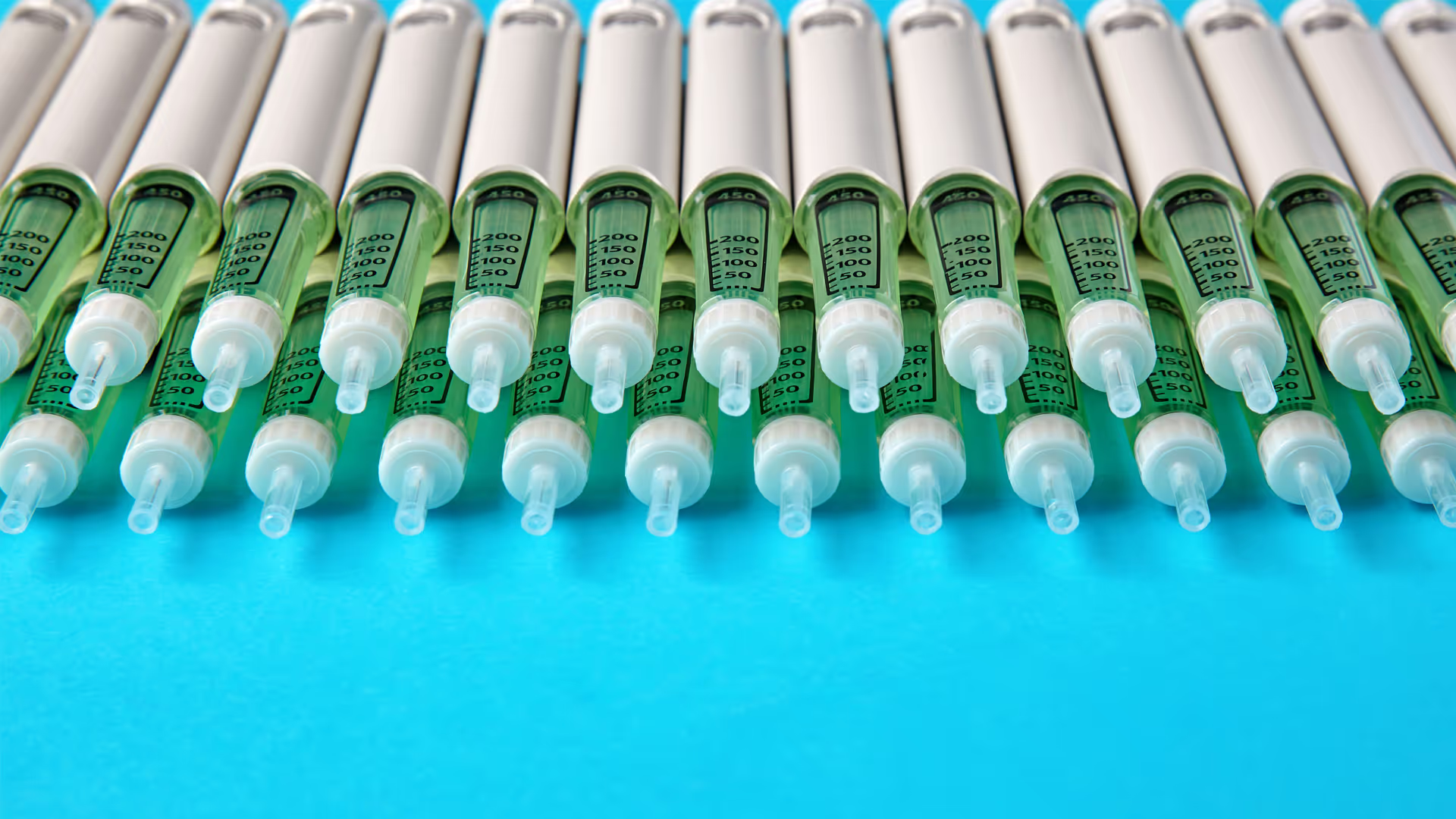
Designing drug delivery devices for scalability
Bringing a new drug to market demands more than just a functional delivery device – it needs to scale seamlessly.
But scaling a delivery device from prototype to production is one of the most complex challenges in drug development. It requires foresight, precision, and a deep understanding of how design decisions impact manufacturability. Addressing scalability early – from materials to automation compatibility – minimises risks and ensures smoother transitions. Teams that prioritise scalability from the outset set themselves up for success when the stakes are highest.
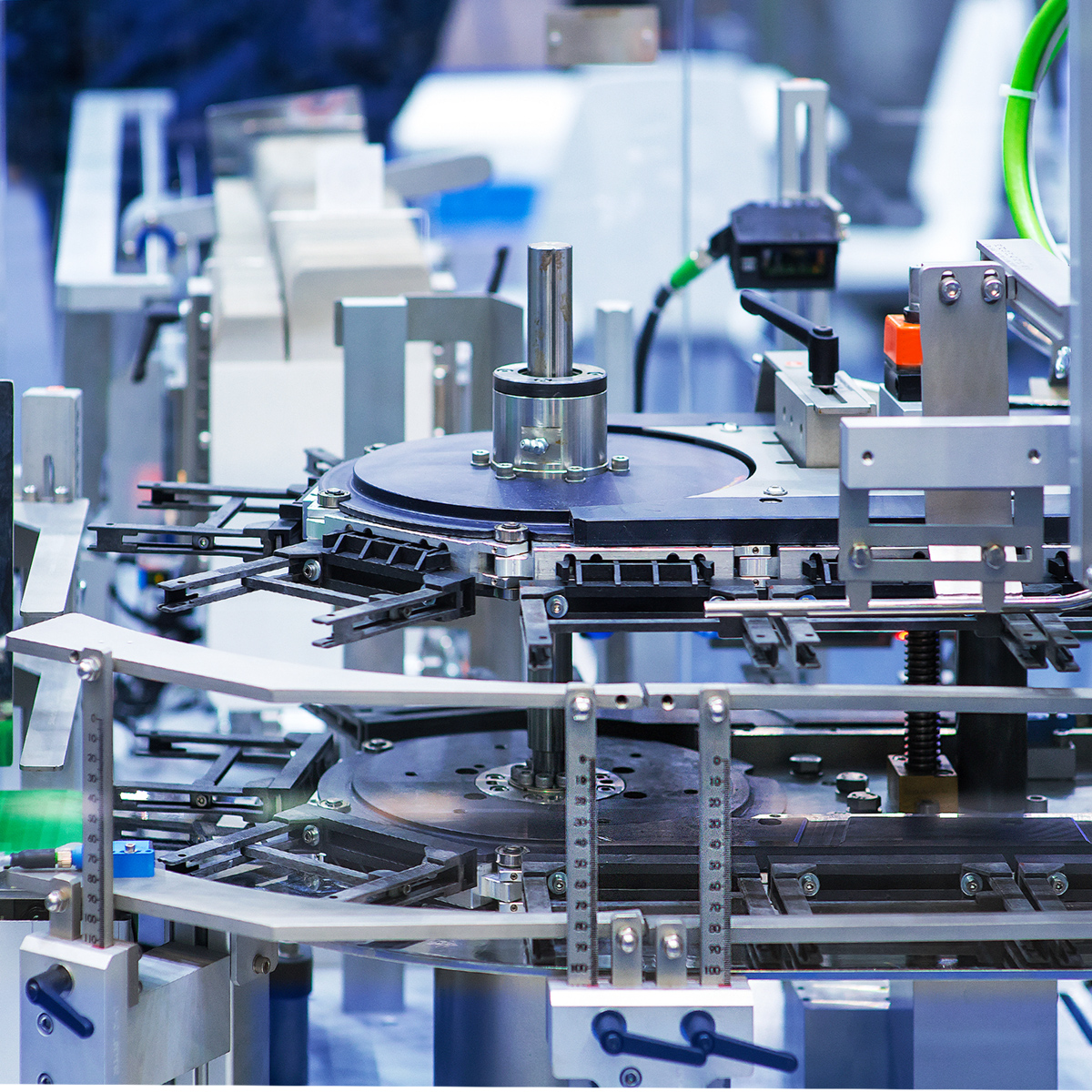
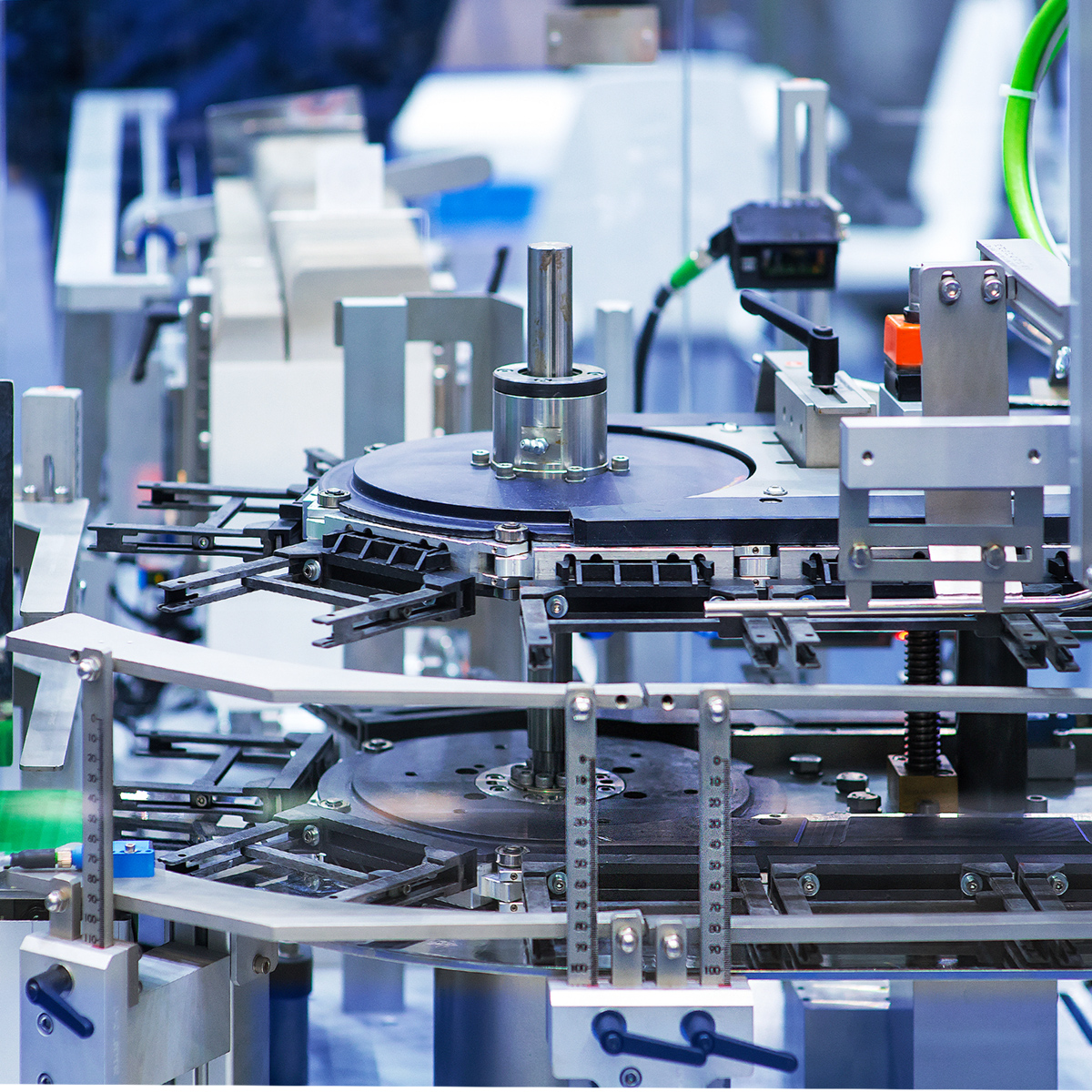
Creating predictability in an uncertain process
Few things are as expensive to develop as new drugs. With on-patent time all too short, every day on the market represents millions in value. That makes it critical for delivery devices to be ready for the drug product, not stuck in pre-production, held back by stubborn automation issues.
An utterly predictable medical device design and development process, from design through scale-up to full-scale production, is the ideal. Achieving this requires a framework to anticipates bottlenecks, adapt to challenges, and integrate scalable processes to avoid costly delays.
It also means ensuring a seamless design transfer, where every decision aligns with both manufacturing requirements and the realities of large-scale production.
Missed opportunities for alignment early on can cascade into significant setbacks down the line, compounding costs and delays.
But how do you turn the inherent uncertainty of R&D into something as dependable as a trip to the grocery store?
The answer lies in knowledge, experience, and most importantly, creative problem-solving. It’s about combining technical rigour with strategic foresight to not only navigate the unknown but to master it.
Find out how TTP's Drug Delivery product development team can support your product ambitions.
Meet us at
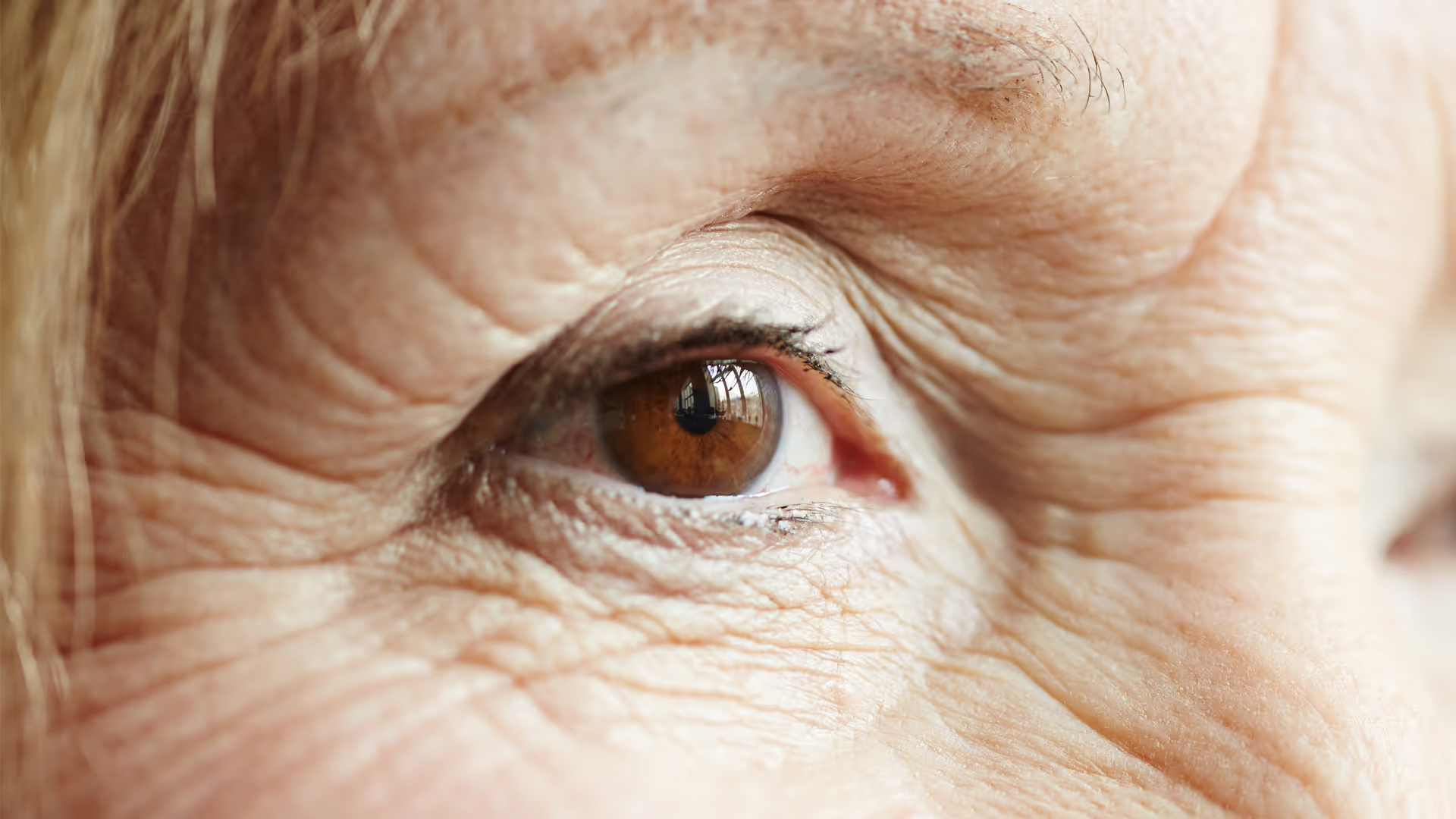
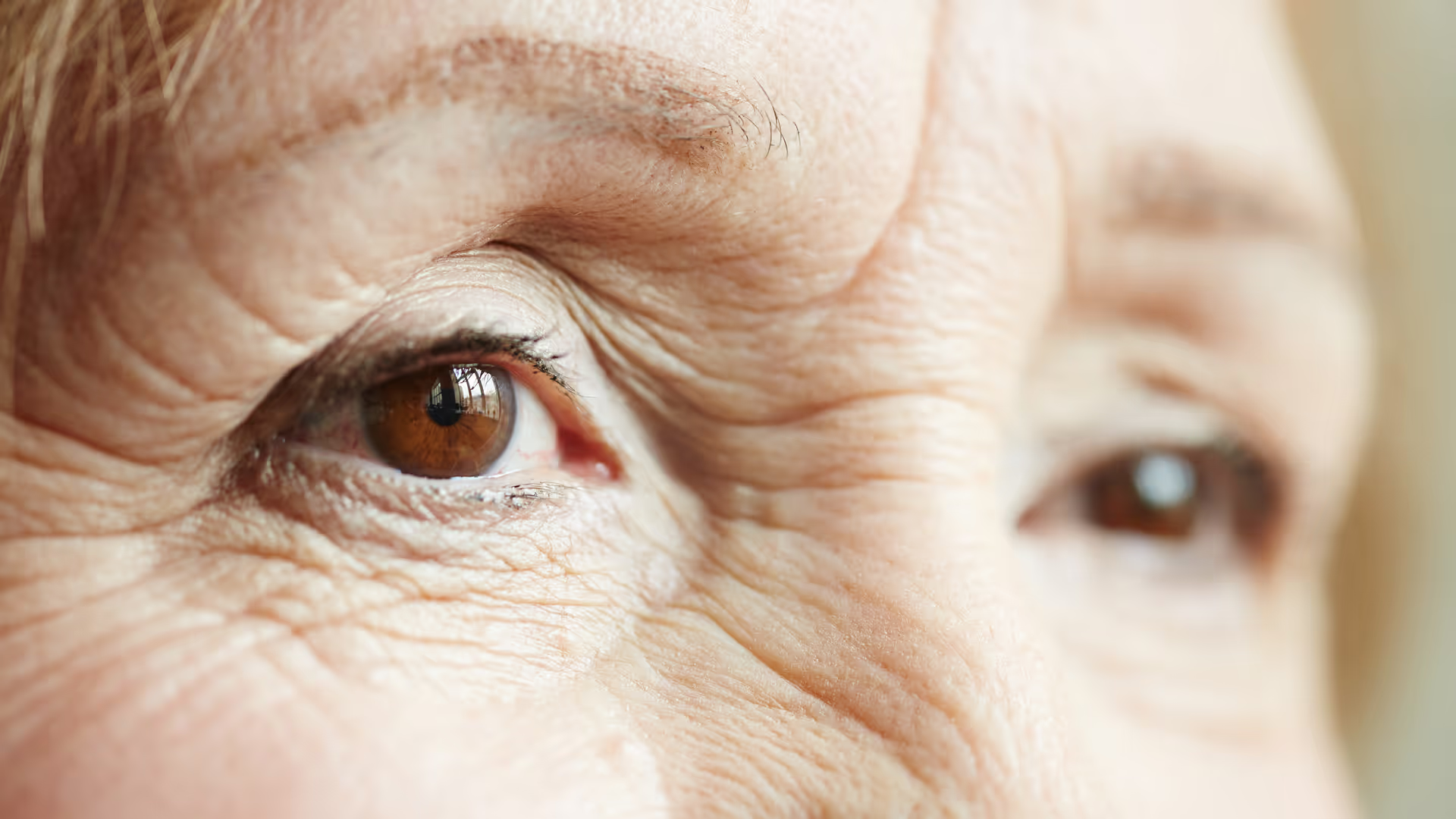
We approached TTP to help us de-risk several of our delivery device concepts. The analysis and concepts generated were well thought out and detailed, allowing us to make risk-based decisions to guide the projects. In one instance, their analysis steered us away from a concept that would have been quite costly to prove reliability. TTP’s expert approach to problem solving is evident as the team was able to meet all deliverables within the agreed budget and timeline. The service we received exceeded expectations and we plan to work with TTP on future projects.
Ian Parrag
Vice President of R&D at Ripple Therapeutics
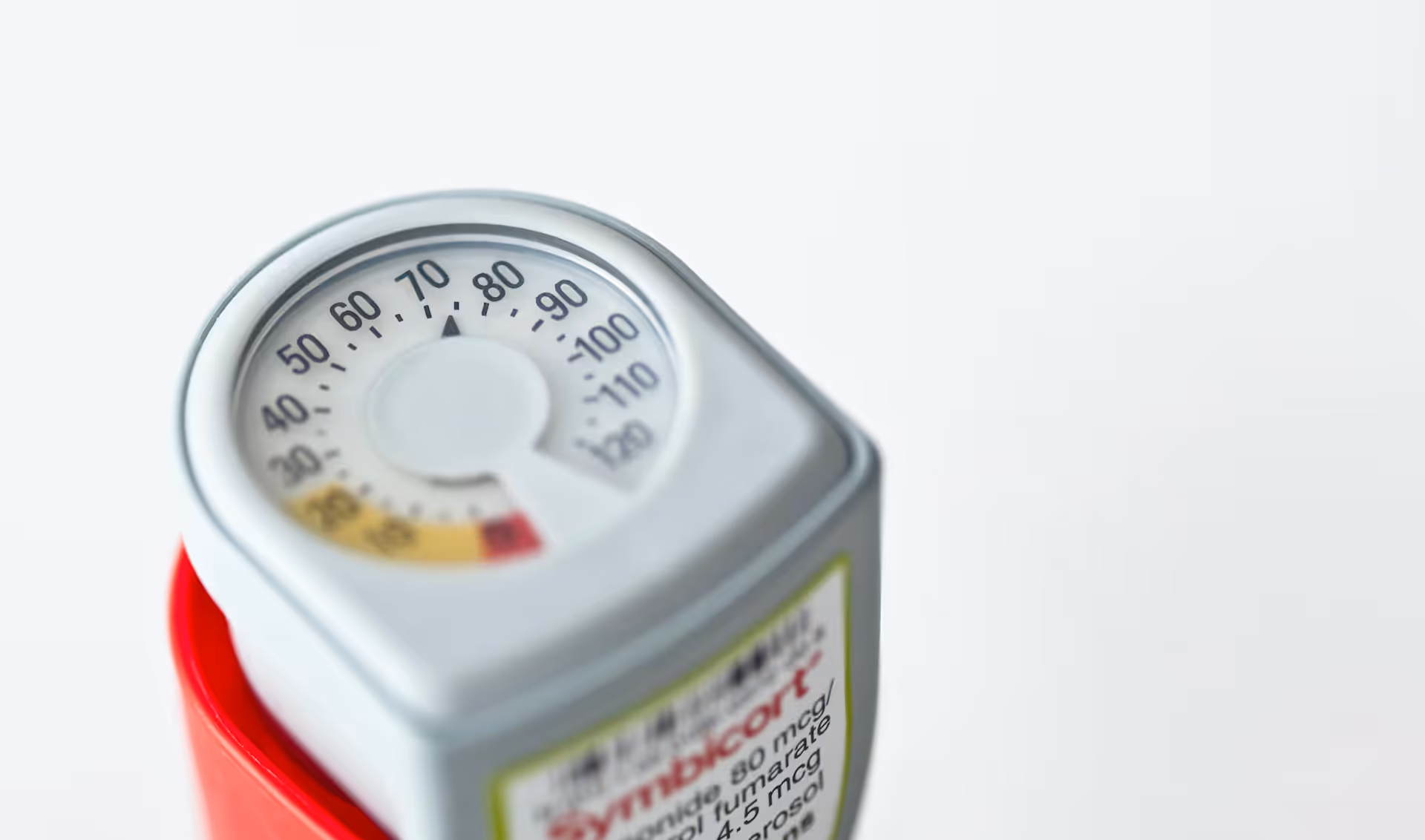
TTP have been an invaluable long-term partner for AstraZeneca. They have both the deep expertise and creativity to generate innovative concepts, and the horsepower to accelerate these through design verification.
Dan Deaton
Executive Director, Patient Experience & Innovation at AstraZeneca
Our areas of focus:
Medical Devices & Drug Delivery
Our approach and capabilities
We deliver across the entire life of a project, from opportunity discovery to production engineering. Discover how our interdisciplinary teams of experts collaborate to tackle the toughest product development challenges.
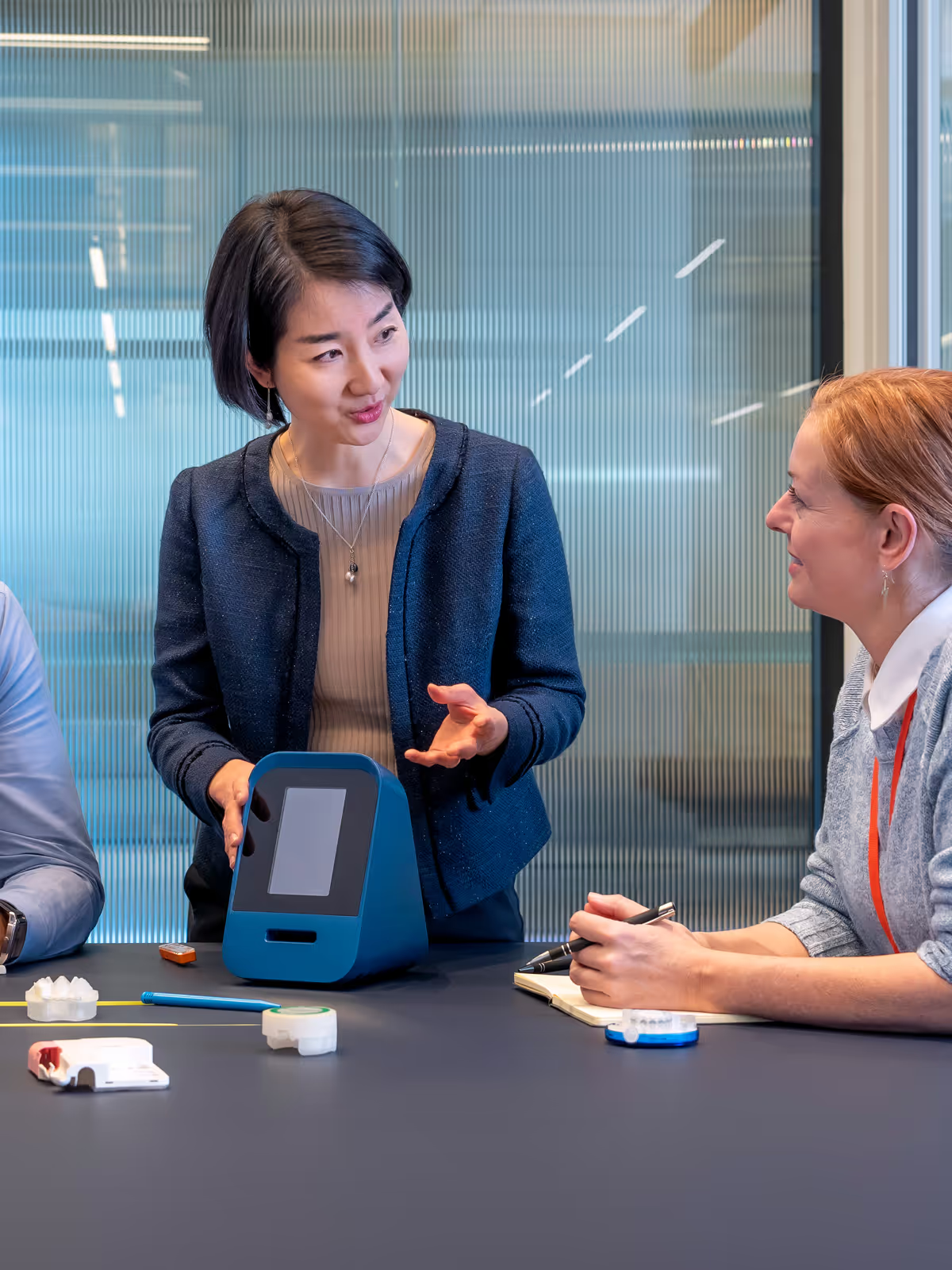
Our campus and facilities
Our award-winning campus has been designed with a clear vision. To create space which can suport our people and our clients as we develop and deliver the very best technology solution.
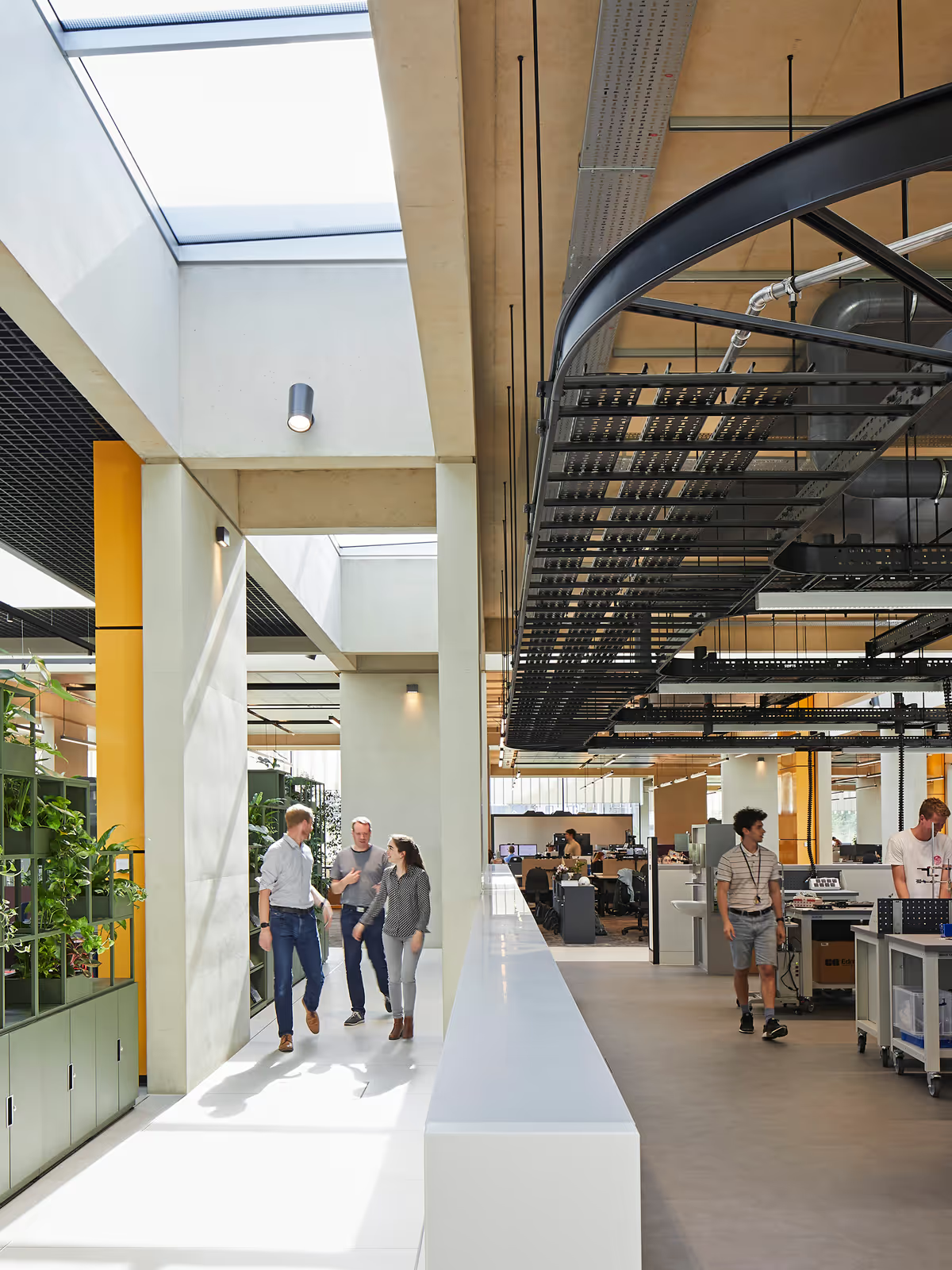
Software capability at TTP
Engaged in all stages of software and product development, our software capability at TTP covers the full spectrum—from in-depth analysis and system architecture to prototype design, implementation, and test development.
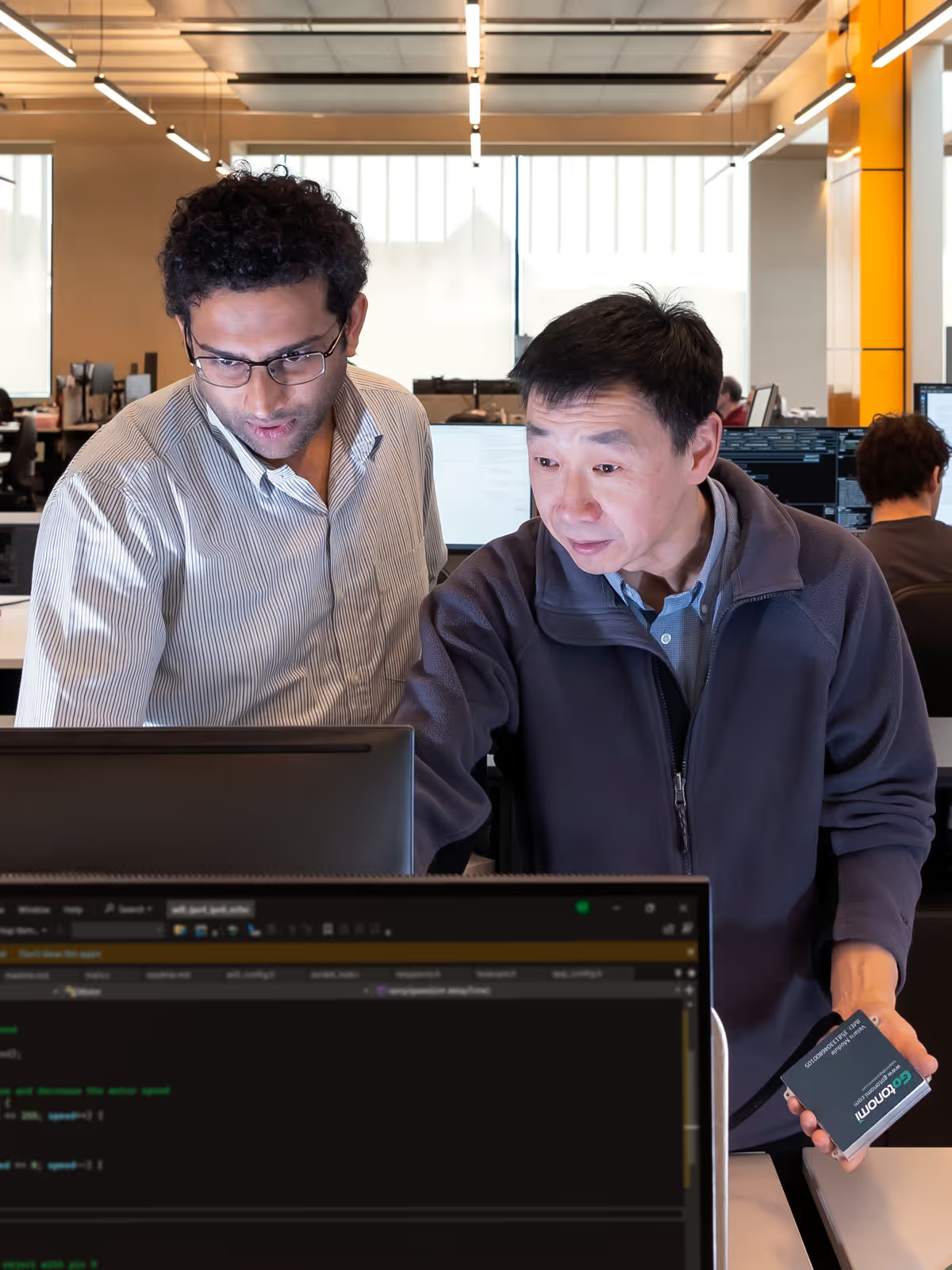
Manufacturing capability at TTP
Working seamlessly with our development teams, we take clients' products through prototype builds, clinical trials, pilot manufacture and more. Using TTP Manufacturing reduces uncertainty, risk and time to market for our clients.
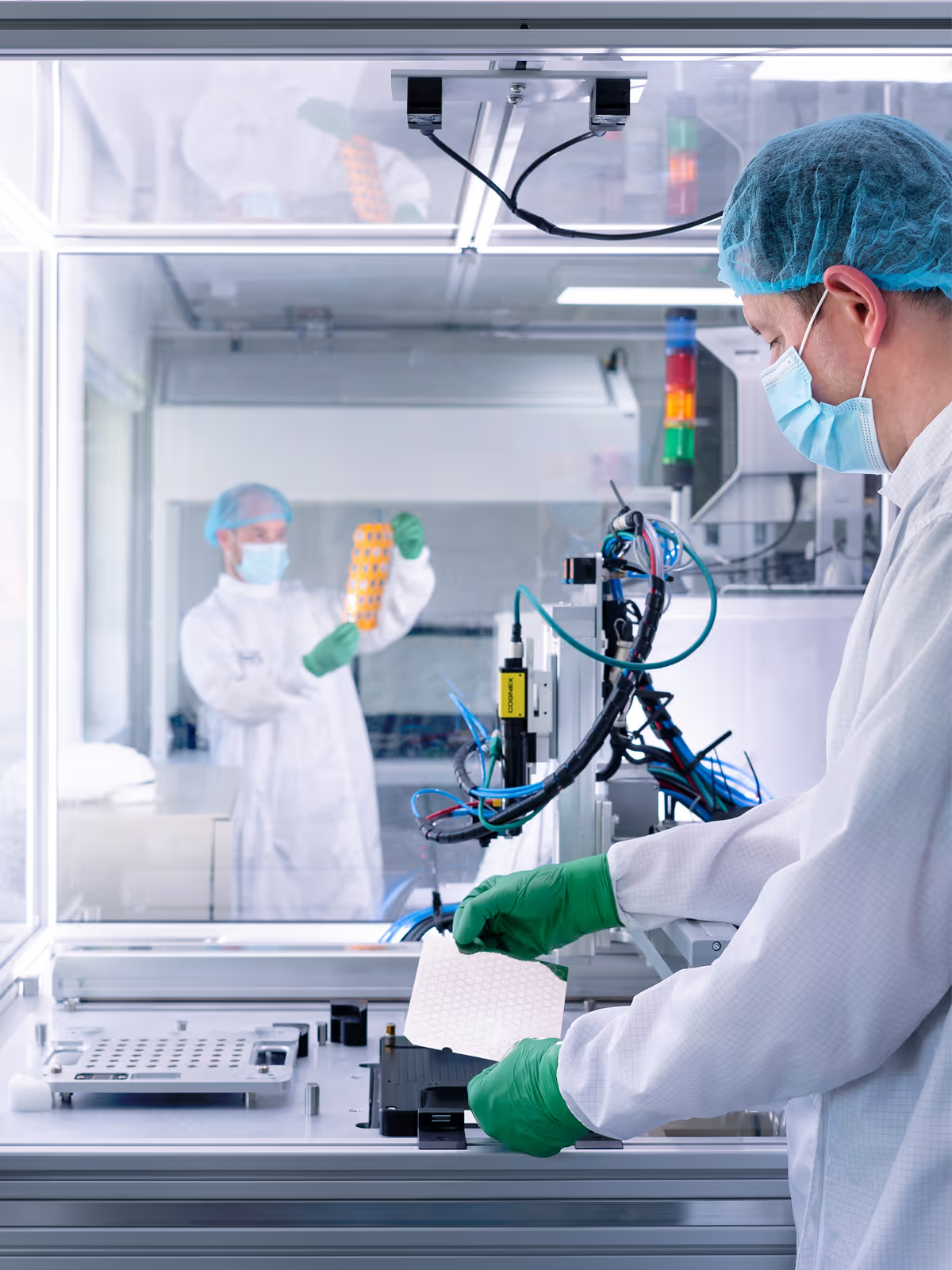
Meet some of the team
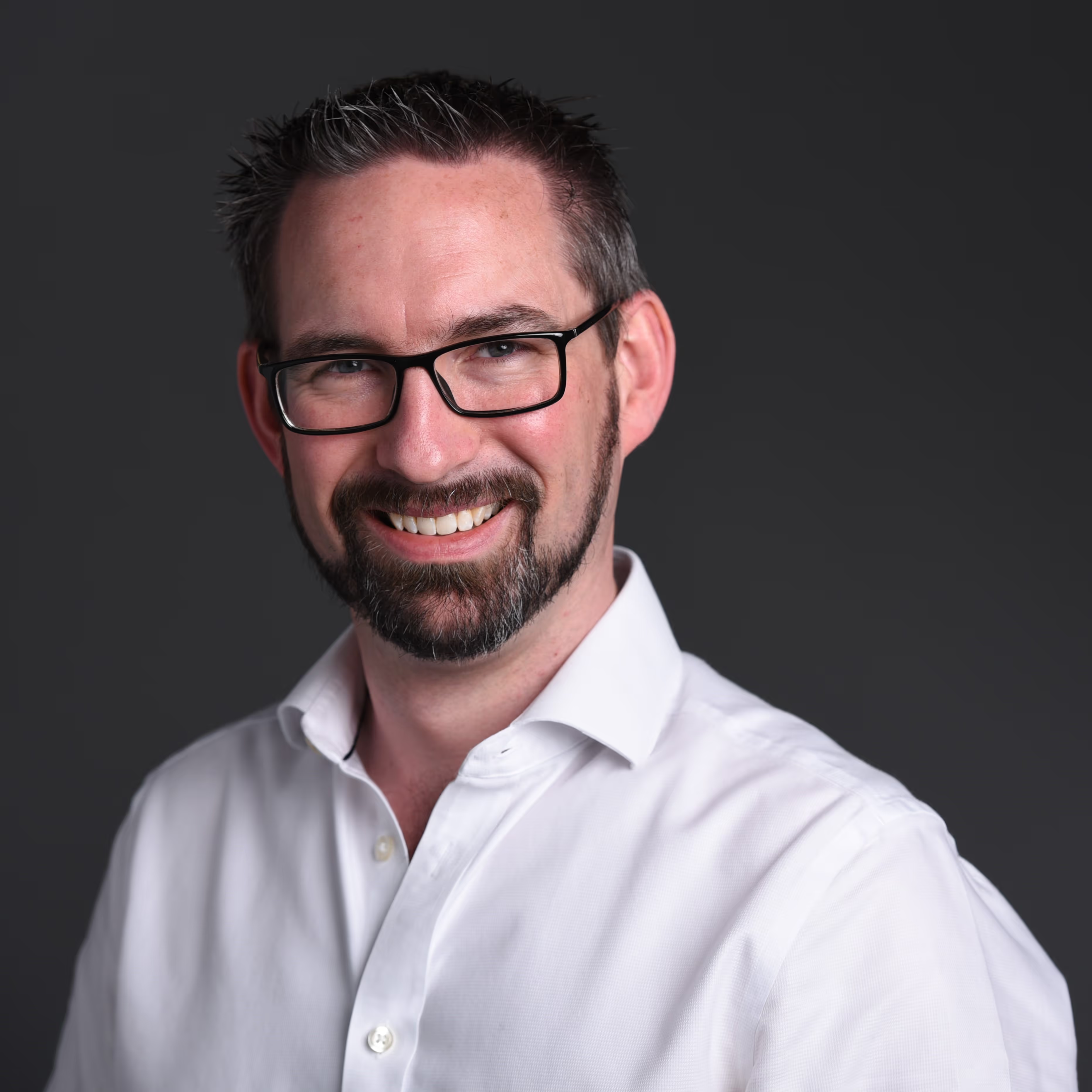
David Cottenden
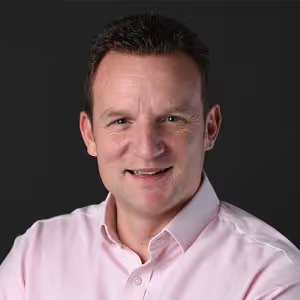
James Howarth
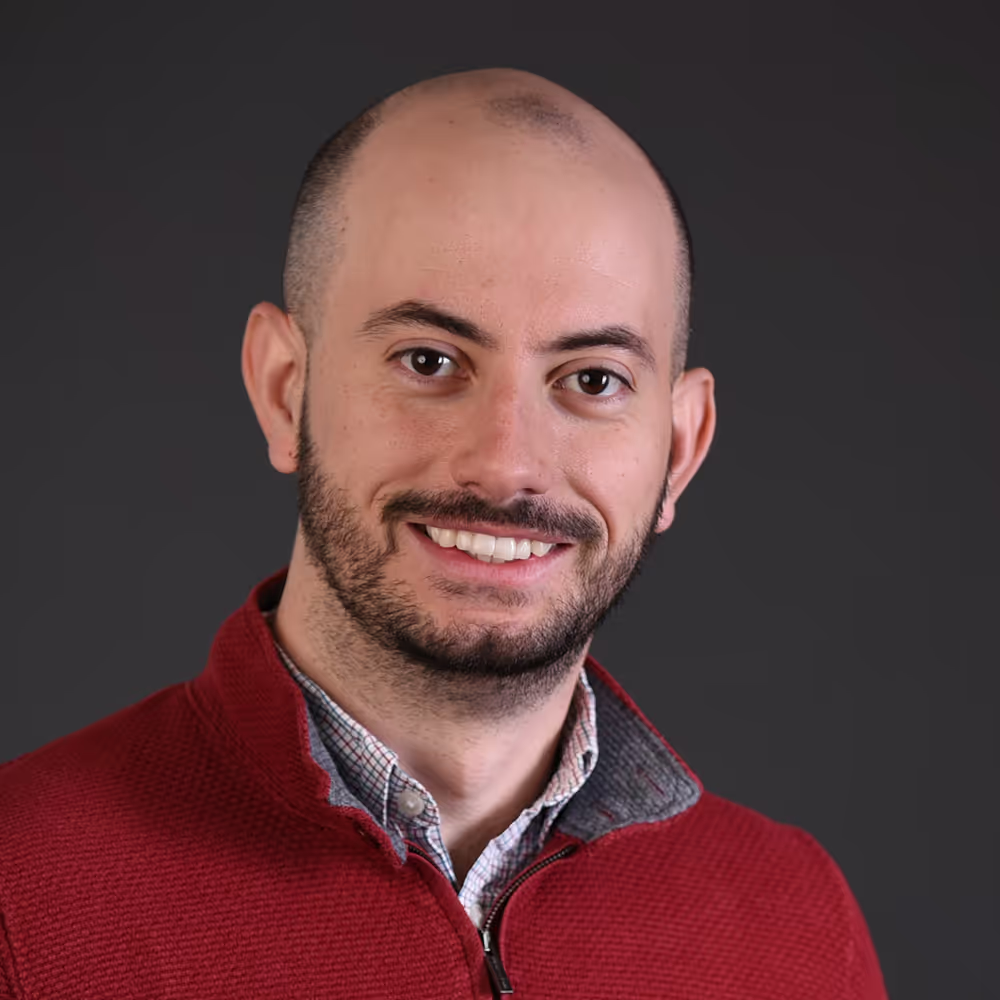
Svilen Savov
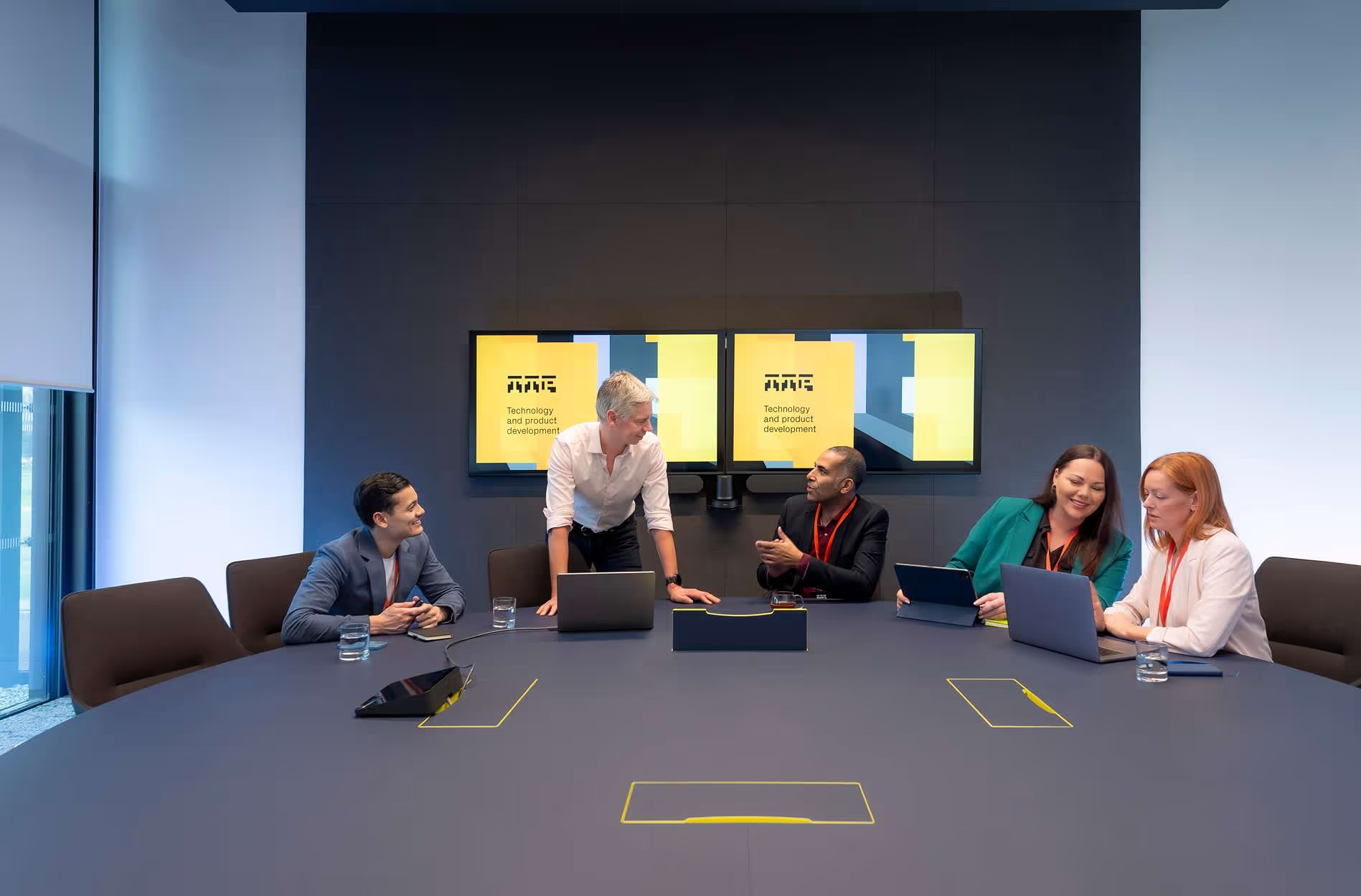