TTP has developed an automated CGM sensor testing platform that helps novel CGM sensors reach the market with ease.
Context:
Progressing the development of a novel CGM sensor to the point where it can improve the quality of life for millions of people with diabetes is a tall order. For confidence that the sensor will be accurate enough to meet FDA requirements, even the in vitro testing calls for significant rigour.
Solution:
To take the place of unreliable manual sensor testing, TTP has developed an automated CGM sensor testing platform that meets the needs of characterising a novel CGM sensor, developing manufacturing processes and generating data to support regulatory submissions.
Result:
With TTP’s automated CGM sensor testing platform, companies commercialising novel CGM sensing technology can focus on core development activities, assured in the knowledge that rigorous and methodological testing to support device characterisation and manufacturing scale-up is in place.
Download the white paper
To find out how our system can accelerate the development of your CGM, download the white paper. Download white paper
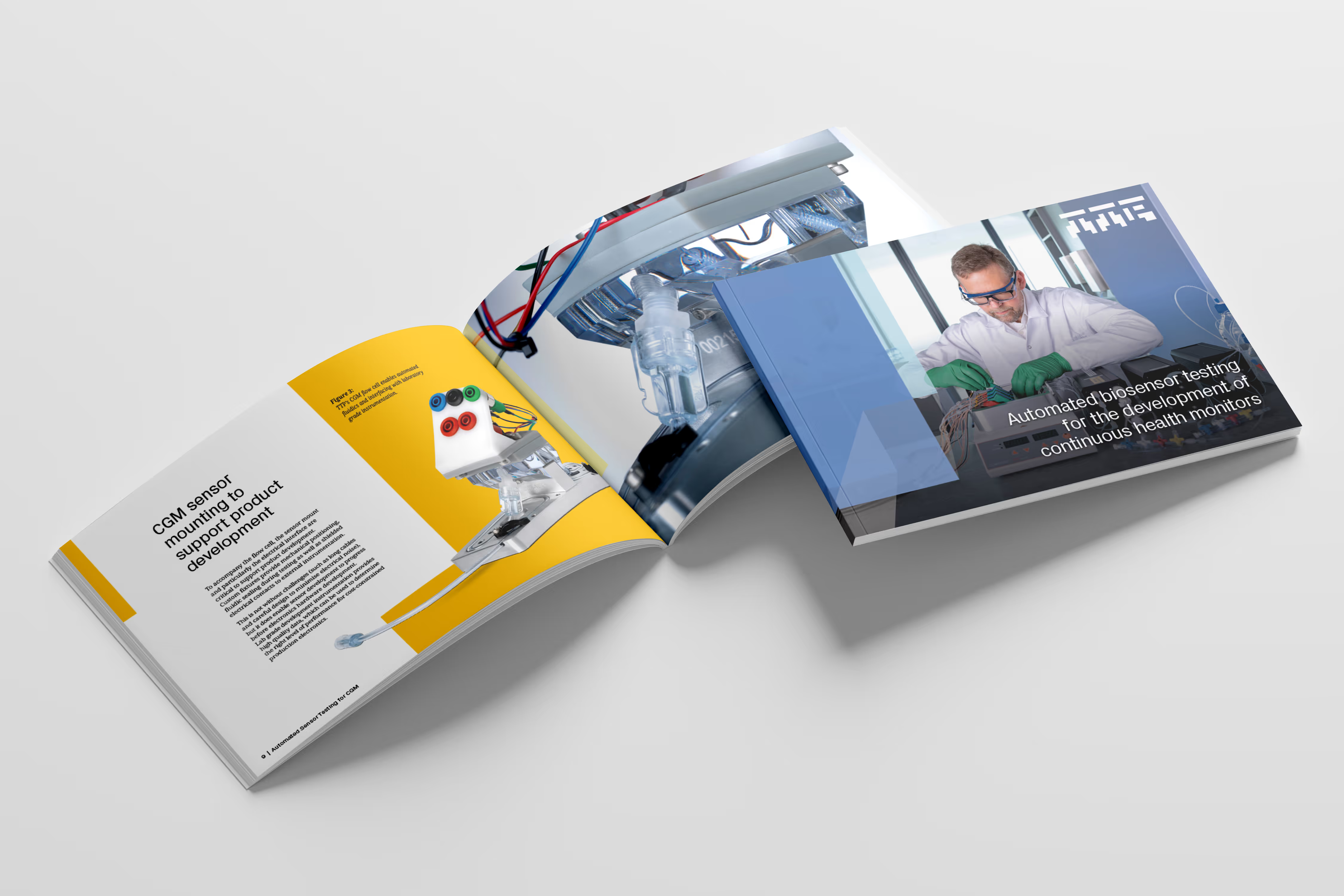
Sooner rather than later, the testing of a new continuous glucose monitoring (CGM) sensor will require more than manual procedures and standard lab equipment.
That’s because, before long, you may be testing hundreds or thousands of sensors over months, if not years, depending on whether the sensor is destined for a short-term wearable or an implantable CGM.
A single sensor could generate 100,000 data points per week, and that data will support not only the design of your prototype but also the development of reliable manufacturing processes and, eventually, regulatory submissions. With this roadmap in mind, one can’t contemplate a test rig or data handling that is inefficient at best and at worst unreliable.
Automated CGM sensor testing
At TTP, we support a wide range of development testing, from drug delivery devices to lab diagnostics.
We’ve thought carefully about the CGM development testing workflow and best practice from other areas to create a flexible system that addresses the challenge of manual operation, test rig reliability, and inefficient data management often seen during sensor development.
Expandable fluidics platform
The core of the system is a robust fluidic platform that runs repeatable test sequences with an expandable number of sensors and test liquids.
During long-term sensor testing, the system can automatically switch between through-flow, for calibration checks with rapid concentration changes, to recirculation, to assess sensor drift while preserving test solutions.
The flow cell in our system has been designed for the specific needs of CGM sensor testing. It guarantees rapid changes in glucose concentrations to reveal the intrinsic response time of the sensor.
To accompany the flow cell, the sensor mount and particularly the fluidic and electrical interfaces are critical to the reliability of the test system. Custom fixtures provide secure mechanical positioning, fluidic sealing as well as shielded electrical contacts to external laboratory grade instrumentation. This is not without challenges, but it does enable sensor development to progress ahead of electronics hardware development.
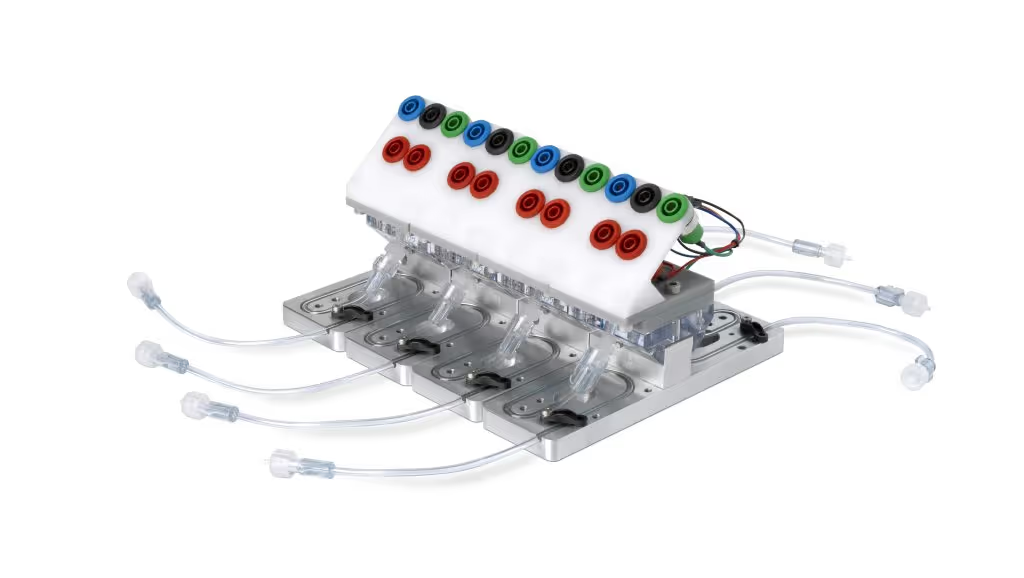
Developing your manufacturing process
When developing a novel CGM sensor, you are inevitably also honing a new manufacturing process. Testing capability is key to selecting the best designs and process conditions, and building up a good understanding of the reliability and manufacturing repeatability of your sensor.
For this, it’s essential to not only capture sensor outputs but to associate them with related data, starting with the sensor IDs (linked to design and manufacturing records), test fluids (with composition and batch traceability), test protocols and test rig configuration.
Analytics made simple
Our CGM sensor testing platform comes with a flexible MongoDB database that links all this information to create secure, complete and accessible test records. Time-series sensor output data are automatically synchronised with fluidic and temperature logs.
One powerful feature of the database is the ease of carrying out virtual experiments: mining existing datasets to answer new questions that inevitably arise.
For example, what was the impact of a change, whether deliberate or unintentional, in the manufacturing process? This system makes the data available to query and provide evidence, facilitating rapid and conclusive resolutions.
Ultimately, the database provides a secure repository for the data that supports your regulatory approvals.
What's next?
Establishing CGM sensor testing capability and data management is a major development activity. And any time spent establishing this test capability is time not spent on developing your innovative sensor.
Nonetheless, the reality is that bringing a novel CGM sensor to market will depend on both – core sensing technology and systems to support characterisation and scale-up. That’s why we have taken the initiative to establish a robust test system to help novel CGM sensors reach the market with ease.
About TTP’s Biosensing Consulting Team
Specialising in the development of wearable and implantable biosensors, TTP’s Biosensor product design and development consultants deploy multidisciplinary teams, combining expert capabilities to deliver tailored solutions that meet the most demanding project requirements.
Whether navigating uncharted territories, supporting your next innovation or accelerating time to market, we solve complex challenges with engineering and scientific rigour, finding and retiring risks early to deliver high-impact, human-centred results. When your internal bandwidth is constrained, TTP is ready to deliver.
Read more about how we are accelerating continuous glucose monitoring design and development.
TTP's Biosensing team is part of our broader Medical Device Consulting business unit, consisting of 300+ engineers, scientists, and human factors specialists. For nearly four decades we've partnered with clients to develop impactful solutions, helping them achieve commercial success. See our approach to medical device design and development.