When PixelOptics hit roadblocks that made it challenging to turn its technology into a commercially viable product, TTP developed an alternative design to meet the value proposition.
Context:
PixelOptics wanted to create a new category product for the eyewear market: spectacle lenses with liquid crystals that switch focus in milliseconds, saving glasses wearers from changing to reading glasses.
Solution:
When the company’s technology proved difficult to scale, we worked with PixelOptics to develop an innovative but simpler lens design that is optically superior and easier to manufacture.
Result:
An ophthalmic-grade liquid crystal lens that allows the wearer to switch from distance to near vision, plus the full manufacturing line that enabled PixelOptics to bring its product to market.
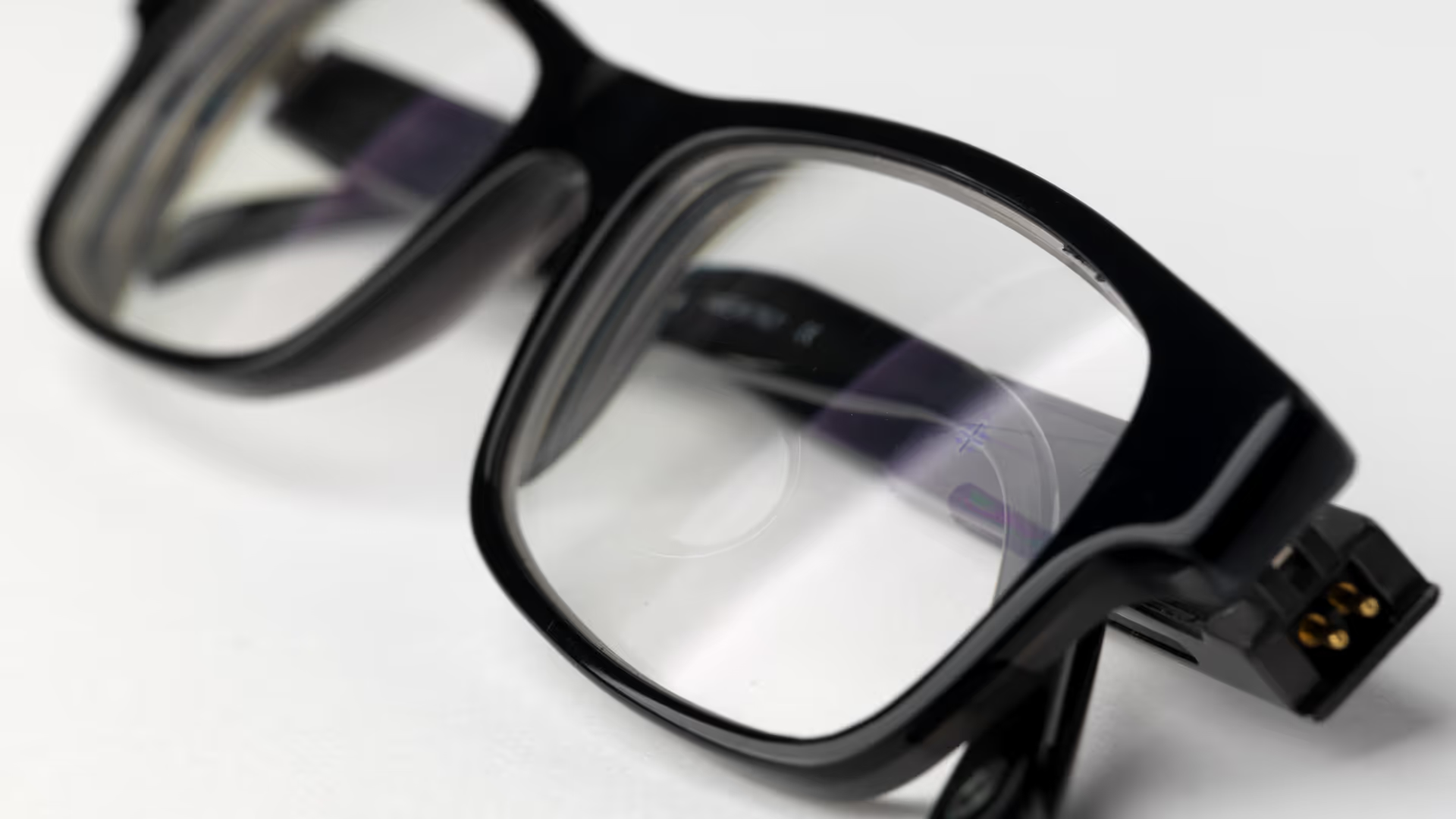
Liquid crystals for switchable lenses
PixelOptics wanted to develop spectacle lenses that incorporate liquid crystals (LCs) to allow the wearer to switch focus from distance to reading glasses at the flick of a switch.
LCs are typically rod-like molecules that align with one another but change orientation and optical properties – in particular the all-important refraction index – when an electric voltage is applied.
PixelOptics’ original design relied on patterning electrically conducting tracks to create a diffractive structure within a spectacle lens. Hundreds of micron-scale indium tin oxide (ITO) electrode structures were needed to turn the diffractive on/off in order to switch from far field to near field vision.
But as a manufacturing operation, the deposition of these ITO tracks onto a curved substrate was prohibitively expensive.
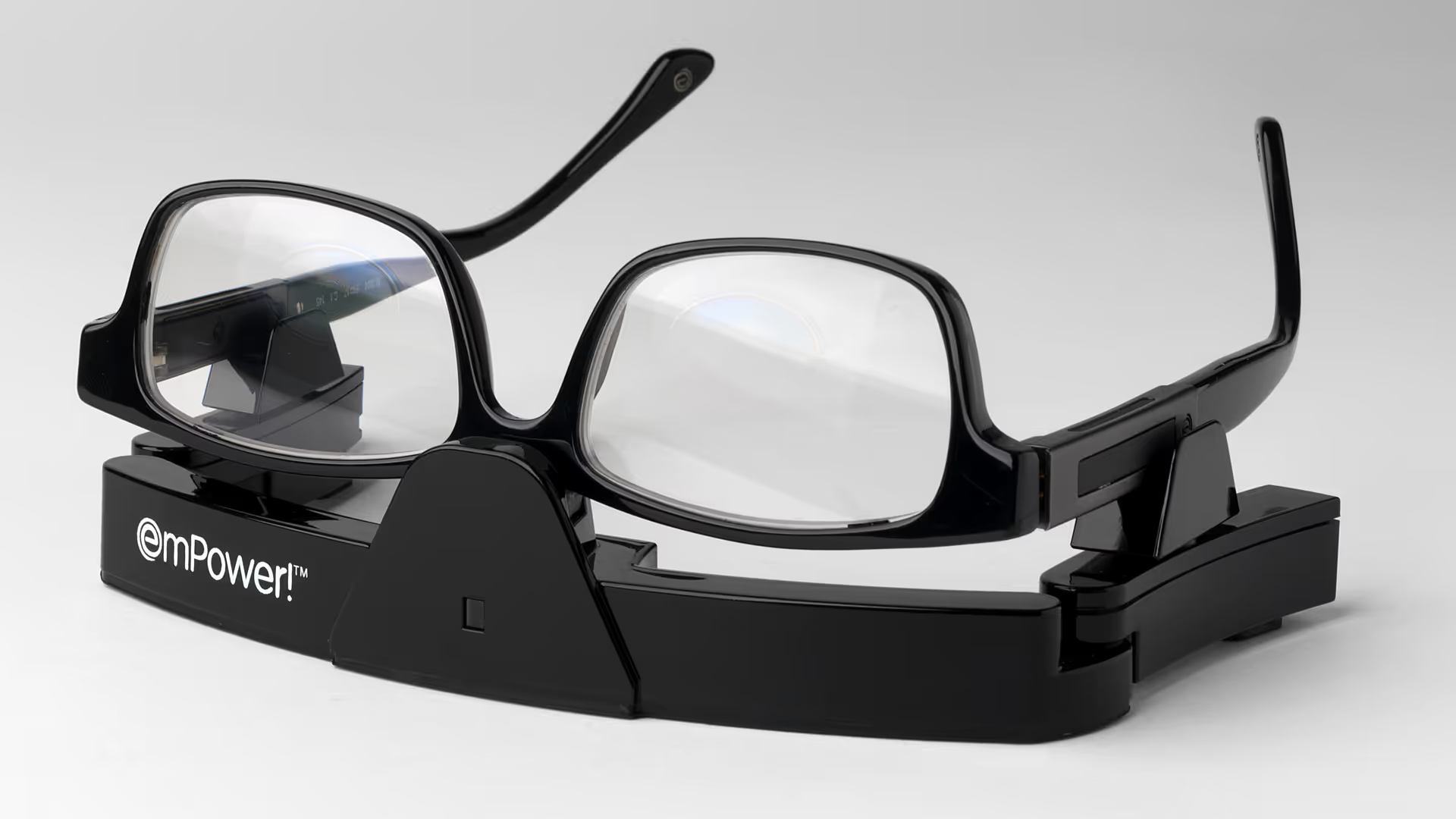
Simplicity at the heart of a new design
TTP’s key simplification was to combine a diffractive structure made from the lens plastic itself with a single LC layer.
Now, instead of requiring electronic control of multiple tracks, a single applied voltage changes the refractive index of a bulk LC layer to be either the same as, or different from, that of the plastic diffractive.
In this way, the new design retained the essential advantage of LCs – rapid switching of optical properties – but used them to turn on/off the optical effect of a physical diffractive.
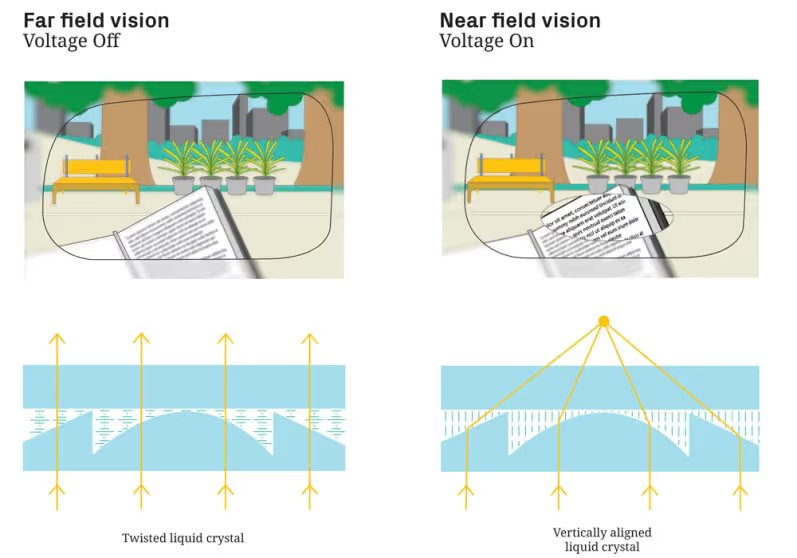
Multidisciplinary product innovation
TTP engineers with experience in all aspects of product development made sure that all decisions in the development of this design focused on functionality, aesthetics, manufacturability and ease of scale-up of the eventual product.
Achieving the necessary alignment of the LC molecules for haze-free performance in an ophthalmic product was critical and required the development of non-standard techniques and equipment. Parts of the diffractive edge profile were engineered to be smoother and flatter as a more optimal surface for LC alignment, whilst maintaining the high diffraction efficiency needed for a vision correction lens. Trimming the thickness of the diffractive also reduced power consumption.
Similarly the thickness of silicon dioxide layers that insulate the ITO was optimised with both functionality and aesthetics in mind to make the switchable LC cell less power hungry and to simultaneously act as an anti-reflectance layer to hide the diffractive structure inside the lens.
User testing complemented theory during product development
Success in commercial R&D often depends on finding the fastest route to a product that meets the value proposition – and taking unforeseen wins along the way. We did both when we evaluated the real-world performance of our design.
Taking advantage of newly available manufacturing technologies, we made test lenses with continuously varying diffractive properties to experimentally explore the optical performance as it appears to the human eye, rather than basing development decisions on theoretical expectations alone.
In an unexpected win, we found that the peak of the diffraction efficiency curve for optimum visual performance does not coincide with the peak sensitivity of the human eye (as previously assumed). This allowed us to further reduce the thickness of the diffractive, and thus power consumption and battery size, enabling frame designers to achieve the look, feel and performance of other commercial spectacles.
Simple and cost-effective manufacturing
At the end of the project, TTP shipped an advanced clean room to PixelOptics that contained all the manufacturing processes needed to make ophthalmic-quality switching lenses.
Much of our work for PixelOptics focussed on developing reliable manufacturing methods based on simple coating processes with industry-standard equipment.
Even in the early stages of this product development, we chose methods that were similar or identical to those used to manufacture the final product in order to allow for a seamless transfer to production.
Where the new technology meant that suitable equipment didn't exist, we developed new manufacturing and inspection instrumentation, for example to measure the diffractive efficiency and to monitor optical haze during high-speed switching.
TTP’s work put PixelOptics in the position of not only offering unique technology, but also being the only company that could produce a switchable lens simply and cost effectively.
Introducing a novel product into a competitive market with strict performance, cosmetic and cost constraints is no easy task. TTP’s cross-disciplinary team of eyecare experts delivered a solution that overcame technical challenges and seamlessly integrated with stylish lenses and frames on the market.
About TTP's Ophthalmology and Optometry consulting team
Building on 30 years of pioneering advancements in ophthalmology, we have collaborated with the industry’s top companies to create sector-defining products. Our deep domain expertise, paired with our unrivalled agility in execution, ensures we consistently deliver high-impact results for our clients. From novel optics for contact lenses and IOLs, to innovative drug delivery and surgical systems, we are always looking for ways to address patient, healthcare professional and industry needs. Find out how our team of ophthalmology technology experts can help you.
TTP's eyecare team is part of a broader Medical Device Consulting business unit. Read more about TTP's approach to medical device design and development.