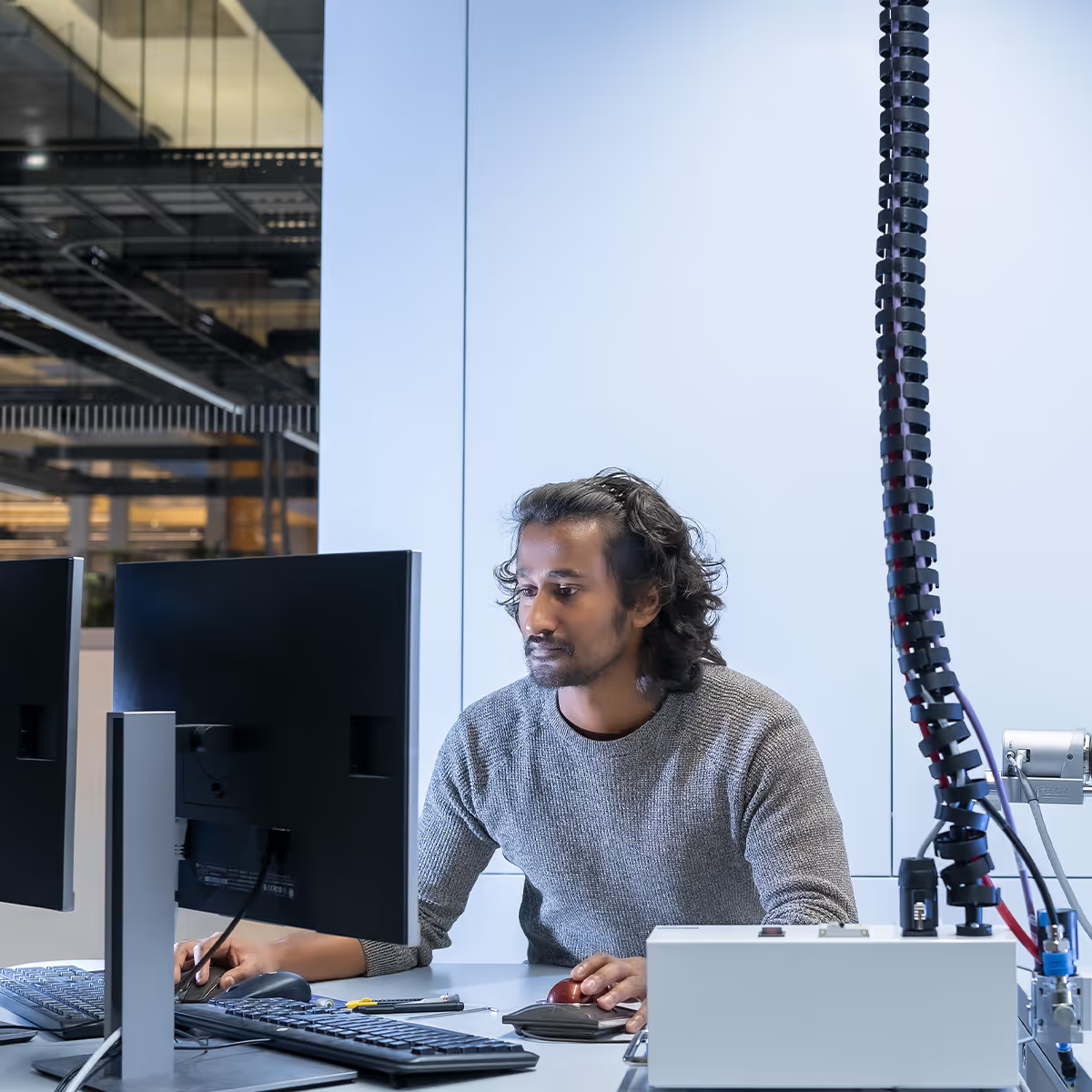
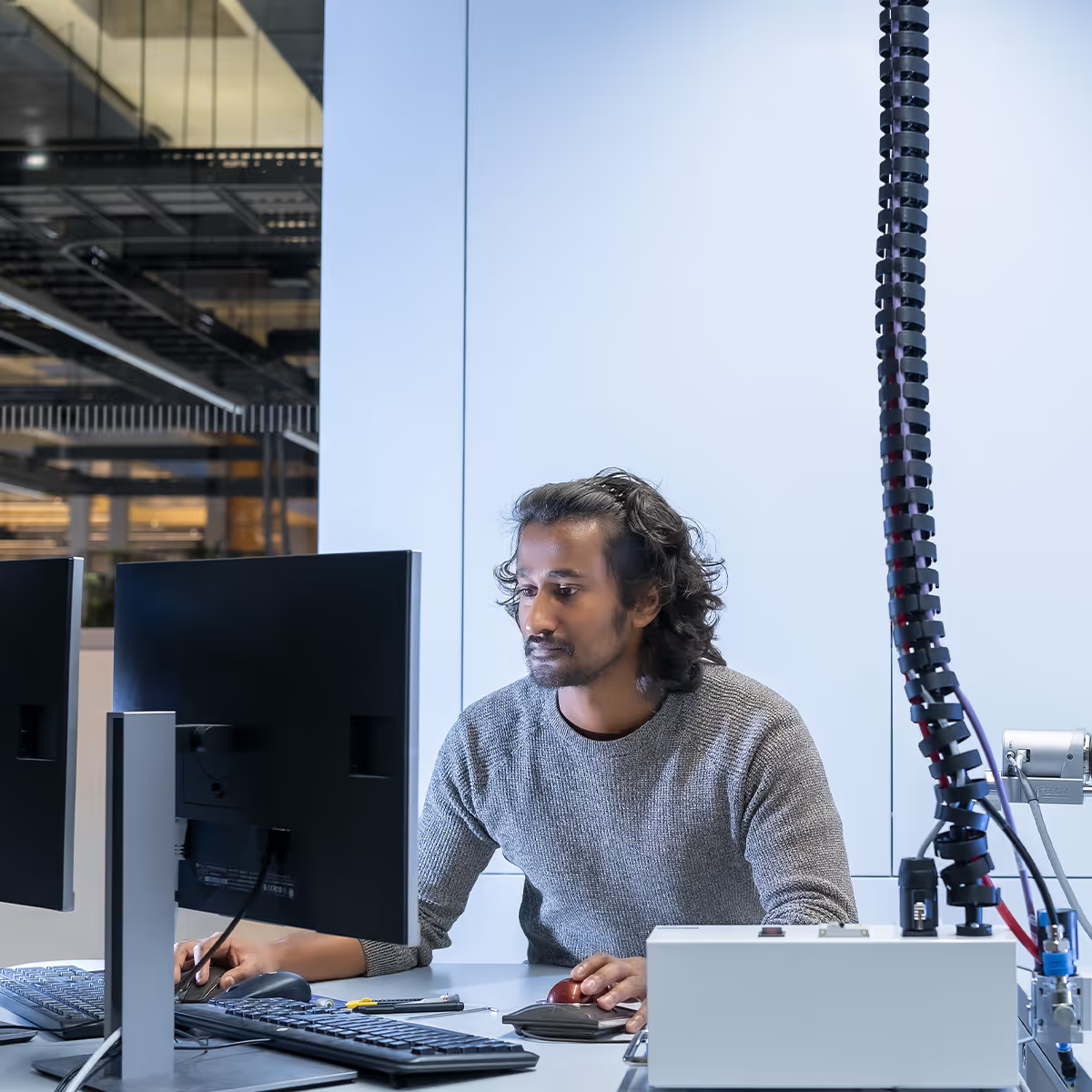
Phase 5: Product Validation
The Product validation phase leads to a demonstrated capability to produce a product in accordance with the design requirements and target production volumes. TTP’s approach builds on the existing dialogue with manufacturing partners, going well beyond sharing design documents and attending knowledge transfer meetings. We typically create process requirement documents covering what each step must achieve for a device to work – without straying into prescribing the process itself.
We create opportunities for teams’ tacit knowledge to be transferred, such as hands-on co-assembly workshops, to mitigate the risk of misunderstanding. We frequently support in-process check development, line qualification, and process validation with our established experimental approaches, as well as design understanding.
It's important to be aware that the timing of this phase compared to other depends on the product and your manufacturing strategy, amongst other factors.
The TTP MedTech difference
TTP's Medical Device Development Consulting capabilities ensures a seamless transition from prototype to production. By working with manufacturing partners from the start, TTP helps prevent major issues. Our clear communication of design insights ensures your other partners can contribute their expertise without unnecessary restrictions, reducing the risk of delays later on. For nearly 40 years, our MedTech and Drug Delivery design and development consulting team - comprising 300+ engineers, scientists, and human factors specialists - has collaborated with clients to develop innovative solutions that drive commercial success, from early concept development through to manufacturing transfer. Find out how we can help you. Learn more.
Our areas of focus:
Medical Devices & Drug Delivery
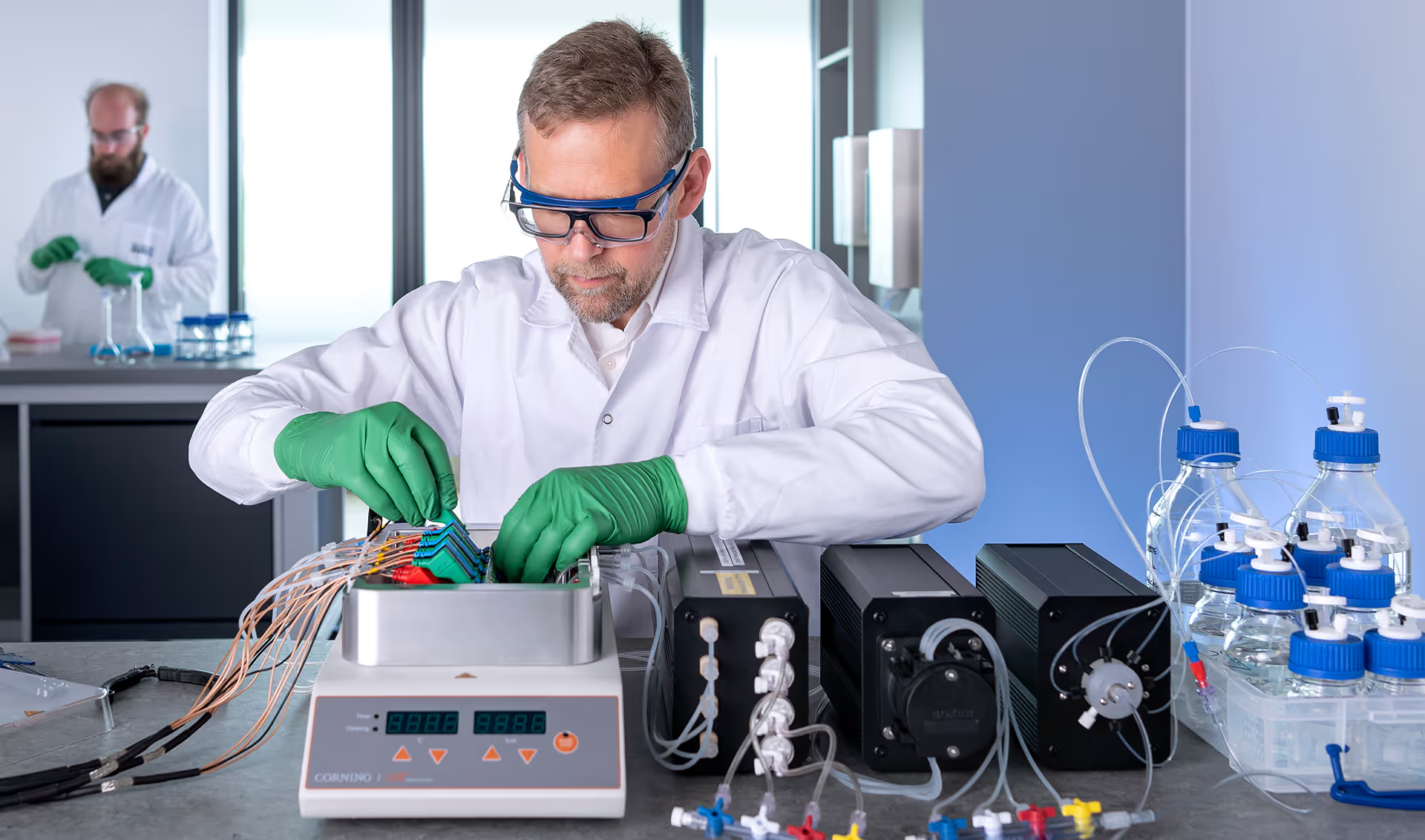
“The modelling phase is an area where TTP has excelled in producing unique applications to our problems. TTP engineers developed laboratory test beds that verified the modelling process and provided the ability to test theorized solutions without the need to do full-scale pilots. By narrowing down proposed solutions first by modelling and then on a test bed we could focus on a few key possibilities in our manufacturing environment, saving time and resources in this critical area.”
Chuck Lynch
Senior Engineering Manager
,
Roche Diagnostics
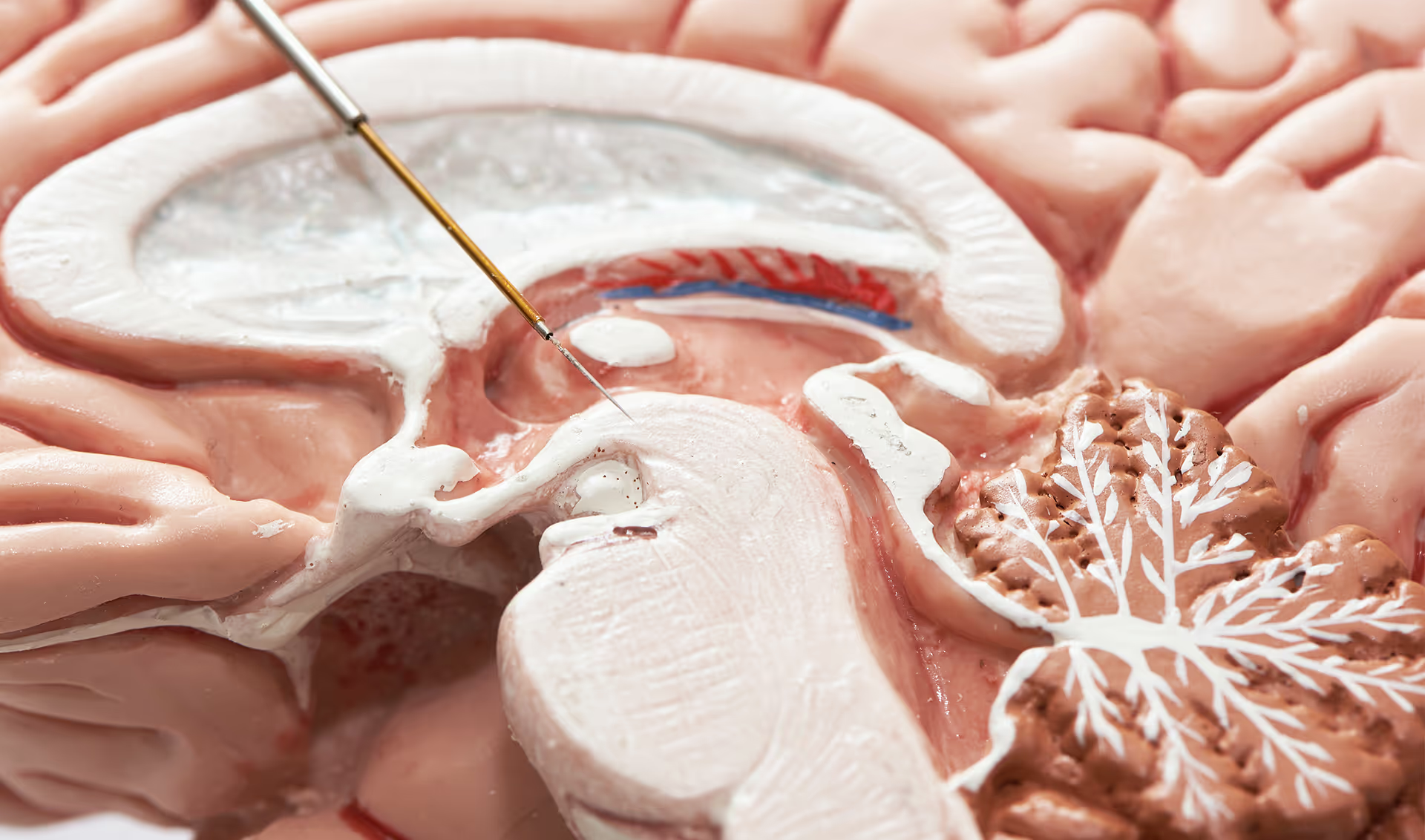
“TTP has been exceptional to work with. They are sharp and experienced and were able to quickly adapt to changing business needs. They are clearly expert at what they do, which made our job easier. We felt we could trust them to do the job right and communicate results clearly. They were also fun to work with, having laid-back styles and engaging personalities. I’d highly recommend TTP and will definitely use them in the future if the need arises!”
Meredith Seaborn
Director of New Therapies, Marketing and Neuroscience
,
Medtronic
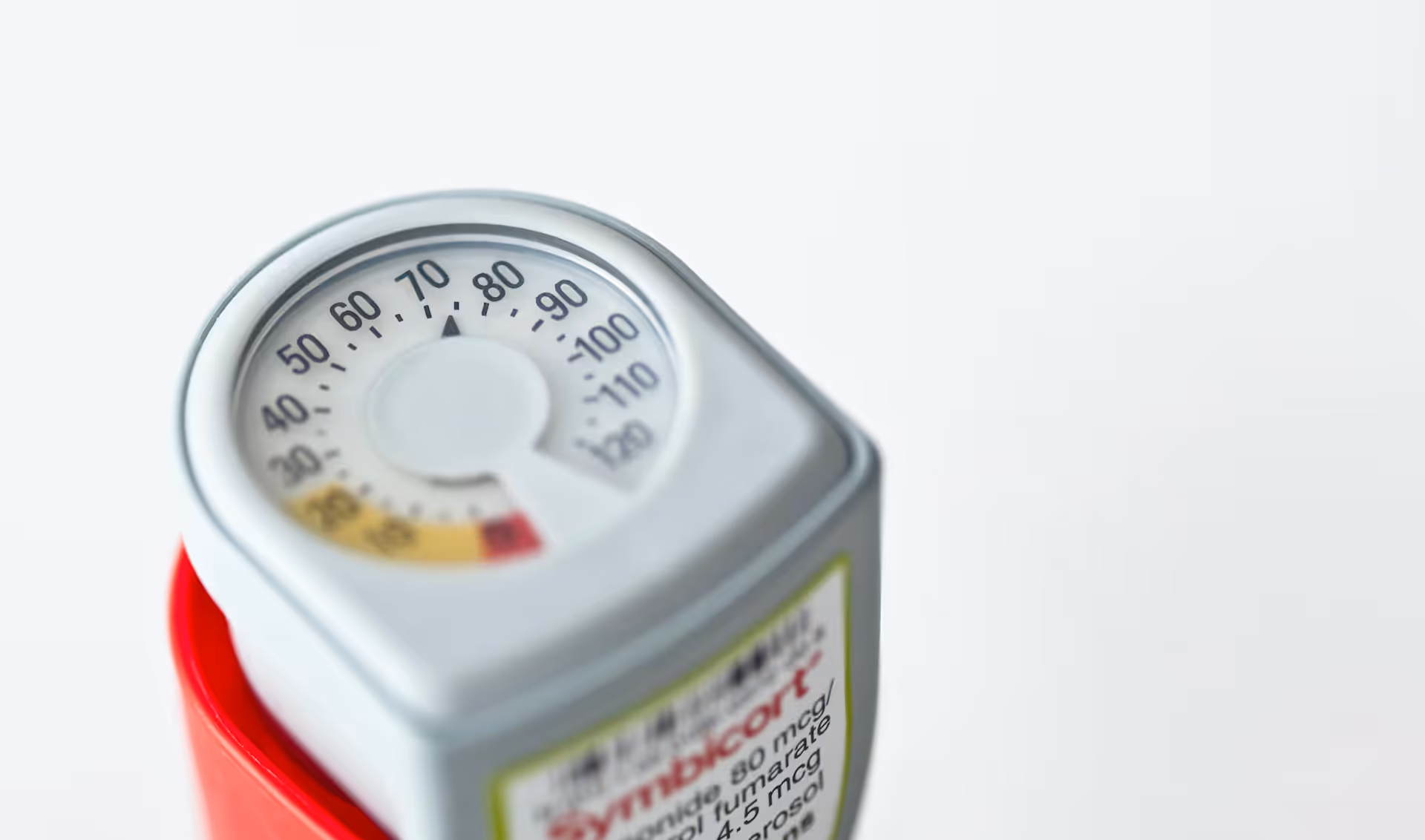
“TTP have been an invaluable long-term partner for AstraZeneca. They have both the deep expertise and creativity to generate innovative concepts, and the horsepower to rapidly accelerate these through design verification.”
Dan Deaton
Executive Director, Patient Experience and Innovation
,
AstraZeneca
Our approach and capabilities
We deliver across the entire life of a project, from opportunity discovery to production engineering. Discover how our interdisciplinary teams of experts collaborate to tackle the toughest product development challenges.
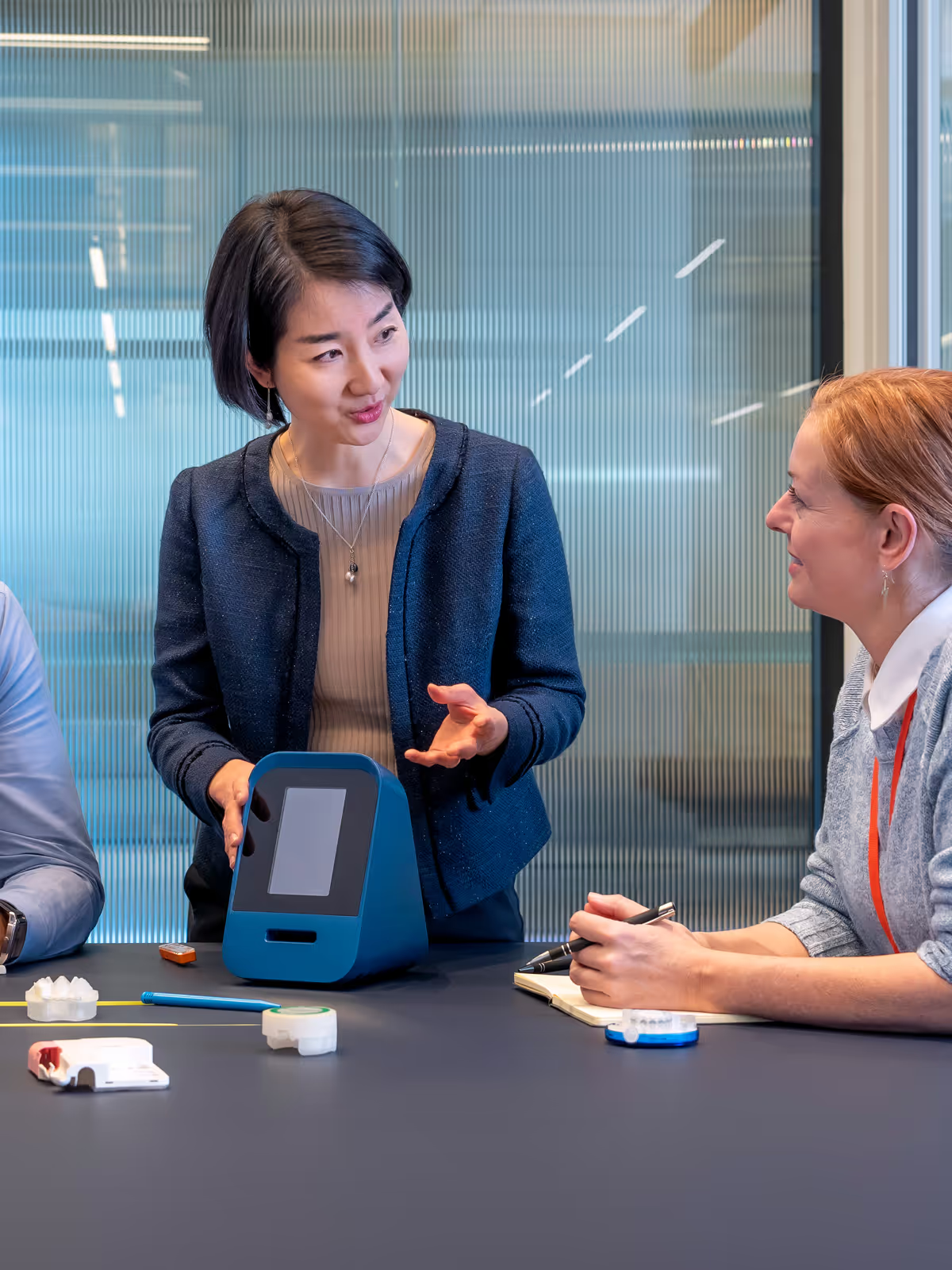
Our campus and facilities
Our award-winning campus has been designed with a clear vision. To create space which can suport our people and our clients as we develop and deliver the very best technology solution.
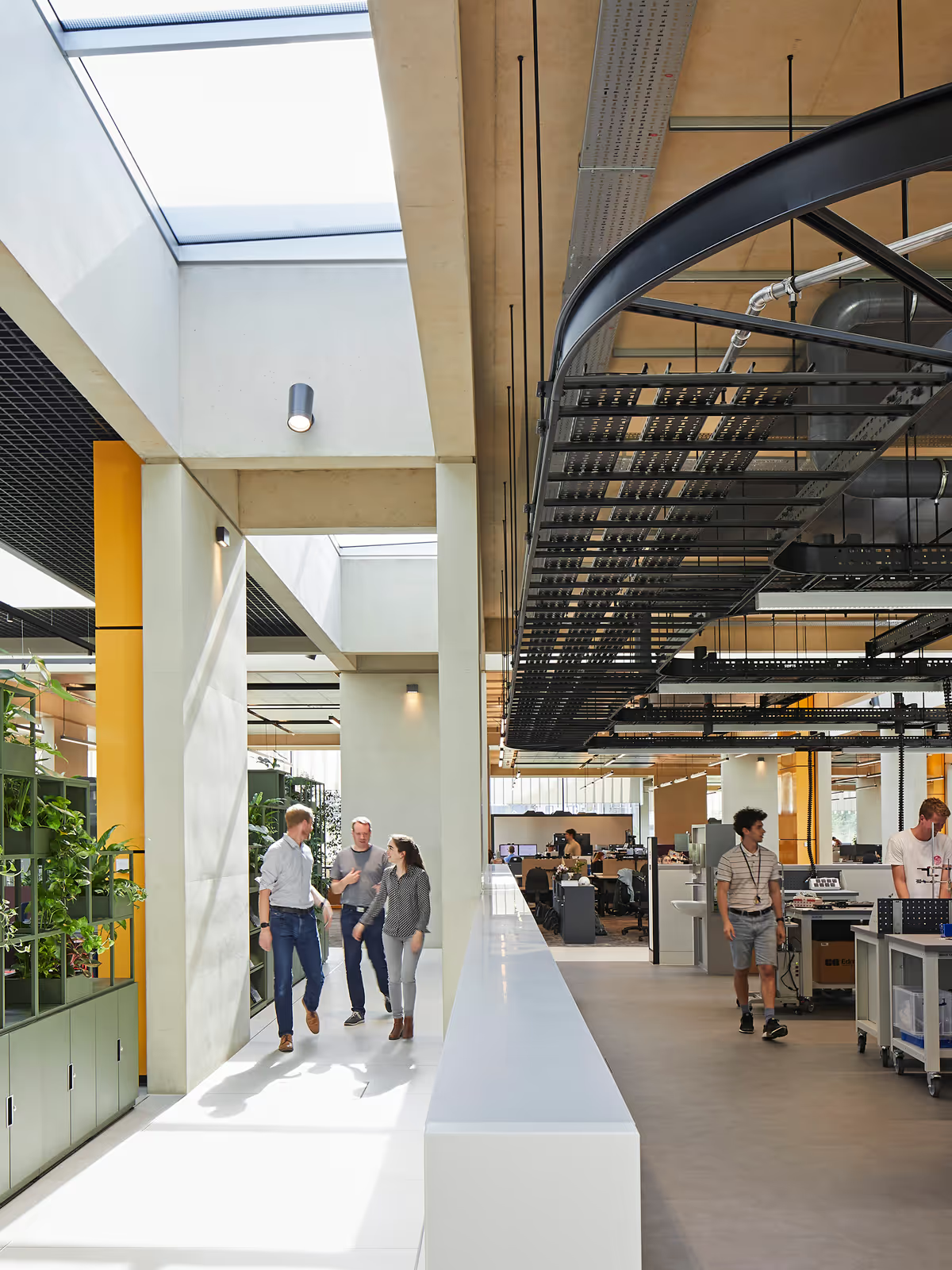
Software capability at TTP
Engaged in all stages of software and product development, our software capability at TTP covers the full spectrum—from in-depth analysis and system architecture to prototype design, implementation, and test development.
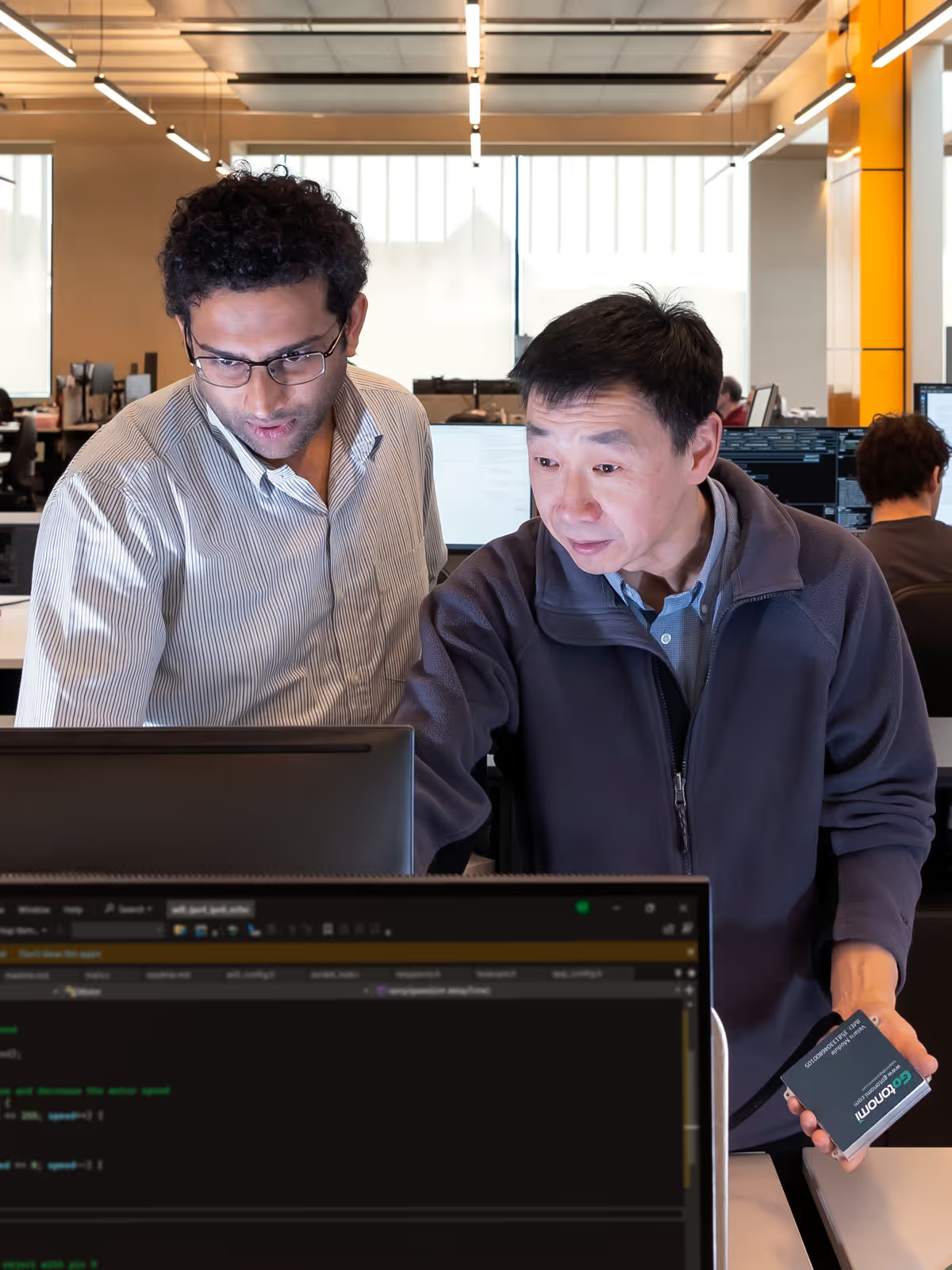
Manufacturing capability at TTP
Working seamlessly with our development teams, we take clients' products through prototype builds, clinical trials, pilot manufacture and more. Using TTP Manufacturing reduces uncertainty, risk and time to market for our clients.
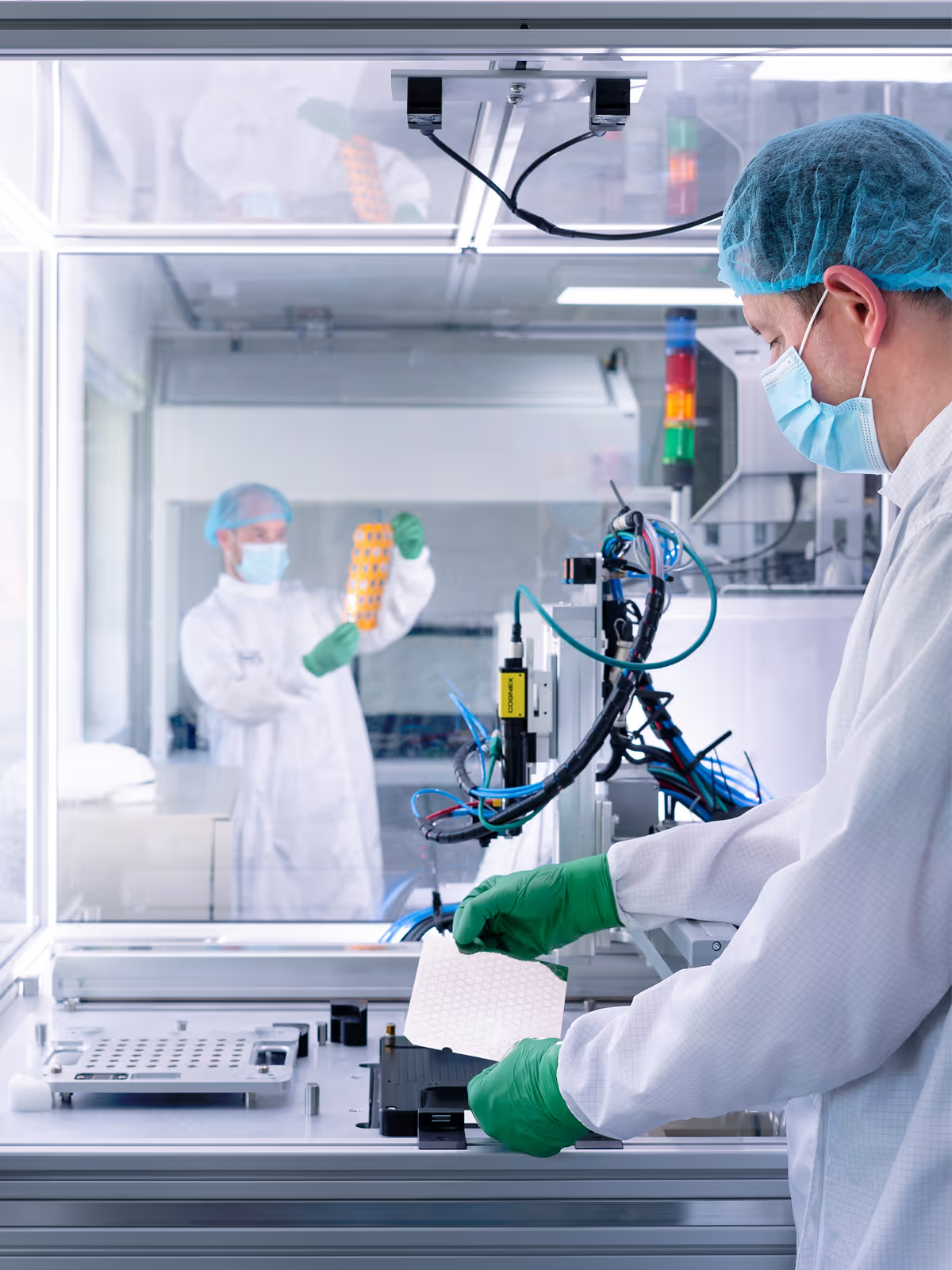
Meet some of the team
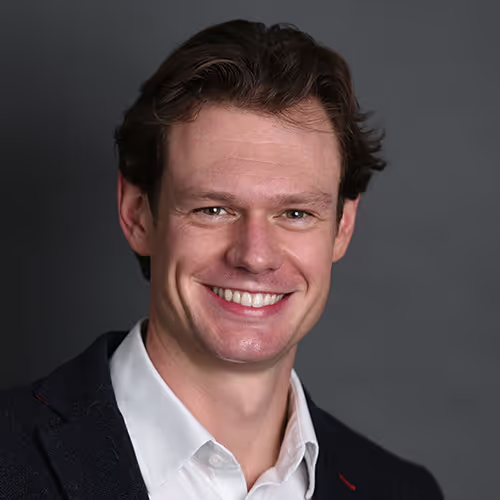
Harry Bullivant
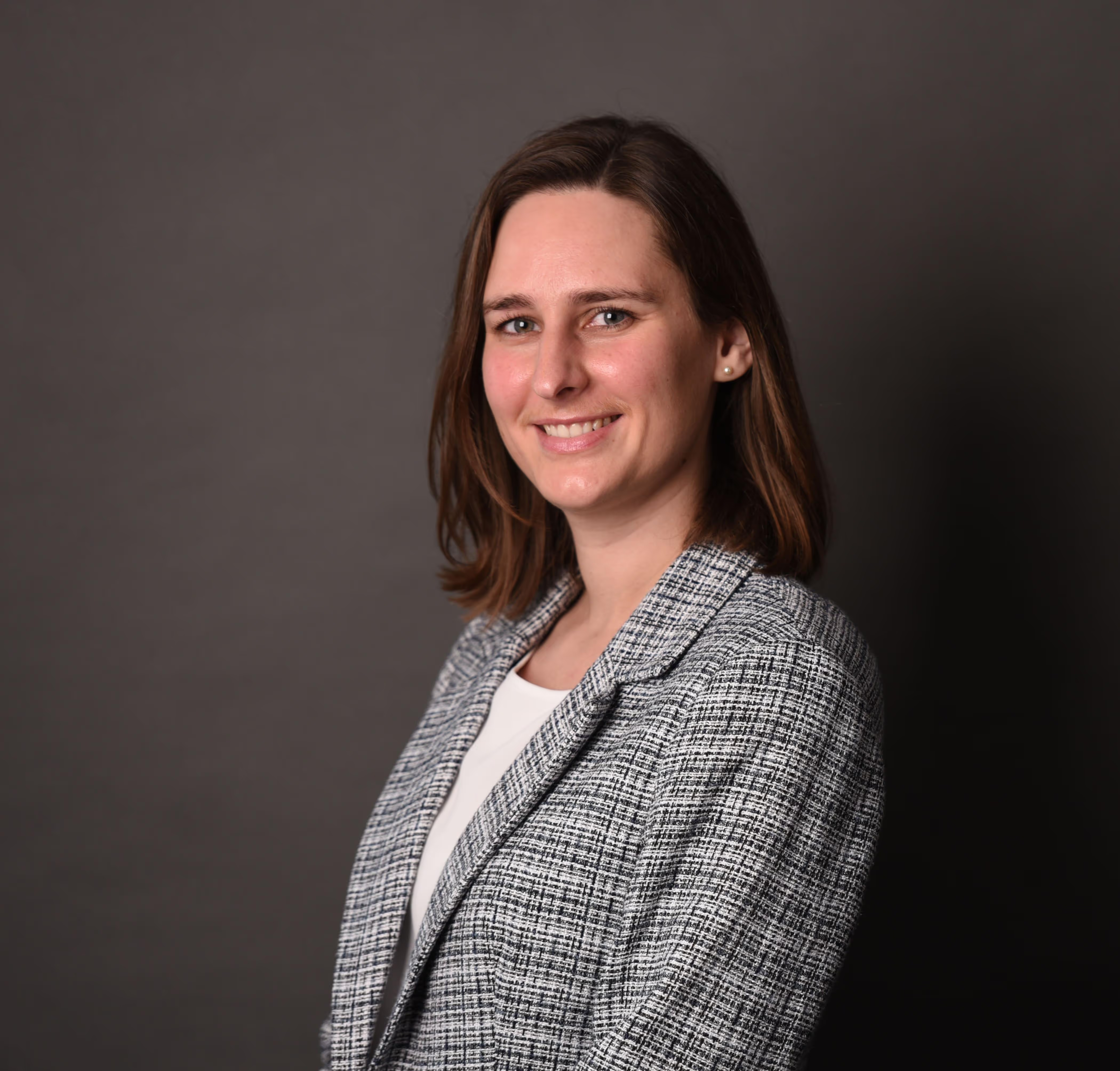
Hannah Claridge
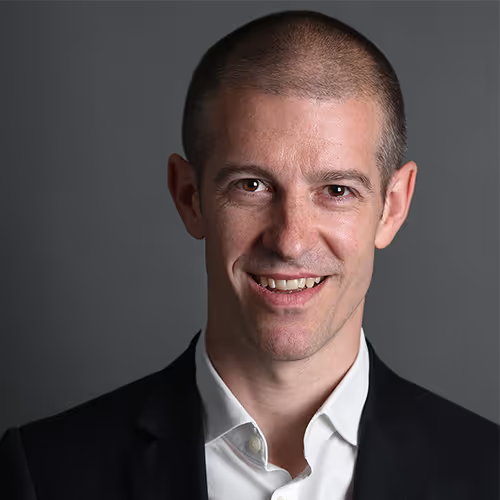
Chris Dawson
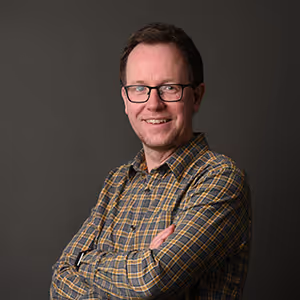
Steve Gowers

Paul Galluzzo

Catherine Wyman
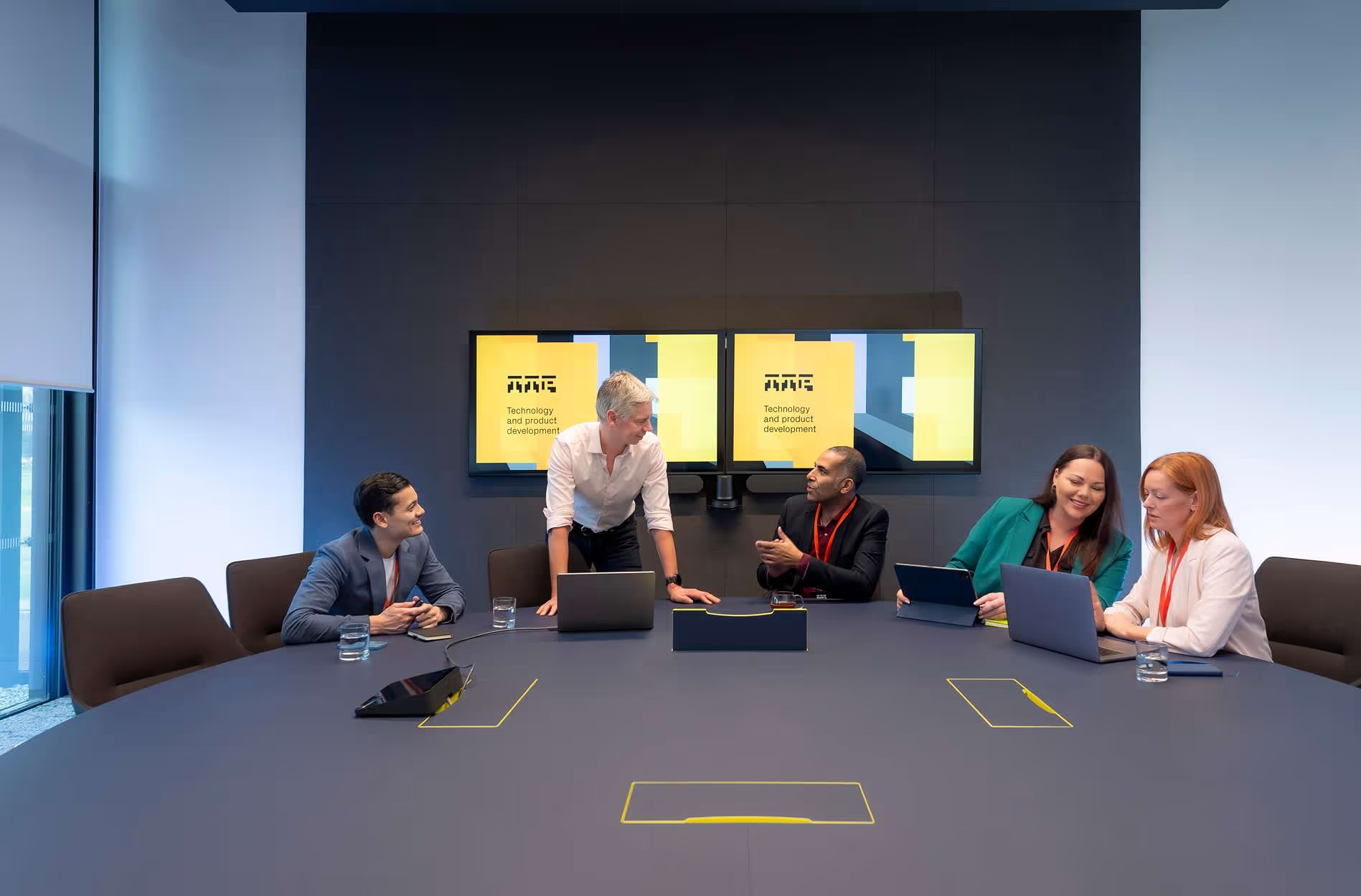