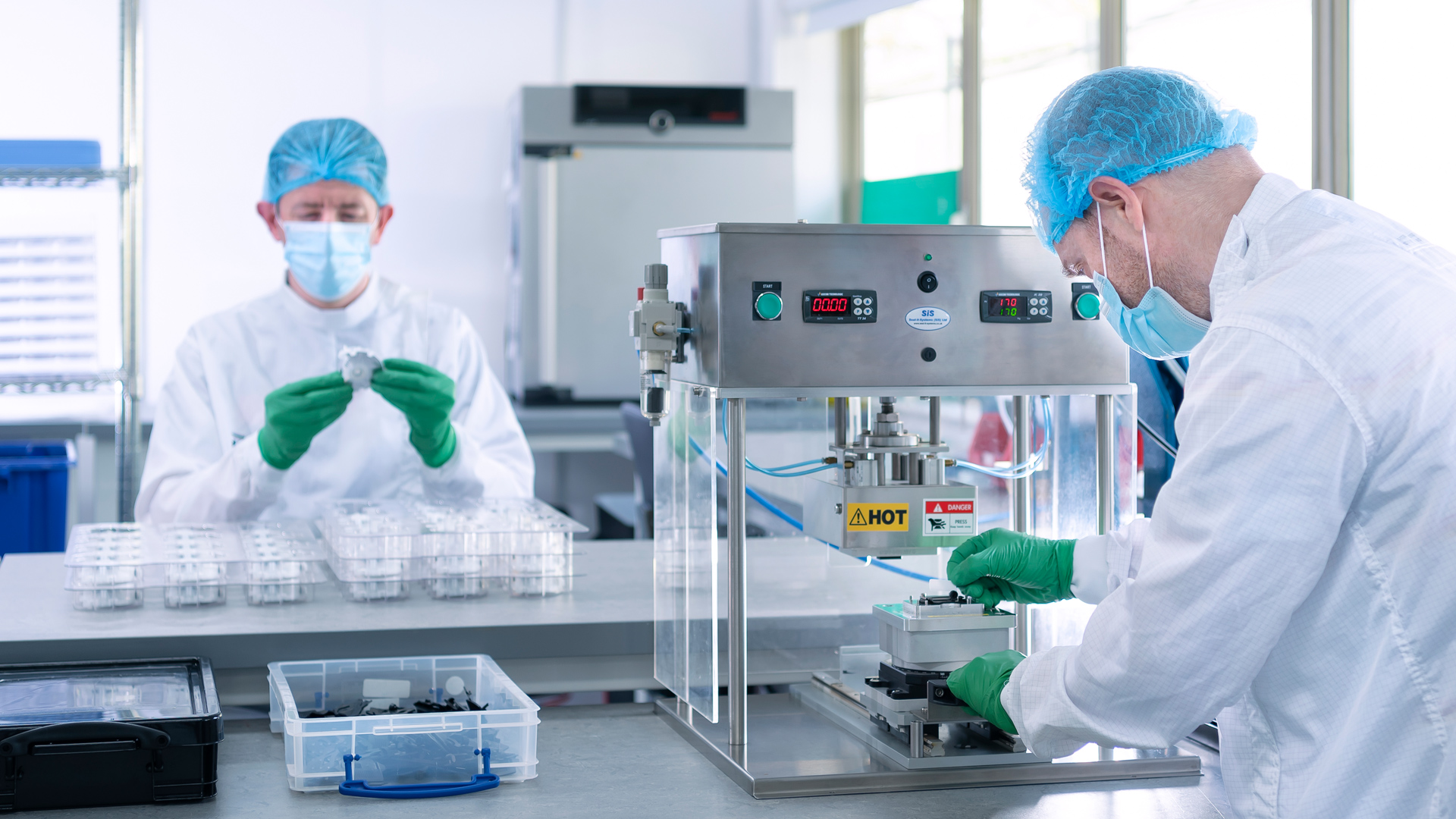
Manufacturing capability at TTP
Reducing risk and time to market by taking your products from development into manufacture.
Working seamlessly with TTP development teams, TTP’s Manufacturing group can take your products through prototype builds, clinical trials, pilot manufacture and into ongoing production. With our dedicated manufacturing team and facilities including microfabrication, cleanrooms, electronics and mechanical assembly, TTP Manufacturing carries out controlled, traceable builds, reducing your development uncertainty, risk and time to market.
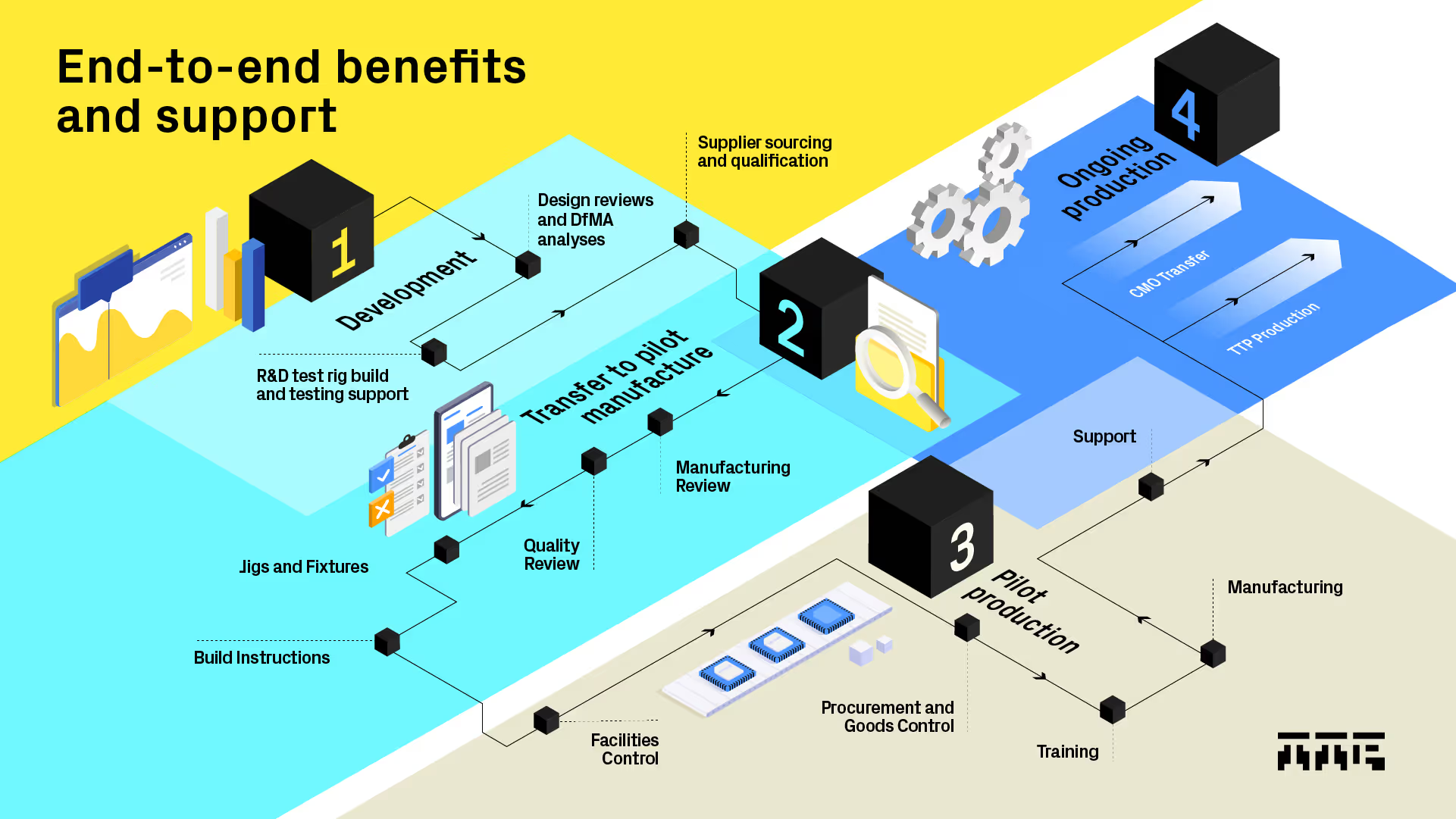
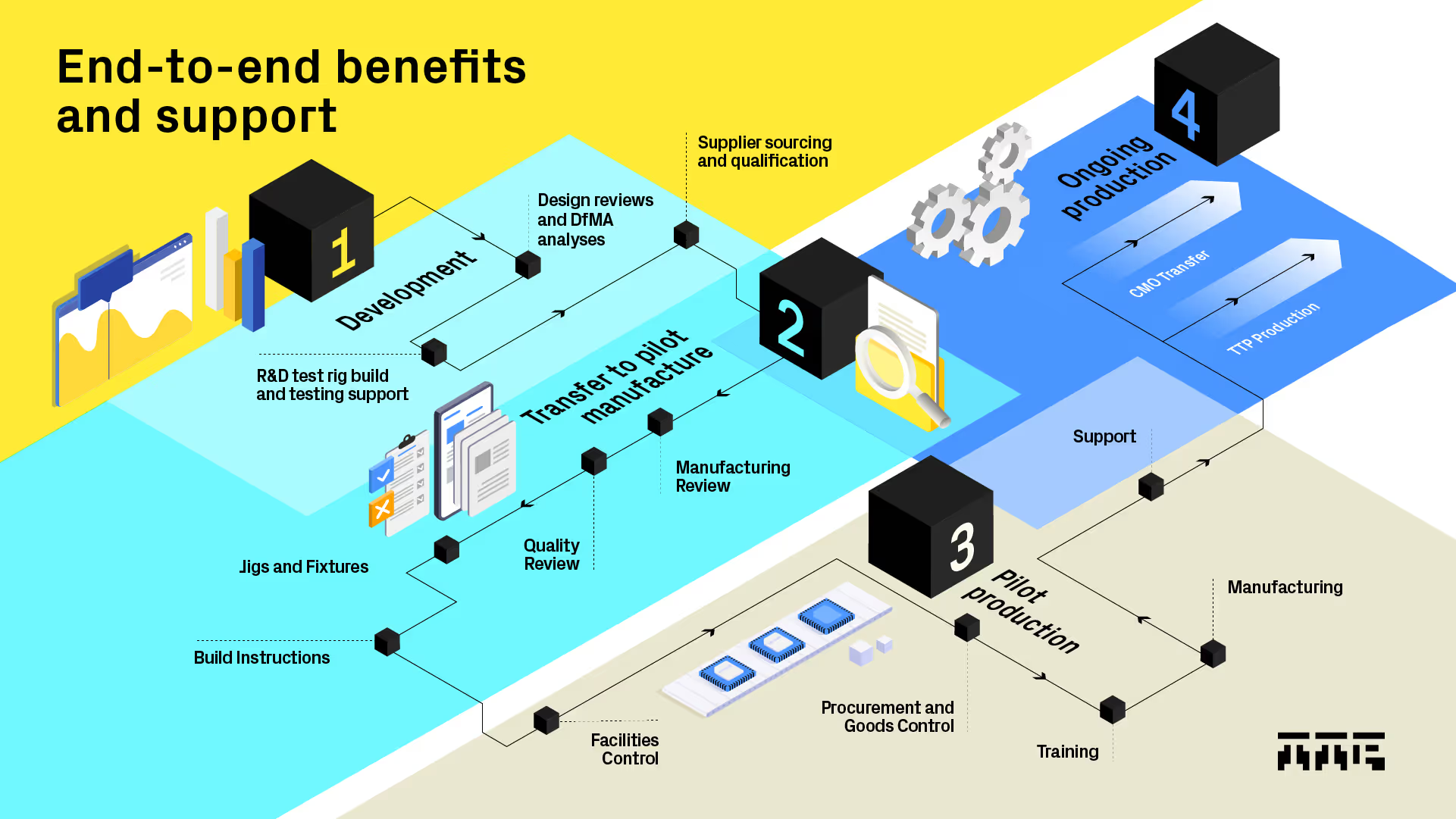
End to end product development and manufacturing
We offer a unique blend of consulting and manufacturing, with a truly end to end service that enables you to move seamlessly and quickly from design and development into prototype builds, clinical trials, pilot manufacture and ongoing production. By using TTP’s Manufacturing services, you can avoid the risks, costs and time involved in the transfer to a 3rd party manufacturer at a critical point in your project.
TTP Manufacturing works with project teams during the development process and offers manufacturing engineering insight to ensure designs are optimised. We are experts in the development and refinement of manufacturing processes, and apply lean manufacturing techniques to optimisation of production workflows. We then oversee everything from BOM management, supplier selection, procurement, stocking and goods control, process FMEA and the manufacturing and test of products. We create full work instructions and all the necessary records for ISO13485 manufacturing of medical devices if required. Our flexible and agile approach means we can quickly turn resources on and off without an additional cost burden, allowing production volumes to grow with your product’s success. We manage change efficiently and when the time is right will guide your production to a full-scale contract manufacturing organisation.
With a track record of tens of thousands of devices produced across life science, medical device and deep tech industry sectors, and relationships with clients forged across 10+ years, TTP Manufacturing is your partner for the verification and production of your products.
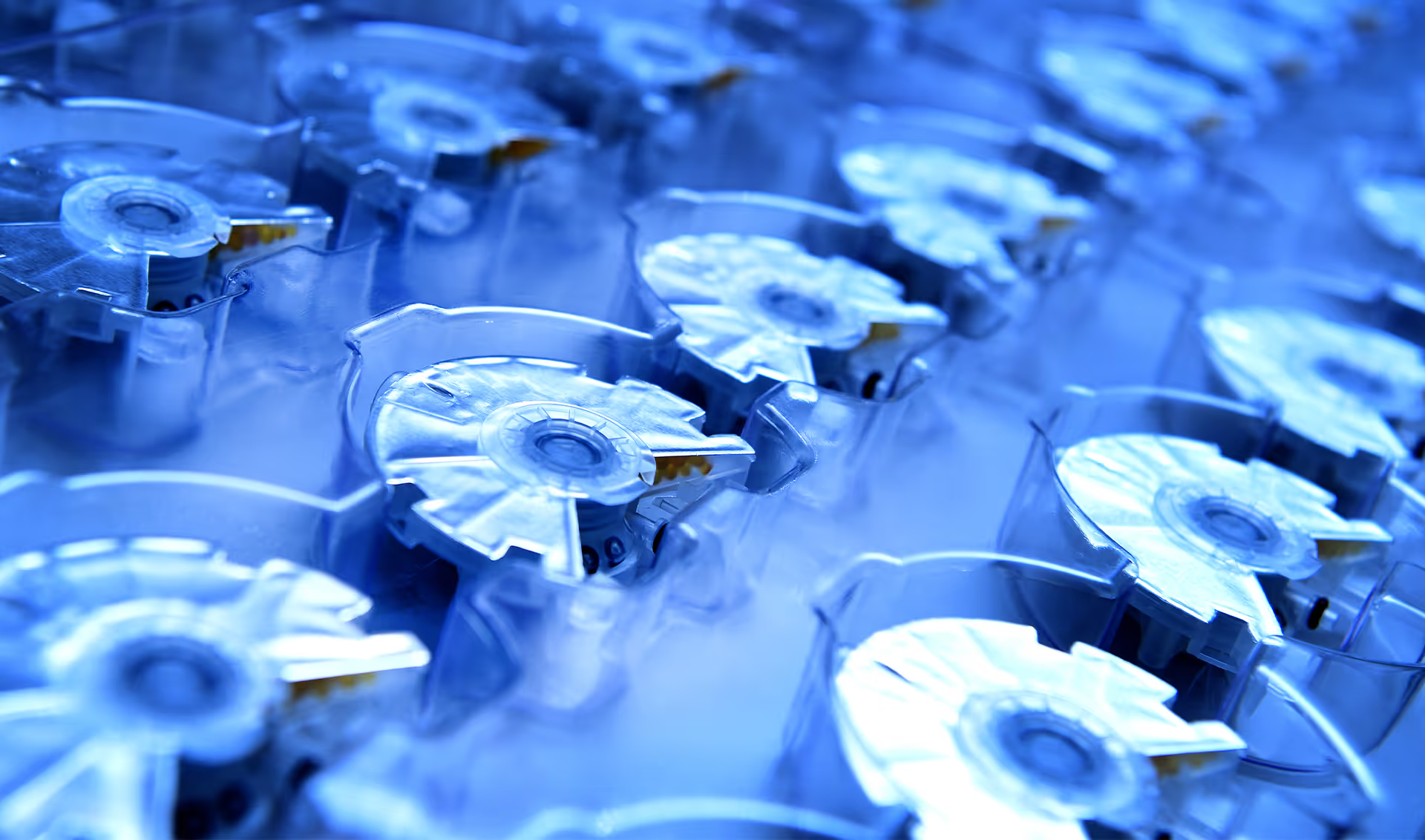
Because TTP is involved in the development and manufacturing, the knowledge is retained through the process, which is unique. What you offer is really fantastic.
Mohammadreza Sohbati
Executive Vice President
,
DNA Nudge
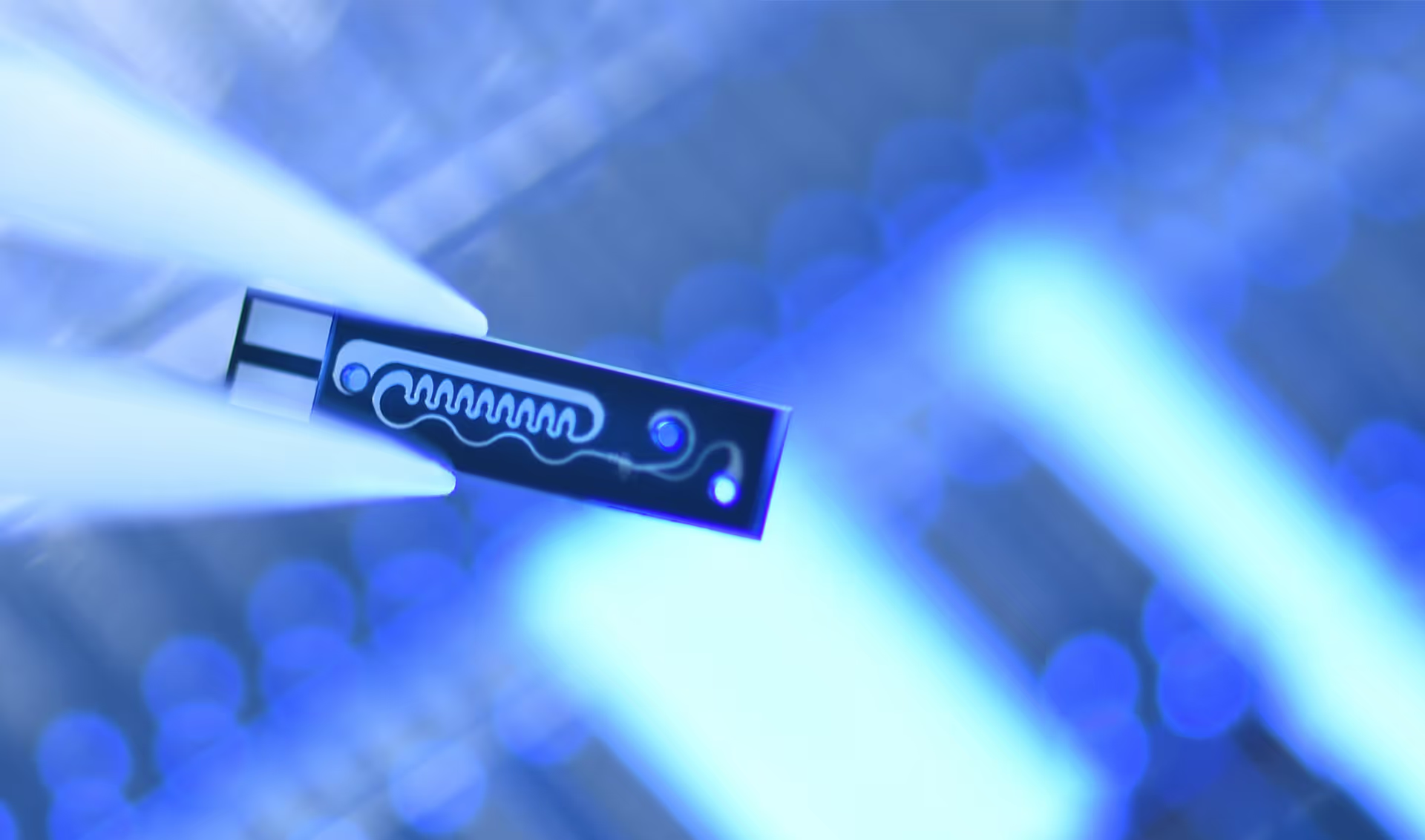
TTP Manufacturing’s Microfab facility allowed us to get performance success in the early stages of development – CSEM and Philips could not have carried out such rapid iteration at a critical point in the development of our technology.
Salman Samson Rogers
Co-Founder and CTO
,
Cellular Highways
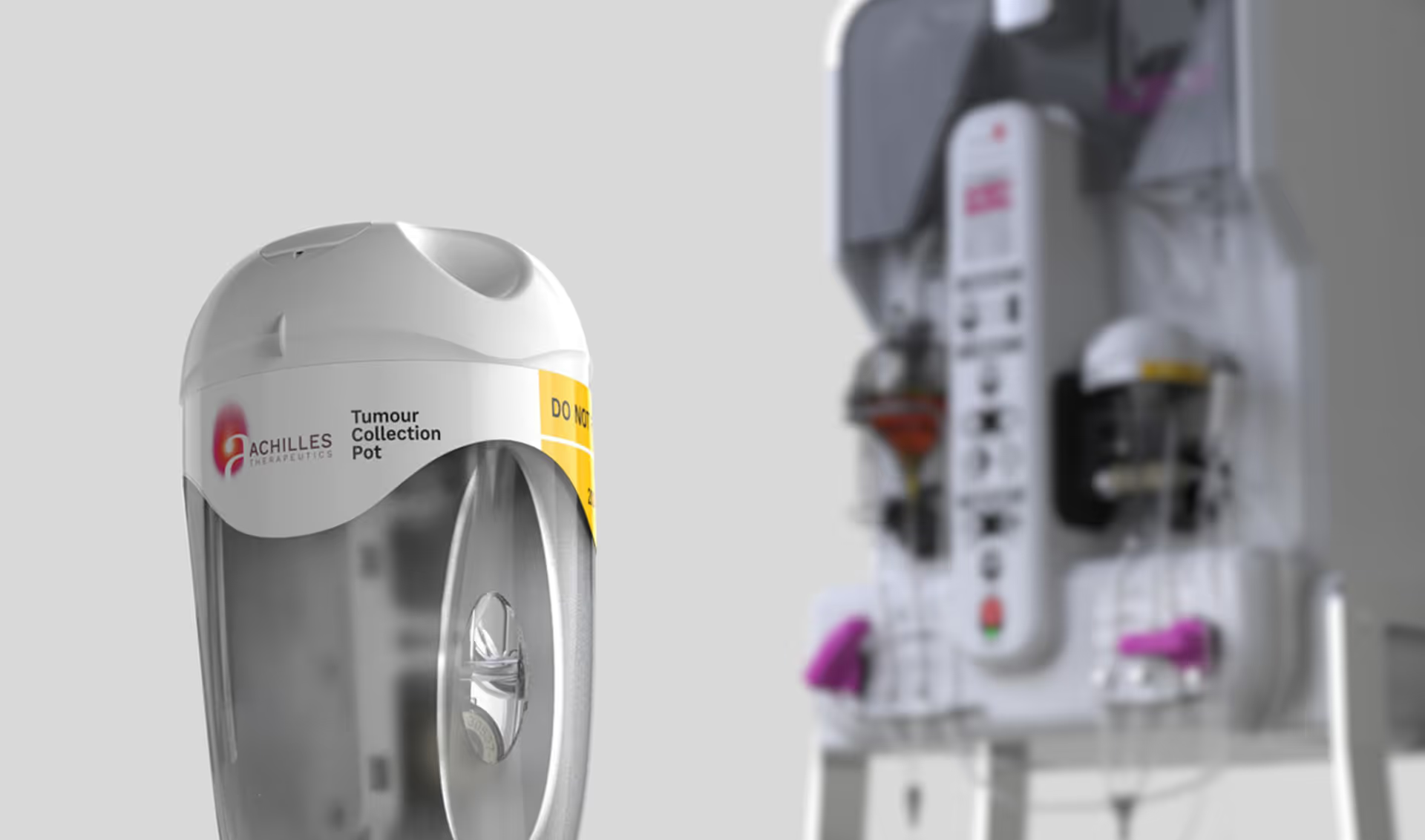
TTP has been an incredible partner, complementing our expertise and delivering designs from whiteboard to moulded functional prototypes. With TTP’s support, Achilles Therapeutics is scaling its manufacturing process and bringing transformative therapies from bench to bedside. The TTP team has shown the same level of excitement as us in getting these therapies to the people who need them.
Ed Samuel
EVP Technical Operations
,
Achilles Therapeutics
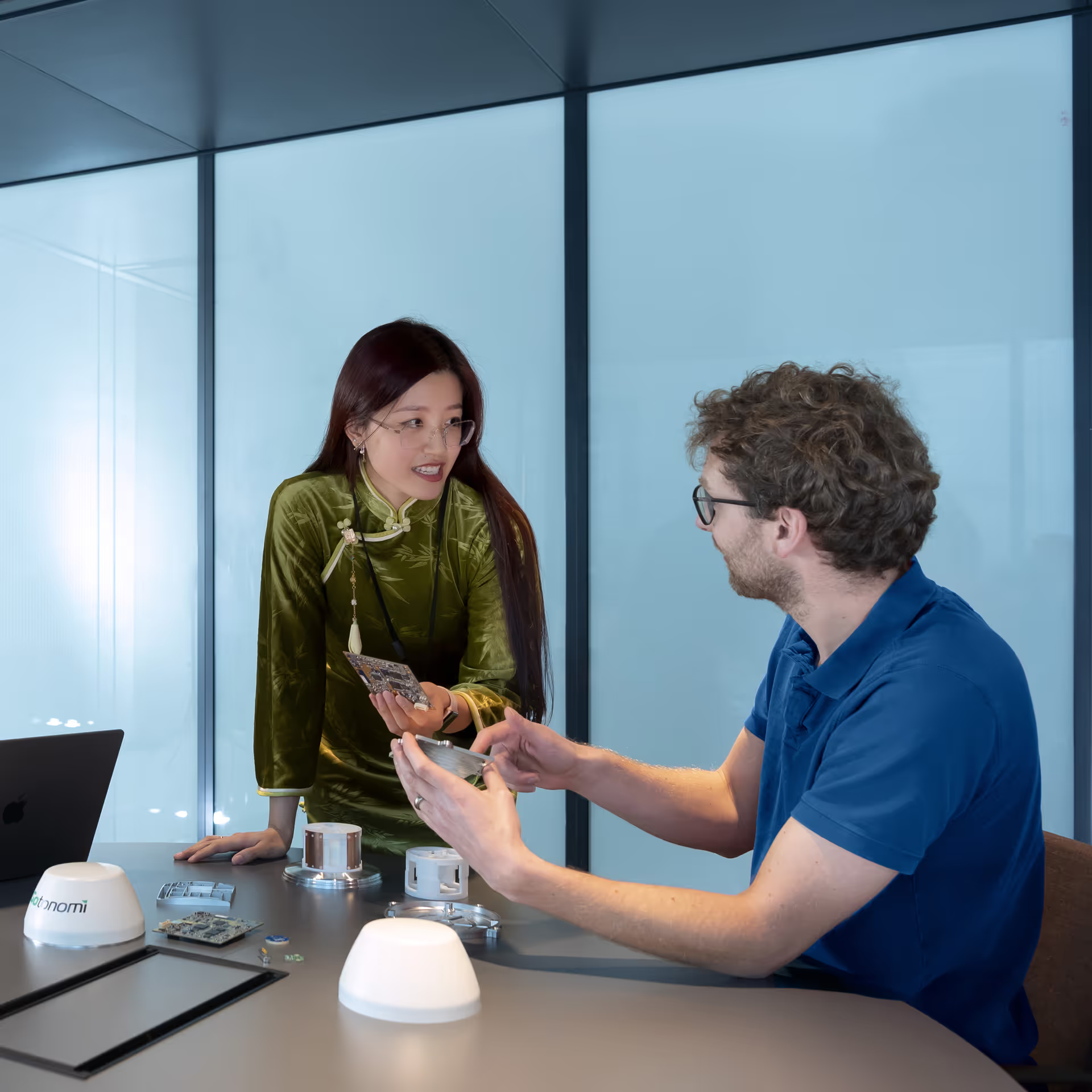
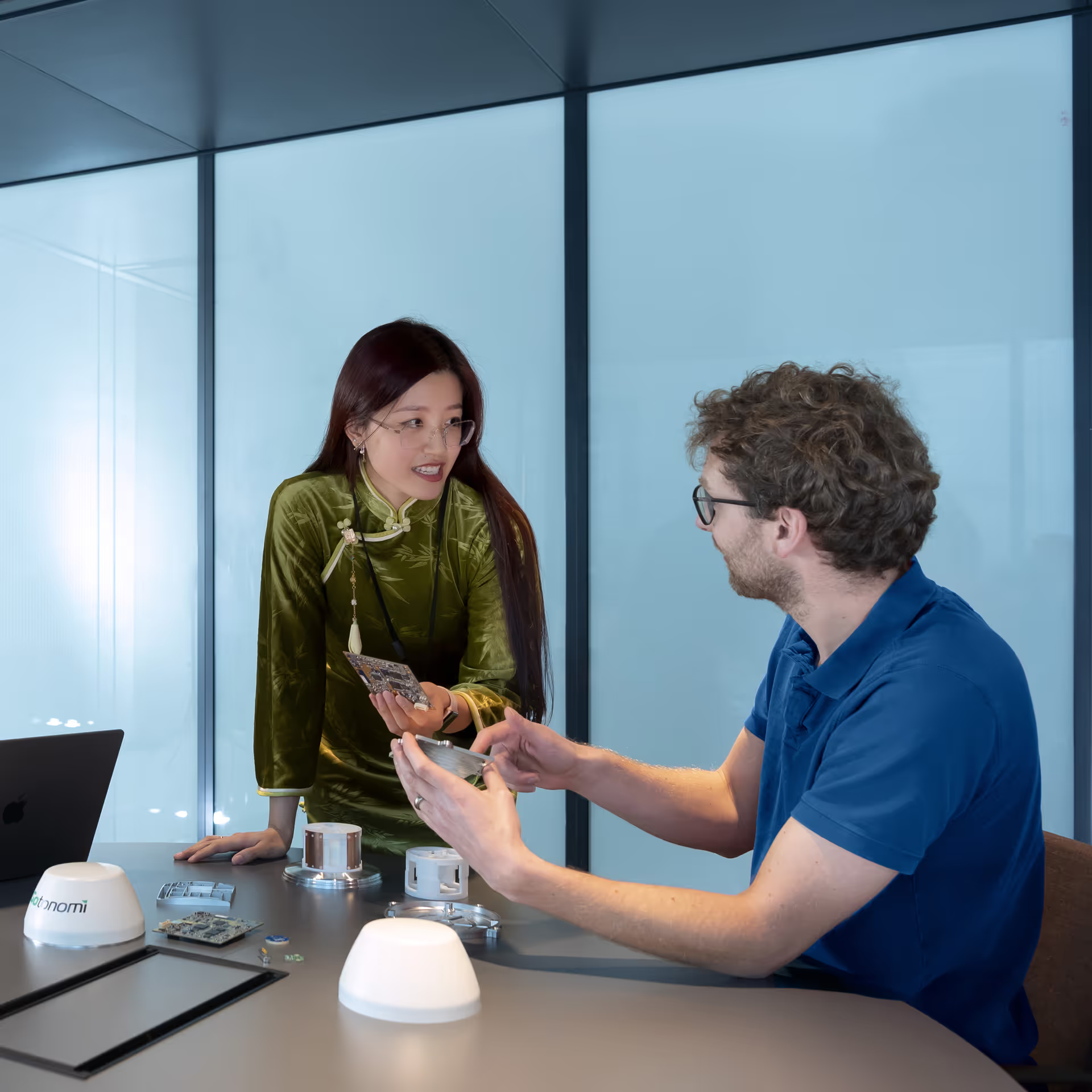
Integrating manufacturing and development
Ensuring a product can be efficiently manufactured is an essential part of the development process. Recognising this at TTP is key to the quality of our designs and the products our clients bring to market.
At each step of the design and development process, the manufacturing team provides input into design reviews using skills like Design for Assembly analysis along with hands-on experience of system builds and manufacturing process development. As projects move into prototype builds, the manufacturing team works alongside our design engineers and technical team, ensuring continuous improvement of the product. As projects require higher volume prototype builds, for example for medical product verification testing, the manufacturing team takes on all aspects of the build and assists the design team in the development of jigging, fixturing and end of line testing.
Close integration of the TTP design and manufacturing teams removes issues that are often seen when transferring products to contract manufacture. When the time comes to transfer your product for high-volume manufacturing TTP will support you every step of the way, with collaborative builds, full data pack preparation and training and debug at the CMO site. Because TTP Manufacturing is involved from early in the programme, the transfer is as seamless as possible.
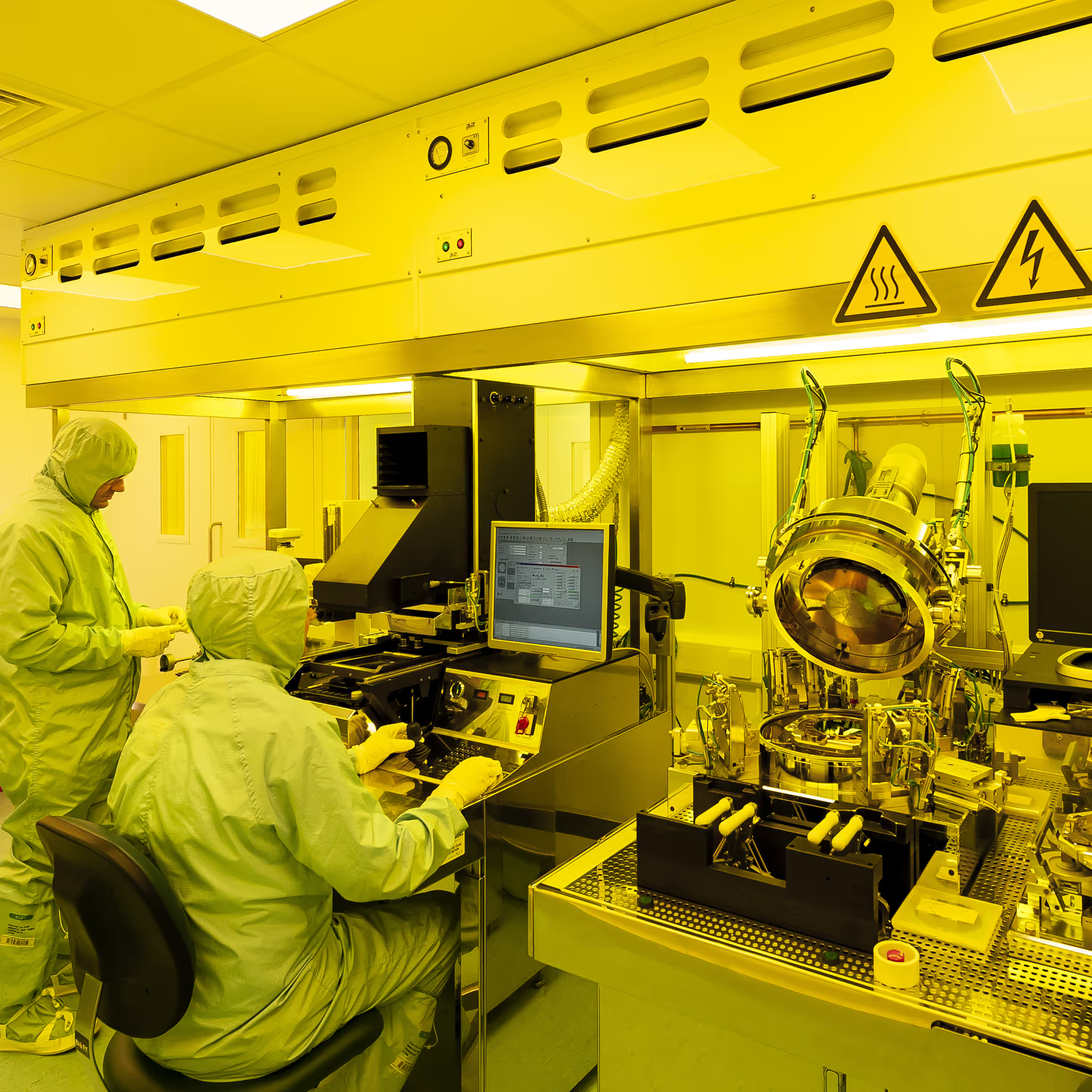
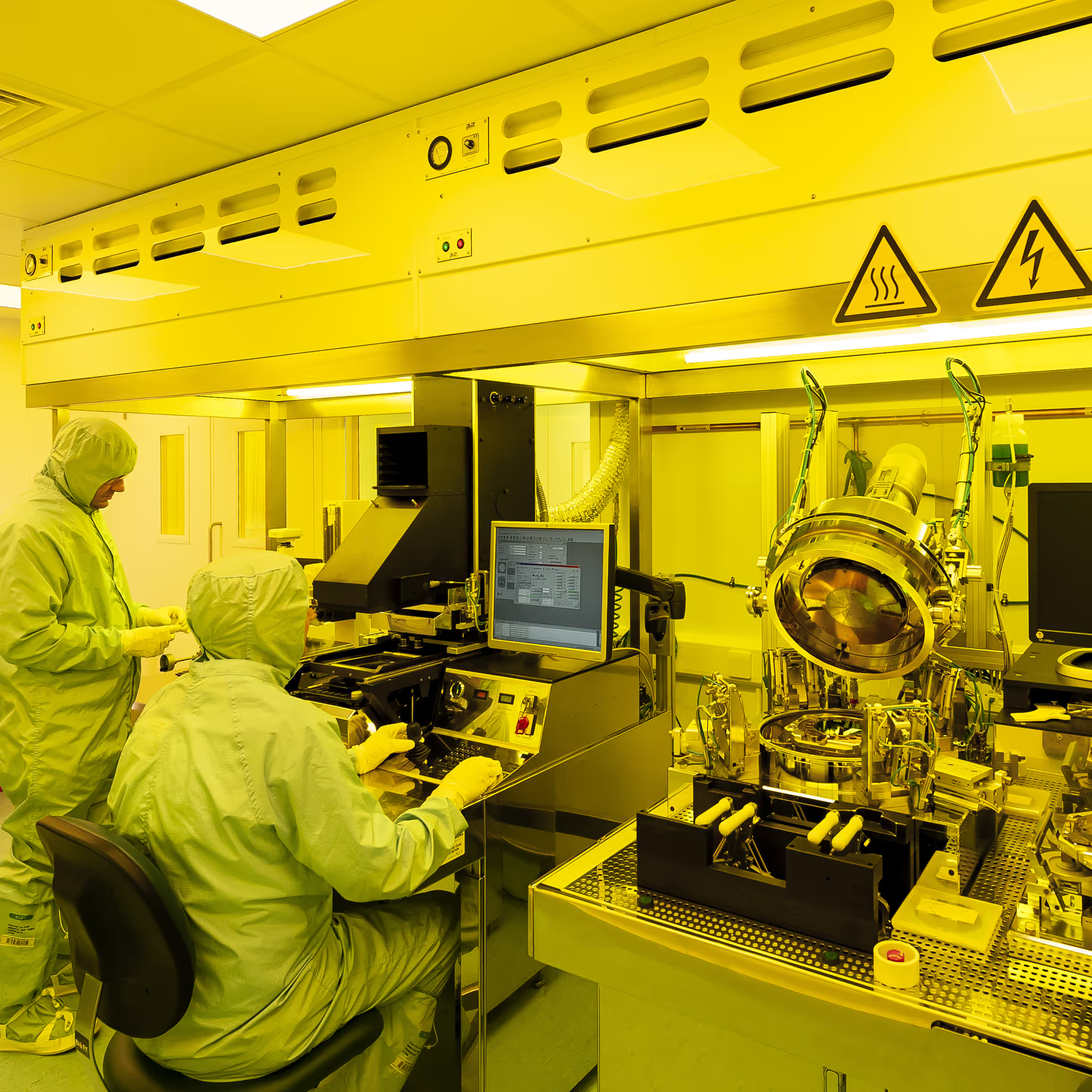
Accelerating device development with microfabrication capability
When developing sensors, devices and microfluidic products, microfabrication techniques come into their own. With our own microfabrication facility on site, TTP is uniquely placed to develop these devices incredibly quickly when compared with using a full-scale foundry.
TTP’s µ-fab facility has a comprehensive range of fabrication, packaging and characterisation equipment for the development of micron-scaled products, paired with over 30 years of microfabrication experience. Operating in an ISO6 cleanroom, we cover silicon, glass and polymer processes, along with forming and bonding techniques. This broad range of capabilities, combined with your product vision and our design teams’ expertise can make your ideas into reality in a surprisingly short time. Iterative design loops become faster, your risks are managed and costs and time to market are reduced.
When it comes to scaling up your product, the µ-fab can prove out production up to 6” wafer scale, and then work with our global network of foundries to transfer your device to full-scale manufacture, guided by our experts all the way.
TTP’s ground-breaking microfabrication devices include a compact and fast microfluidic cell sorter for therapeutic applications, PCR for rapid DNA amplification, tiny all-optical sensors for medical and other non-EM applications, accurate spray nozzles, polymer light waveguides and ultrasound imaging micro-chips.
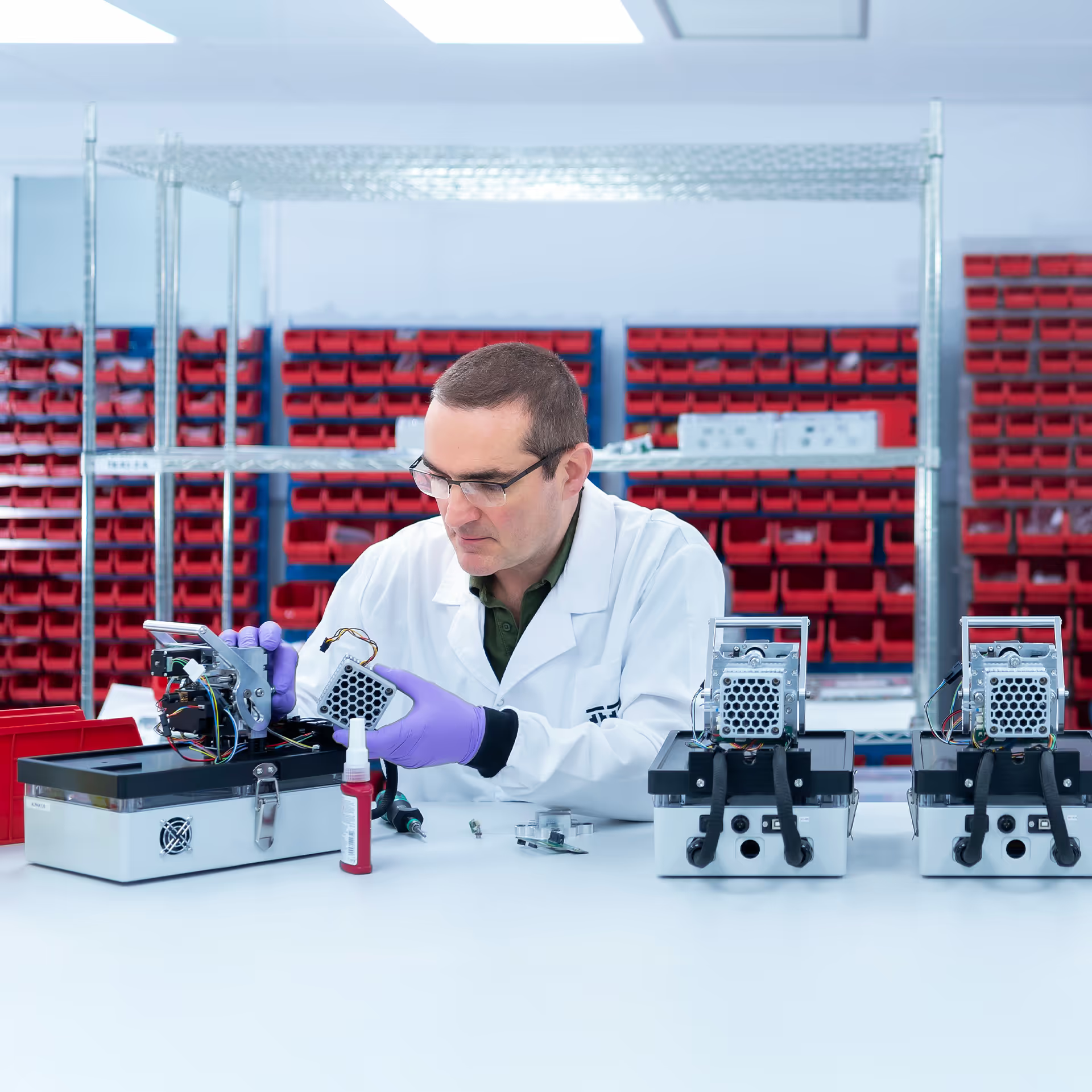
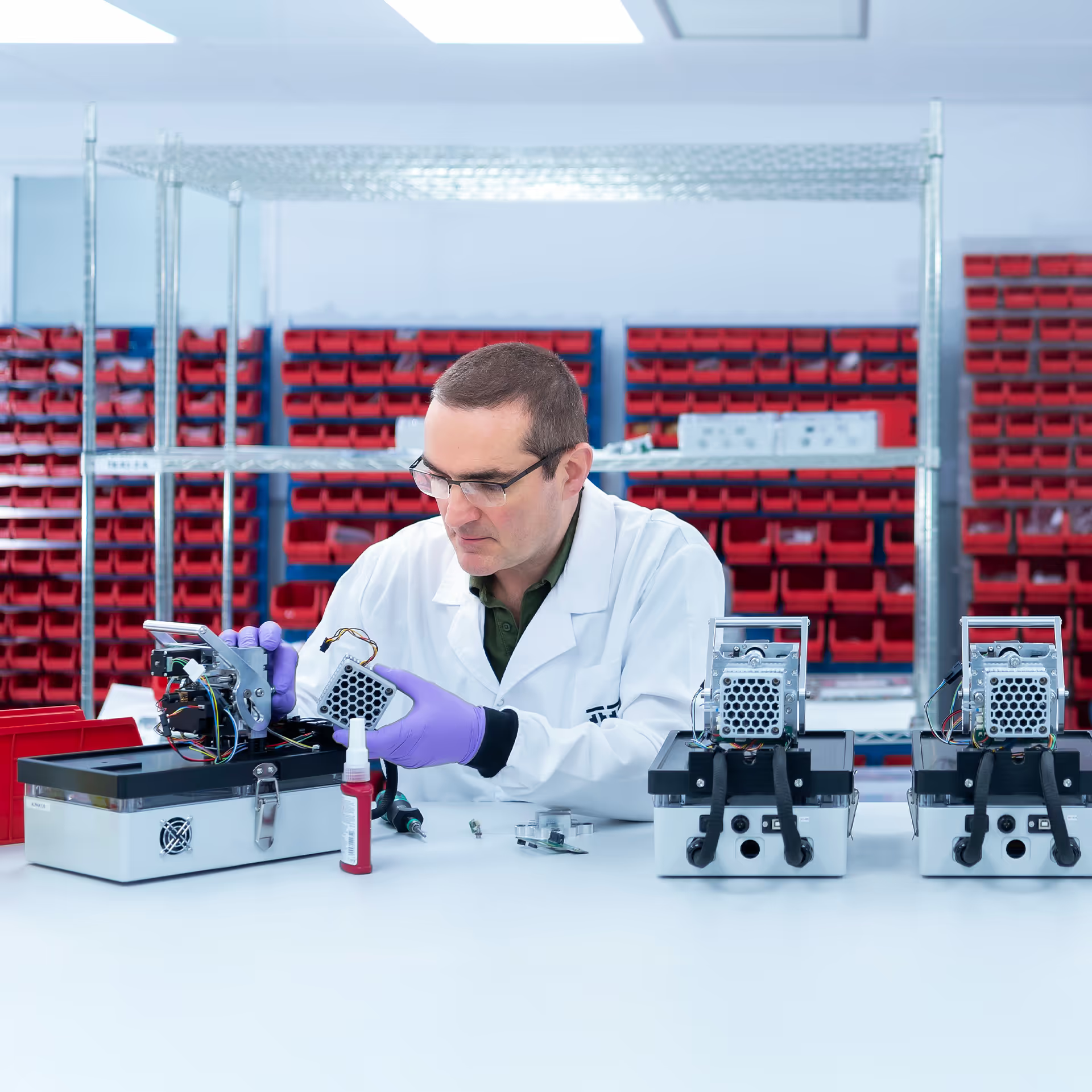
Series production with quality system compliance
Knowing when to transfer a product to full-scale contract manufacturing is difficult, especially when market adoption is uncertain, or the product is so novel it is creating its own market. The process of design transfer can be complex, costly and rather than presenting an opportunity for your business, can be a stumbling block to your progress.
This is where partnering with TTP Manufacturing makes sense. We can set up for series manufacturing with full compliance to quality system requirements, including ISO13485:2016 for medical devices. Our trademark agility and flexibility to your needs can help with the uncertainty of production volume requirements. Our integrated approach means the teams who designed your products are on hand immediately to solve any issues and ensure we deliver to your requirements. If changes are required, our joined-up approach means ECNs are processed rapidly, production re-validated and designs re-verified if required.
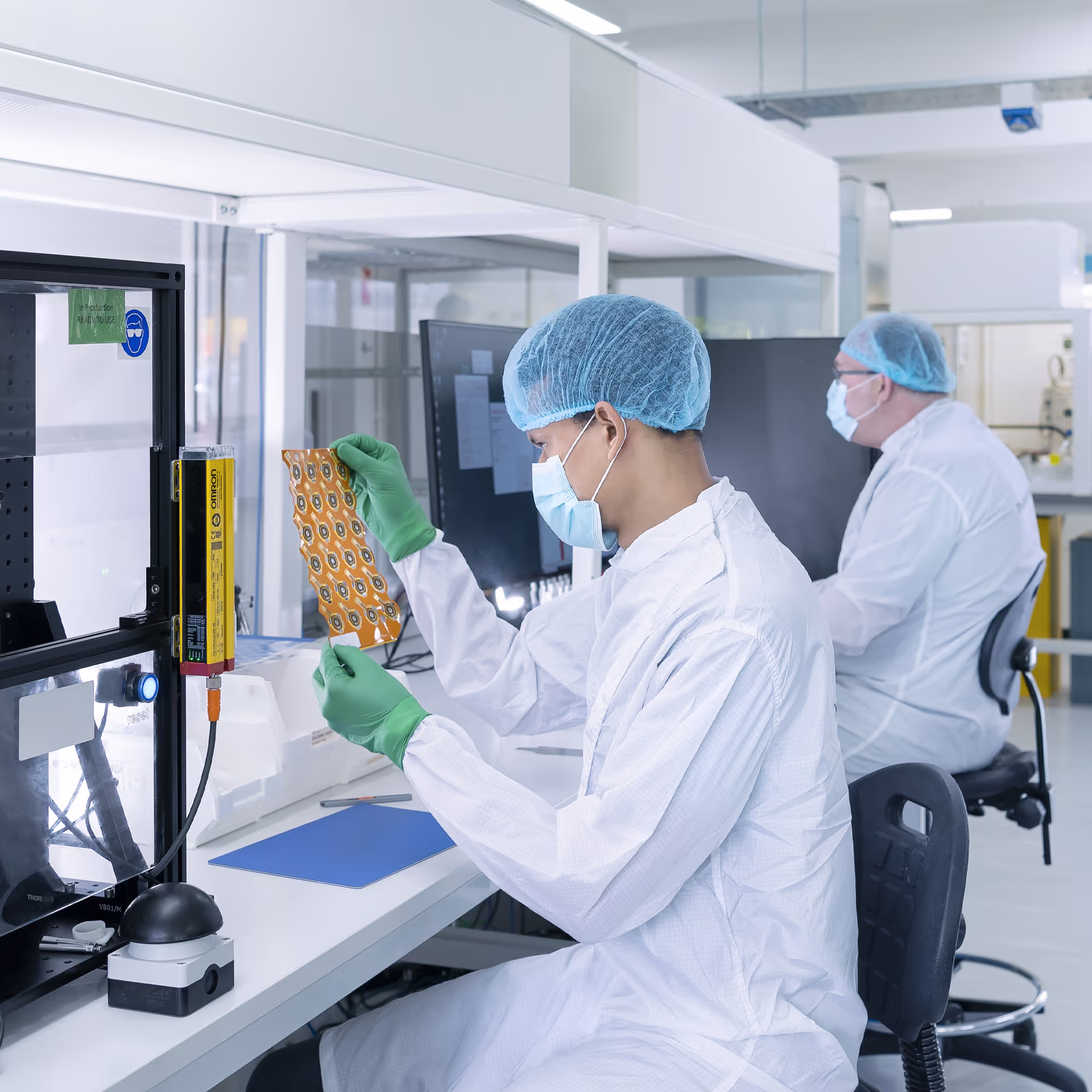
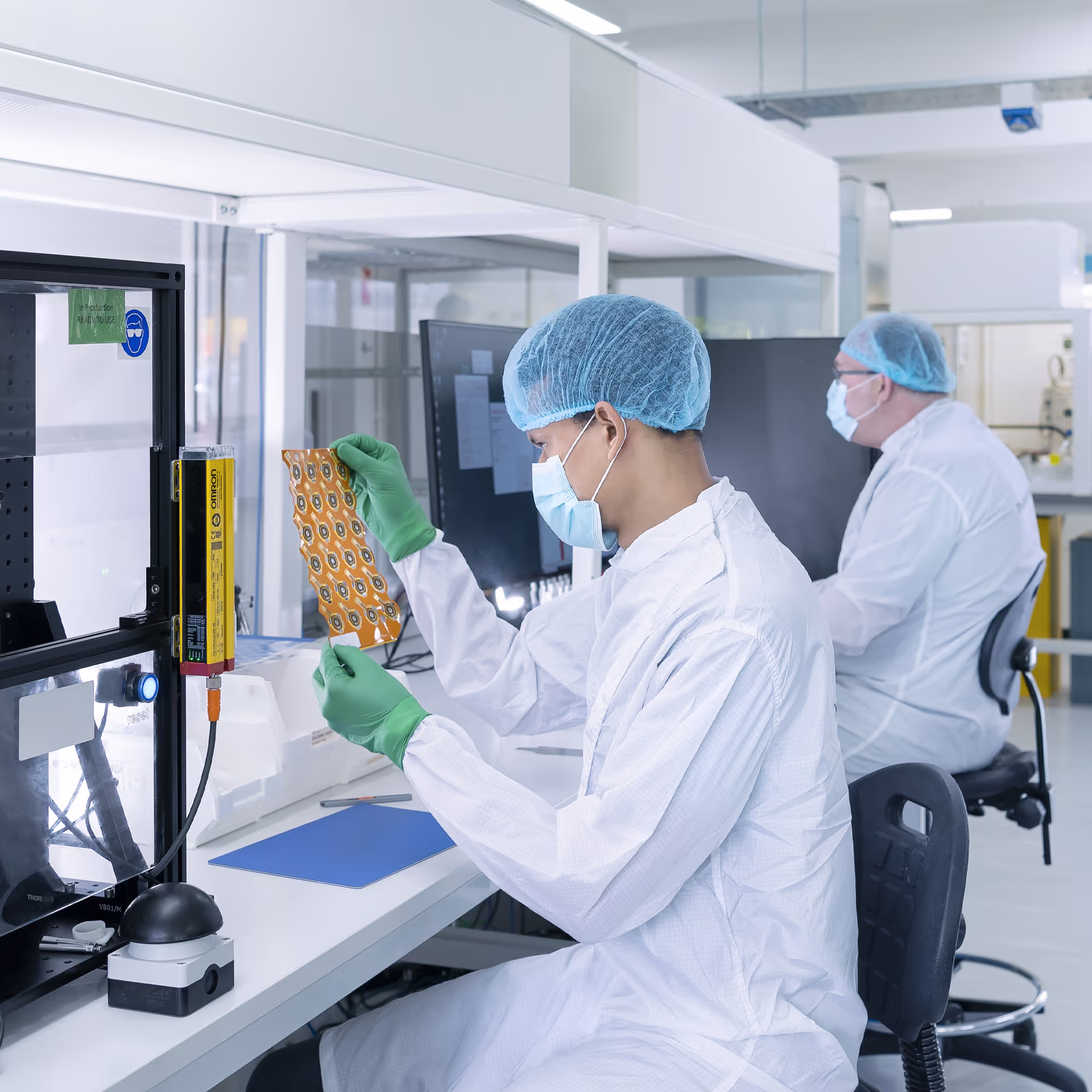
Cleanroom facilities for medical device manufacturing
We operate a robust QMS for IVD and medical device manufacturing. Our manufacturing facilities include ISO 6, 7 and 8 cleanroom facilities, which are managed and controlled in compliance to relevant cleanroom standards. We operate part controls and traceability according to the requirements of your build, we produce batch records and manage product release, and we maintain all the necessary records for facilities, equipment, training and manufacturing processes.
TTP Manufacturing has a track record in the production of tens of thousands of devices, with customer relationships over more than 10 years. When the time is right, based on your business and market growth, we stand ready to guide you through the process of transferring your production to full-scale CMO.
If you're looking to turn your prototypes into qualified products, designed for manufacture and supported as your market grows, TTP Manufacturing can help.
How we can help
Device and consumable manufacturing
We specialise in the manufacture of medical, life-science and consumer product devices, from first prototypes to verification units to clinical trial builds and series production. With a focus on quality and traceability, we collaborate with our design teams to ensure a seamless path from concept to manufacture.
Complex system assembly
TTP Manufacturing builds everything from high-value 1-offs to ongoing instrument / machine and system production. We cover industries including life science, satellite and space and energy, and handle complex RF wiring, electrical panel builds and intricate mechanical assembly. The team tests and debugs systems, providing feedback to the design teams.
Microfabrication
Our in-house microfabrication facility enables fast development of micro-devices, alongside a global network of foundries to allow production transfer of the devices we develop. With processes across silicon, glass and polymers we offer a unique environment to apply the benefits that advanced microfabrication offers in sensors, microfluidics and surface modification technologies.
Design for manufacture and assembly
Our team of manufacturing engineers is trained in DfMA (Design for manufacture and assembly) analysis, as well as having many years of practical hands-on experience of solving manufacturing issues. We can carry out an analysis on your existing design to recommend approaches for manufacturing and assembly optimisation, leading to reduced part count, reduced cost and increased reliability.
Device and consumable manufacturing
We specialise in the manufacture of medical, life-science and consumer product devices, from first prototypes to verification units to clinical trial builds and series production. With a focus on quality and traceability, we collaborate with our design teams to ensure a seamless path from concept to manufacture.
Complex system assembly
TTP Manufacturing builds everything from high-value 1-offs to ongoing instrument / machine and system production. We cover industries including life science, satellite and space and energy, and handle complex RF wiring, electrical panel builds and intricate mechanical assembly. The team tests and debugs systems, providing feedback to the design teams.
Microfabrication
Our in-house microfabrication facility enables fast development of micro-devices, alongside a global network of foundries to allow production transfer of the devices we develop. With processes across silicon, glass and polymers we offer a unique environment to apply the benefits that advanced microfabrication offers in sensors, microfluidics and surface modification technologies.
Design for manufacture and assembly
Our team of manufacturing engineers is trained in DfMA (Design for manufacture and assembly) analysis, as well as having many years of practical hands-on experience of solving manufacturing issues. We can carry out an analysis on your existing design to recommend approaches for manufacturing and assembly optimisation, leading to reduced part count, reduced cost and increased reliability.
Our approach and capabilities
We deliver across the entire life of a project, from opportunity discovery to production engineering. Discover how our interdisciplinary teams of experts collaborate to tackle the toughest product development challenges.
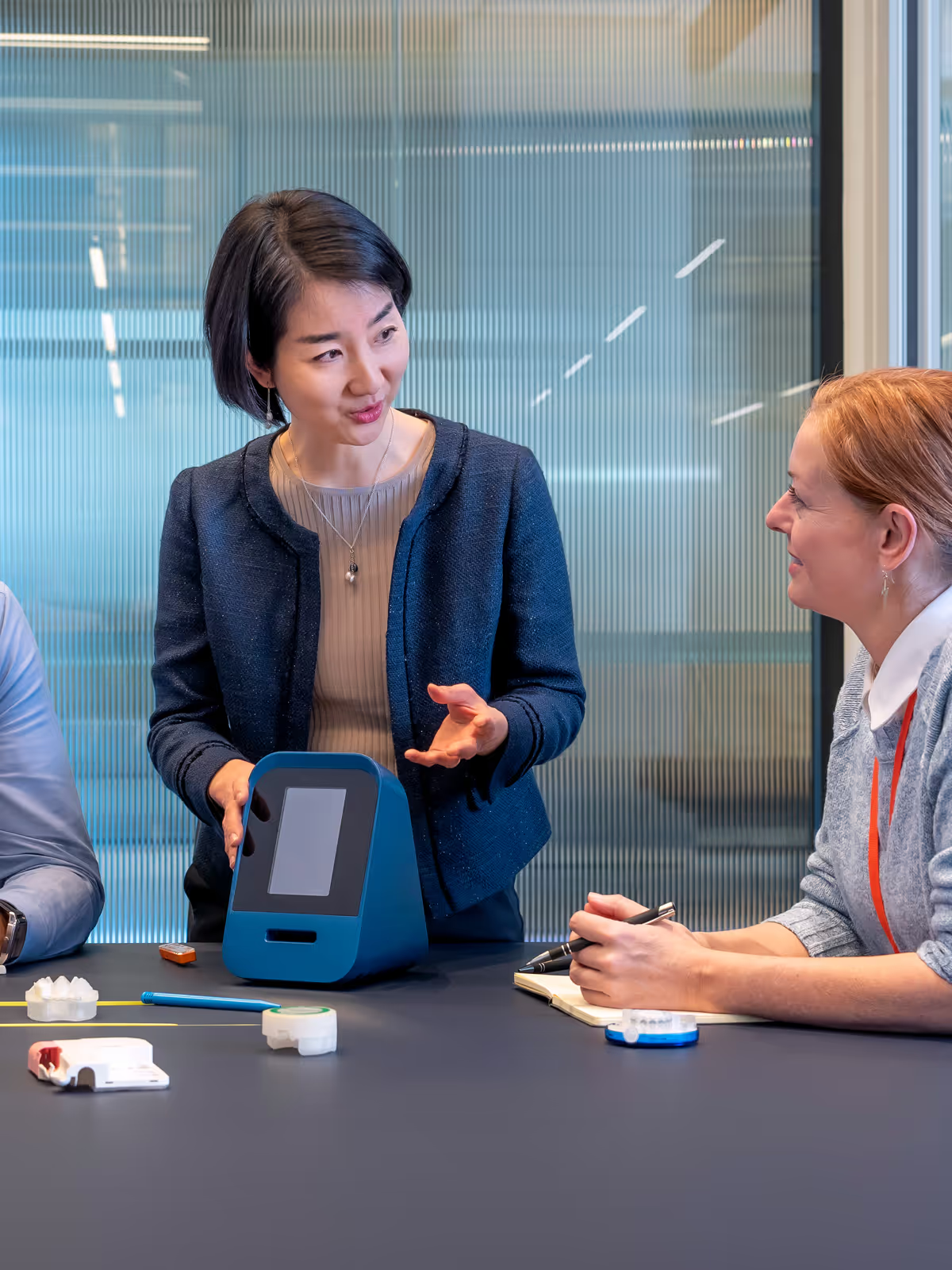
Our campus and facilities
Our award-winning campus has been designed with a clear vision. To create a space which can support our people and our clients as we develop and deliver the very best technology solutions.
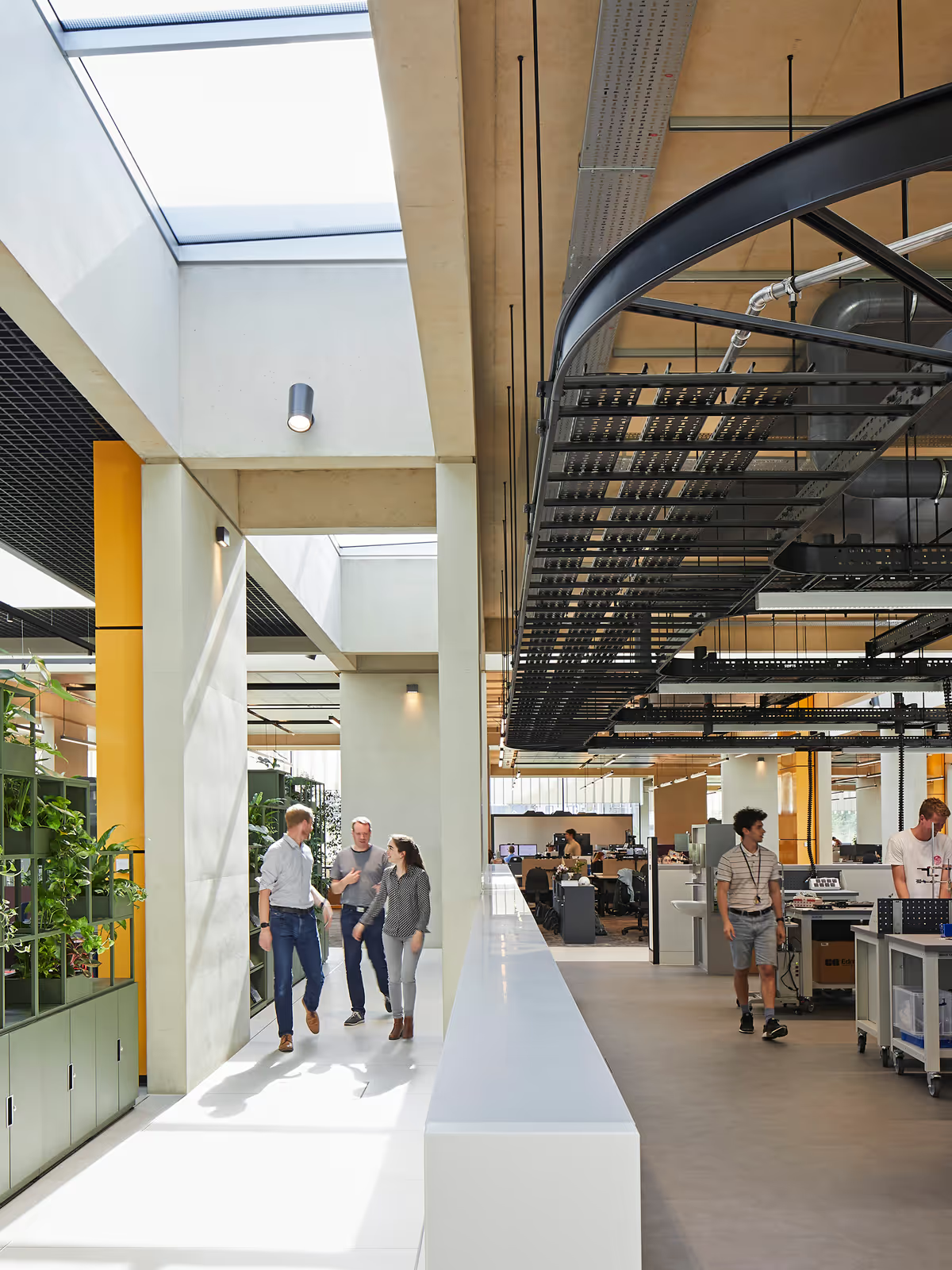
Meet some of the team
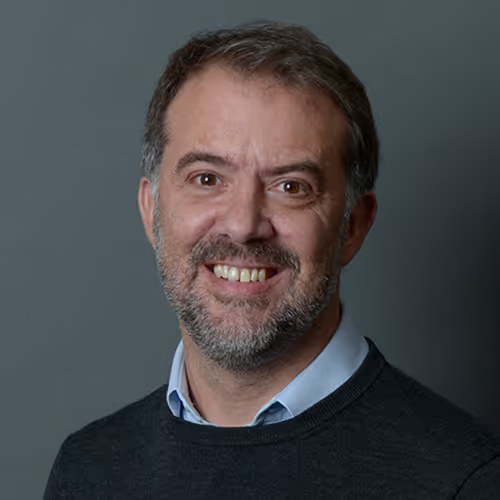
Will Cramer

Fred Hussain
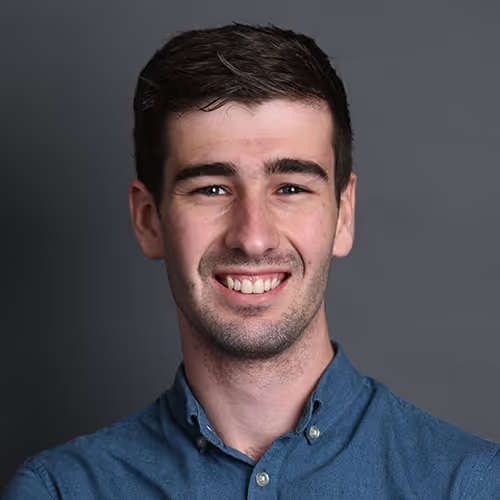
James Gregson
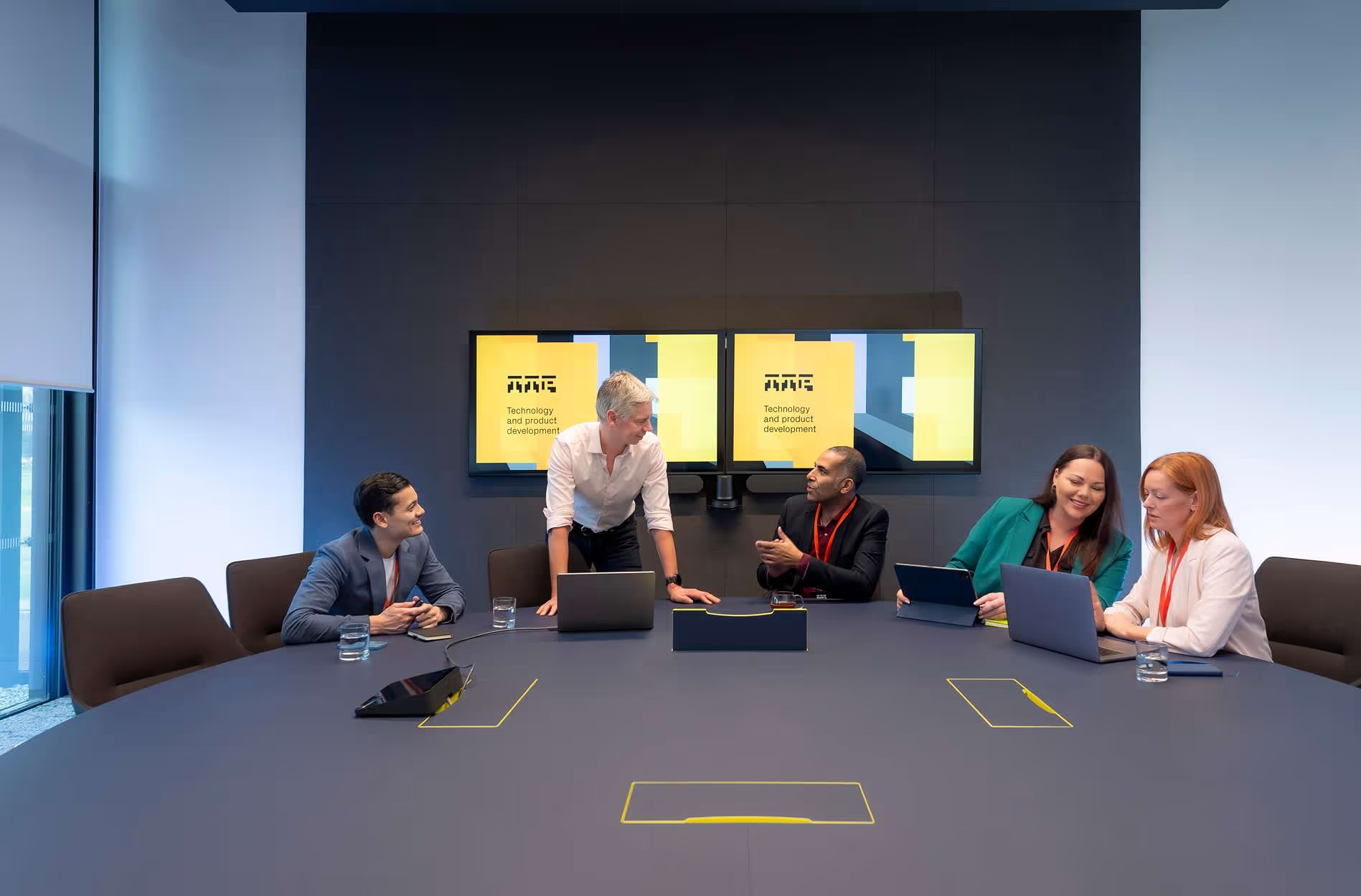
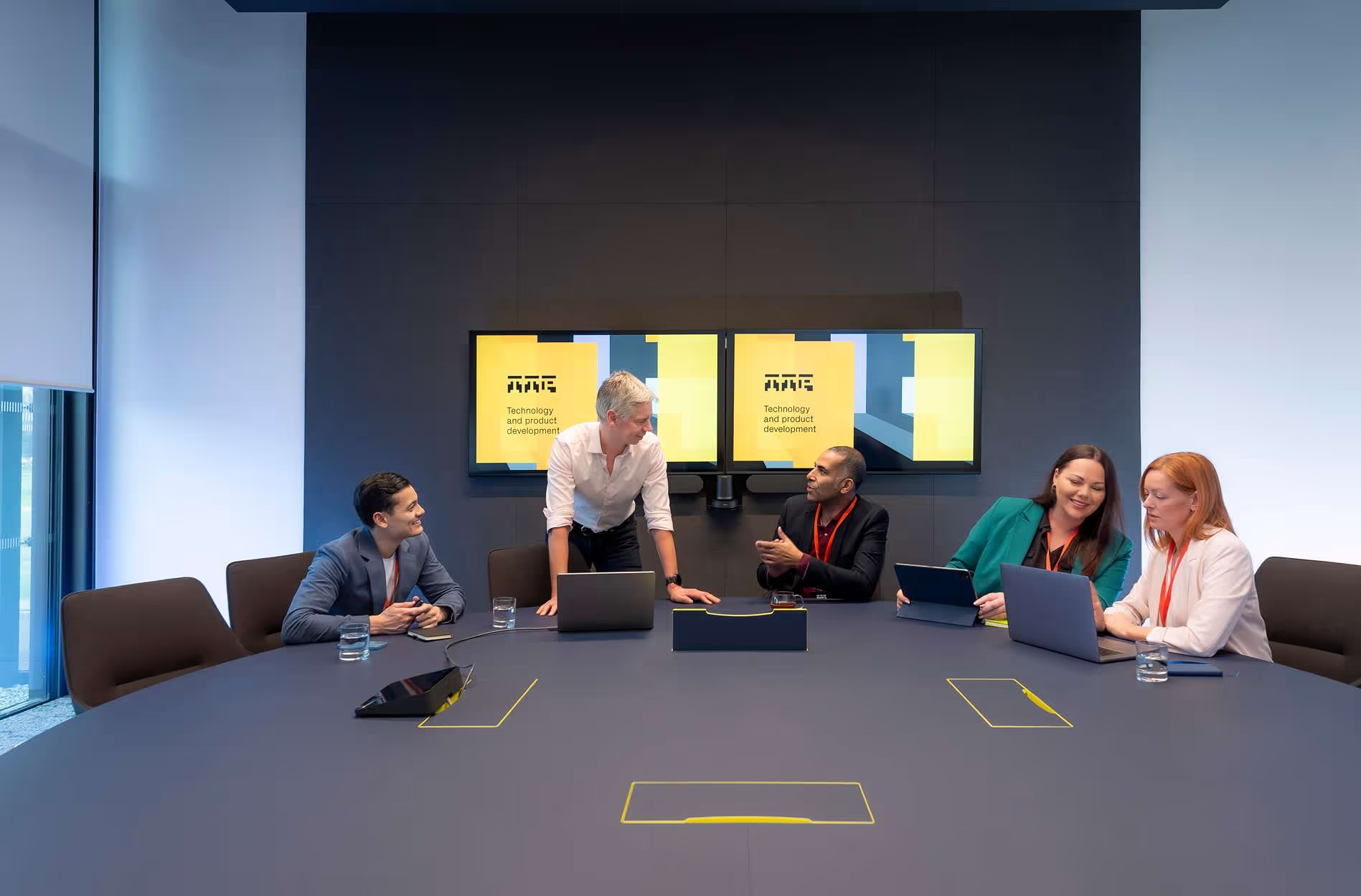