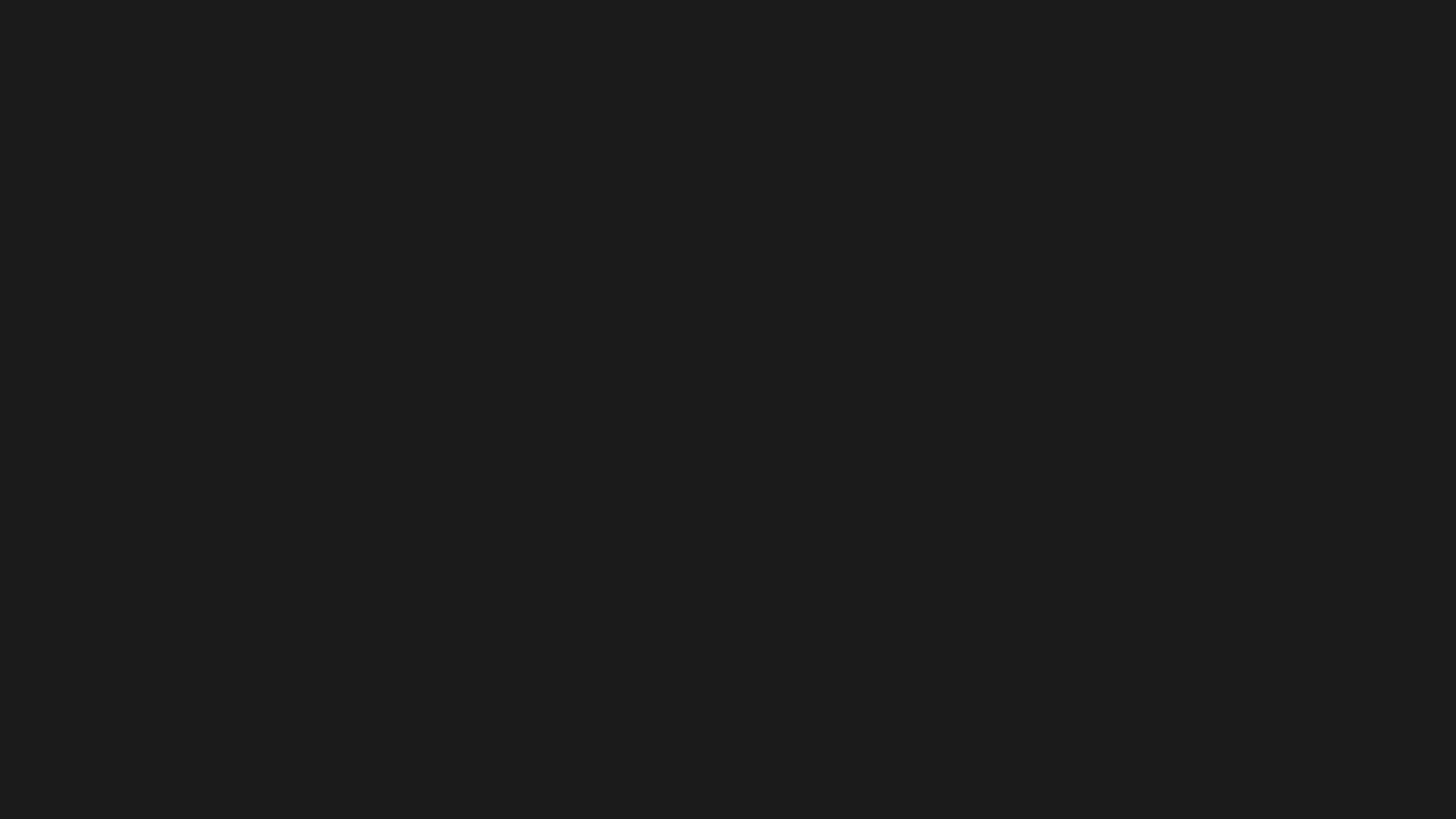
Bioprocessing
Enabling the commercialisation of breakthrough advanced therapies.
We bring unparalleled systems engineering expertise to the advanced therapies industry, supporting the development of life-enhancing therapies for patients. With over 20 years of market experience, we address complex bioprocessing challenges by resolving process bottlenecks, automating labour-intensive steps, and delivering solutions that not only address current challenges, but adapt to new ones as they arise.
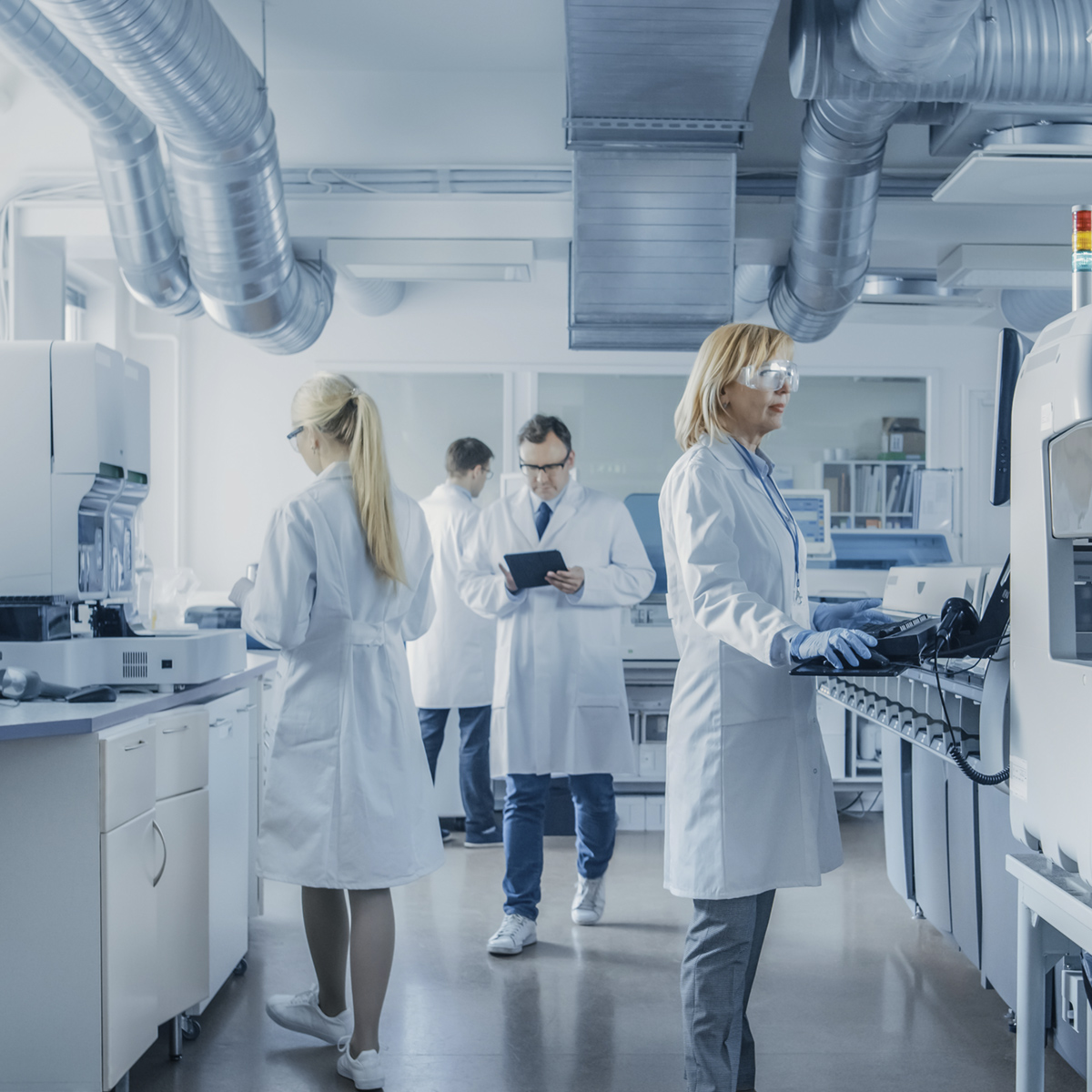
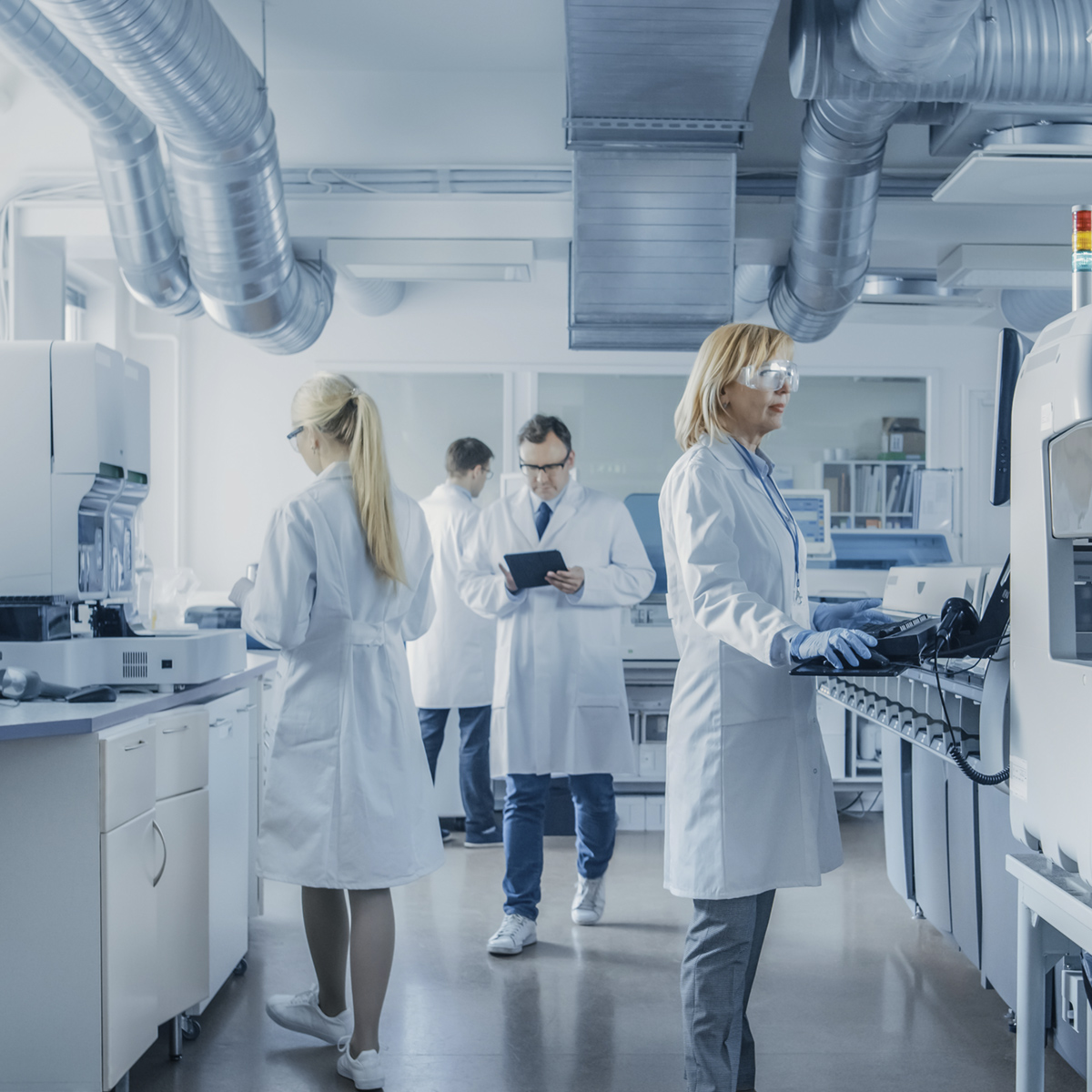
Robust, scalable bioprocessing solutions for clinical trials, commercial-scale manufacturing, and quality control
Advanced therapies have the potential to deliver life-enhancing treatments to a wide range of patient populations, but to achieve this vision, therapy developers need robust and scalable bioprocessing solutions to support clinical trials, commercial-scale manufacturing, and quality control through advanced analytics.
At TTP, we offer a unique approach to systems engineering for advanced therapy applications, applying fundamental scientific understanding to create solutions and develop products that scale seamlessly for commercial use. As a specialist developer of custom, scalable bioprocessing equipment, our focus is on enabling emerging modalities within advanced therapies to be developed, manufactured and released efficiently and cost-effectively.
Our biologists and engineers work hand in hand to ensure that automation enhances, rather than compromises, the biological performance of your therapy. With extensive experience in delivering fit-for-purpose solutions for regulated environments, we can minimise the demands on your team. Moreover, we are deeply invested in the industry’s success, having played a part in the genesis of some of the most innovative companies in the industry.
By partnering with TTP, you will add our expertise in bioprocess systems engineering to your knowledge of therapy development. Together, we can make a meaningful impact on patient wellbeing by broadening access to advanced therapies.
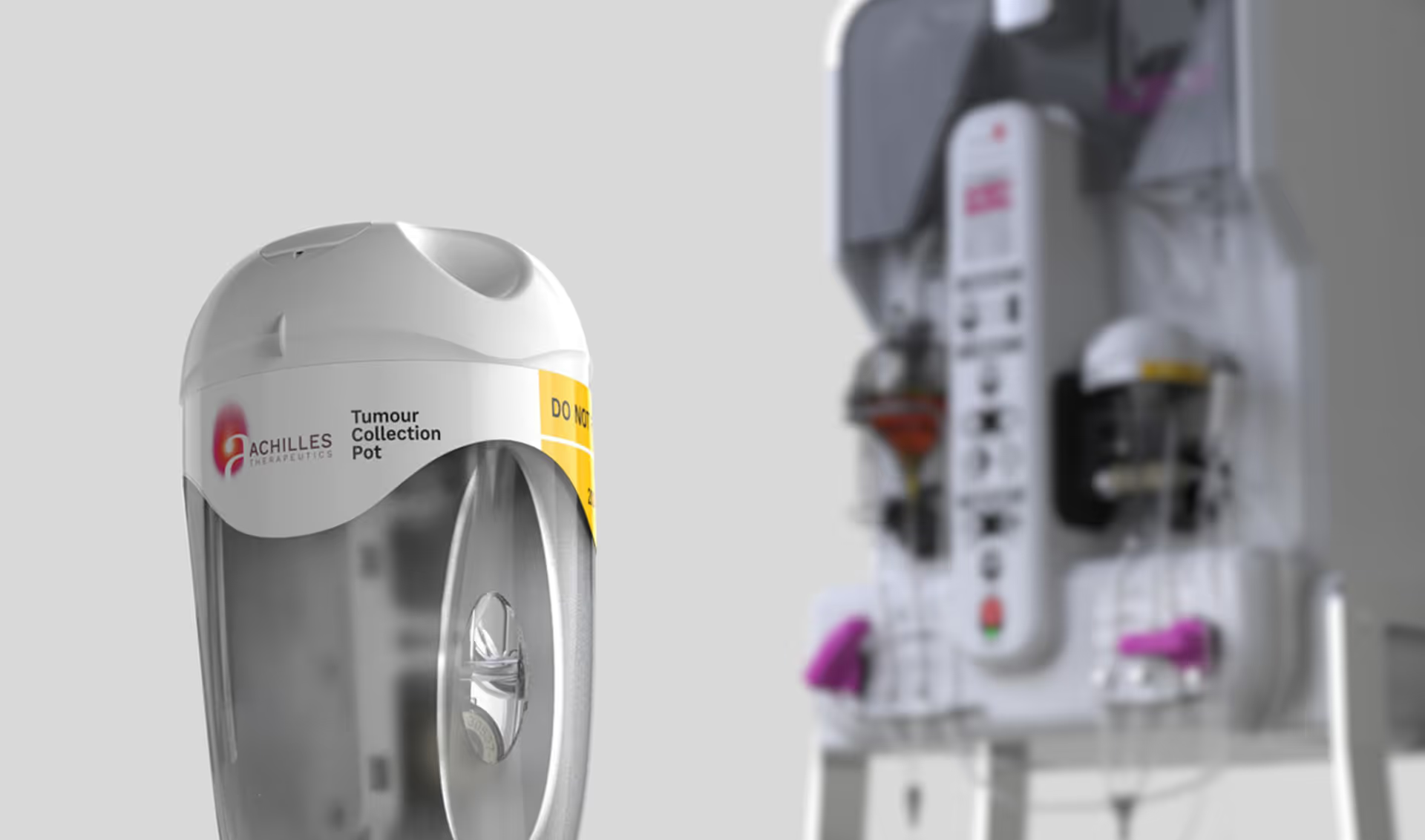
TTP has been an incredible partner, complementing our expertise and delivering designs from white board to moulded functional prototypes. With TTP’s support, Achilles is scaling our manufacturing process and bringing transformative therapies from bench to bedside. The TTP team has shown the same level of excitement as us in getting these therapies to the people who need them.
Ed Samuel
EVP Technical Operations
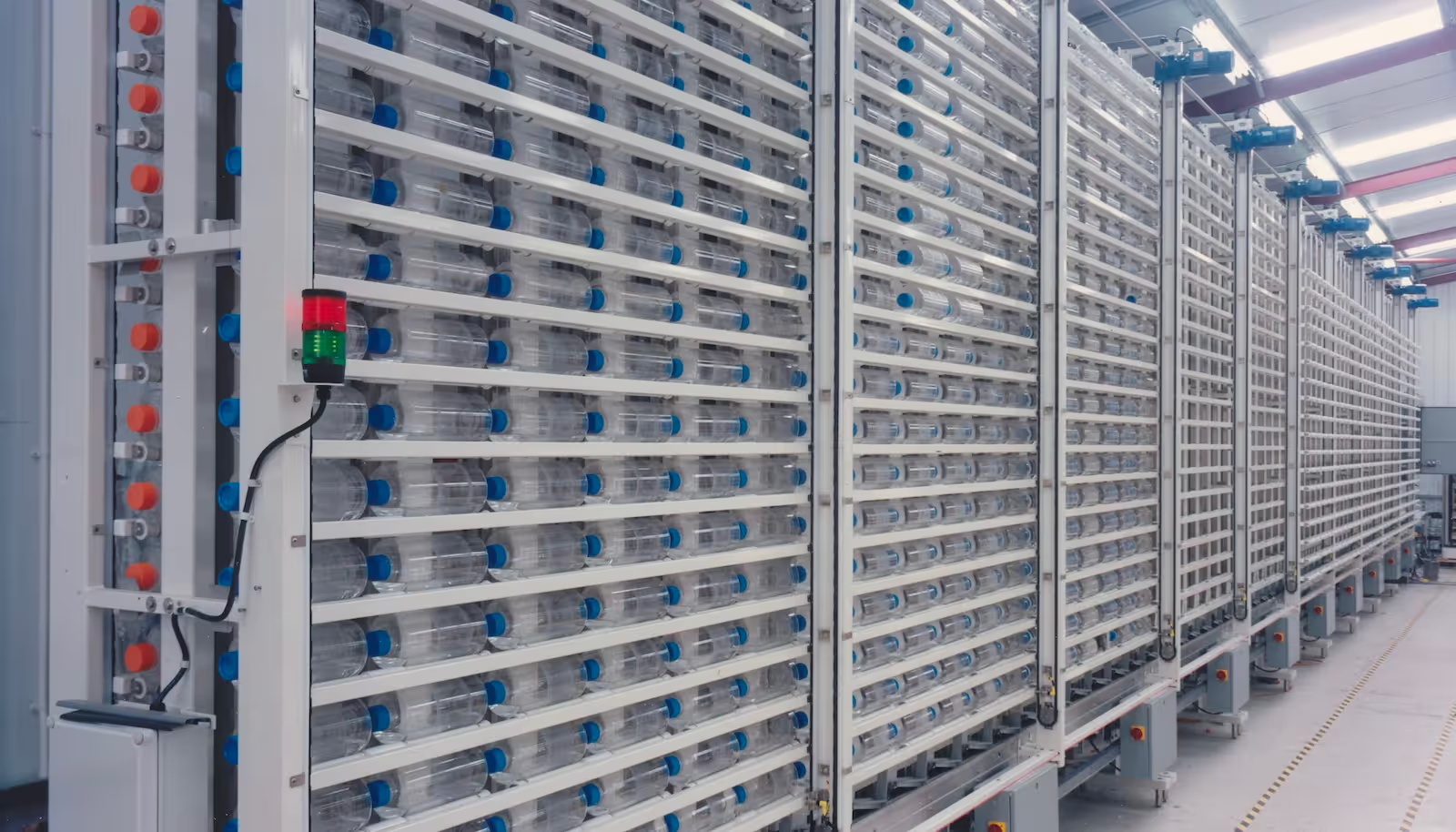
The system, potentially the largest undertaking in biotech manufacturing automation, required 25 man-years to develop and incorporates over 1 million components. While a significant investment, it’s noteworthy that its cost was less than a single day's EPO revenue.
Stephen Fleck
LabTech
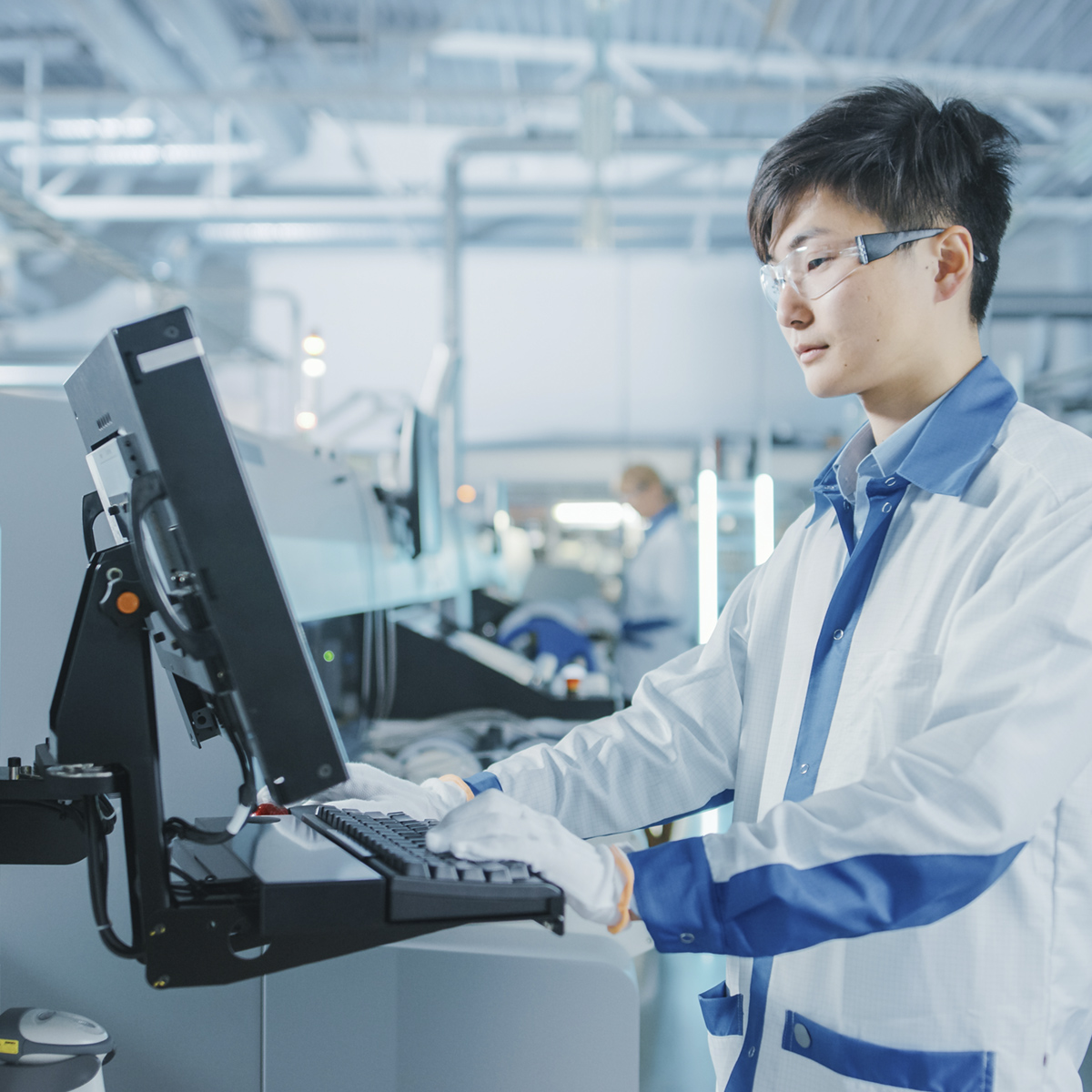
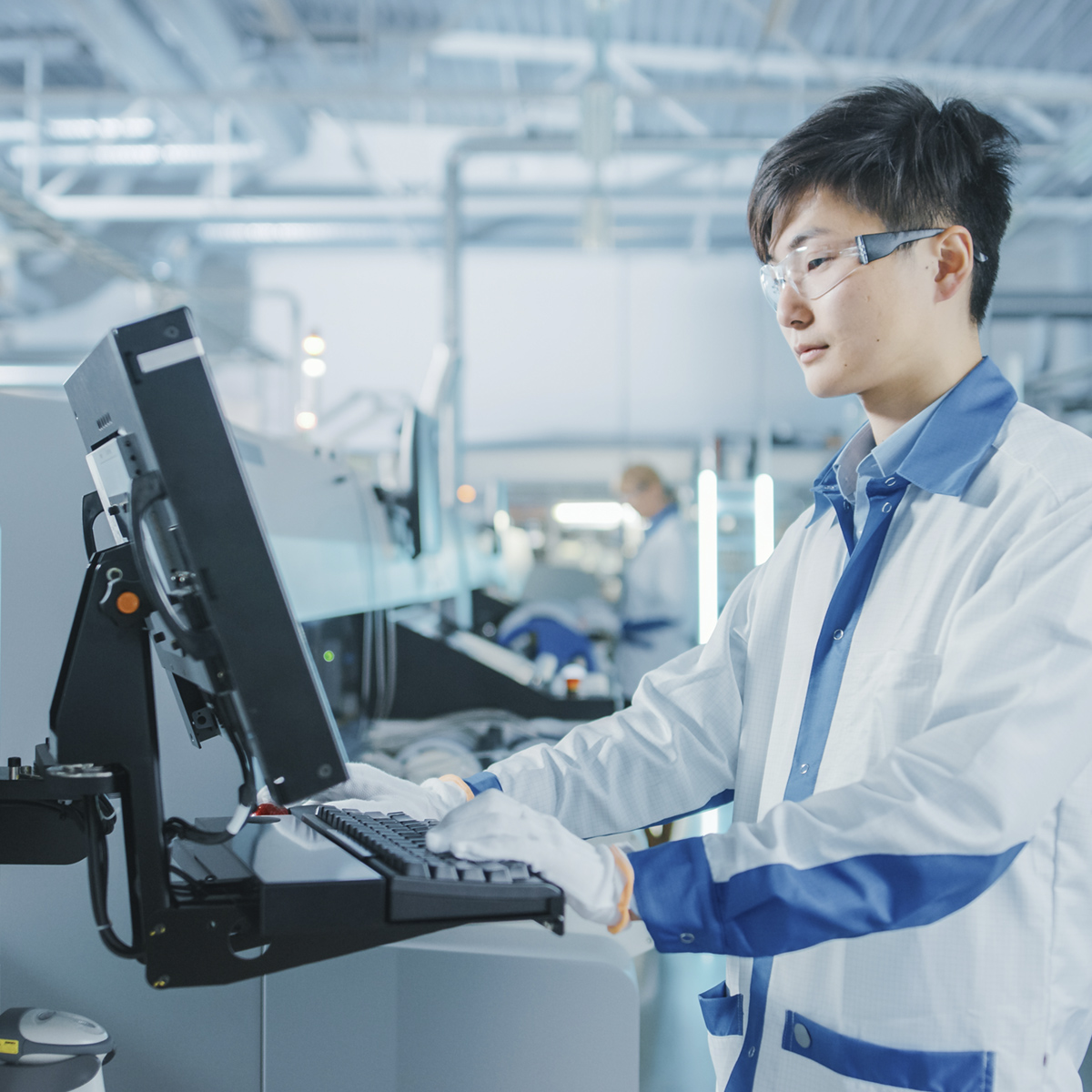
How we close, automate and digitise therapy manufacturing
To make a meaningful impact for patients, advanced therapies must be scaled to meet market demand.
Today's cell and gene therapy manufacturing approaches are developed using manual processes and legacy equipment. This often leads to commercial-scale manufacturing being dependent on specialised personnel, leading to increased costs and limited flexibility.
Automation has the potential to transform the way therapies are manufactured at scale. However the workflows used during therapy development and clinical trials are frequently ill suited for scaling to commercial production, creating obstacles in the path to efficient manufacturing. Finding off-the-shelf equipment that matches therapy developers’ specifications can be challenging.
TTP enables manufacturers to streamline their operations, moving from open to closed systems, manual to automated workflows, and empirical to digital methods. We deliver solutions that can transform pre-clinical workflows into scalable manufacturing processes, building on existing equipment with custom automation solutions as needed.
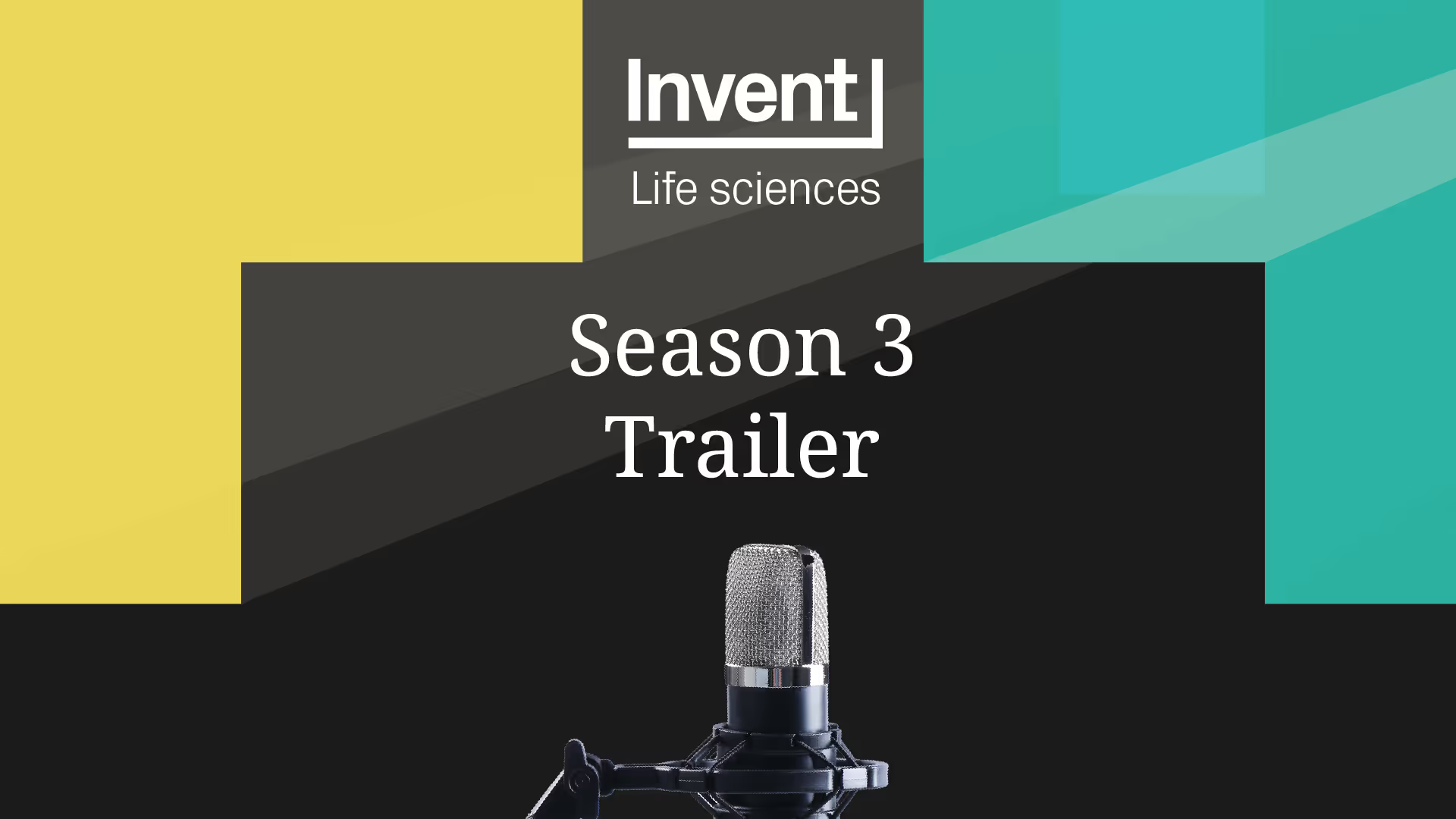
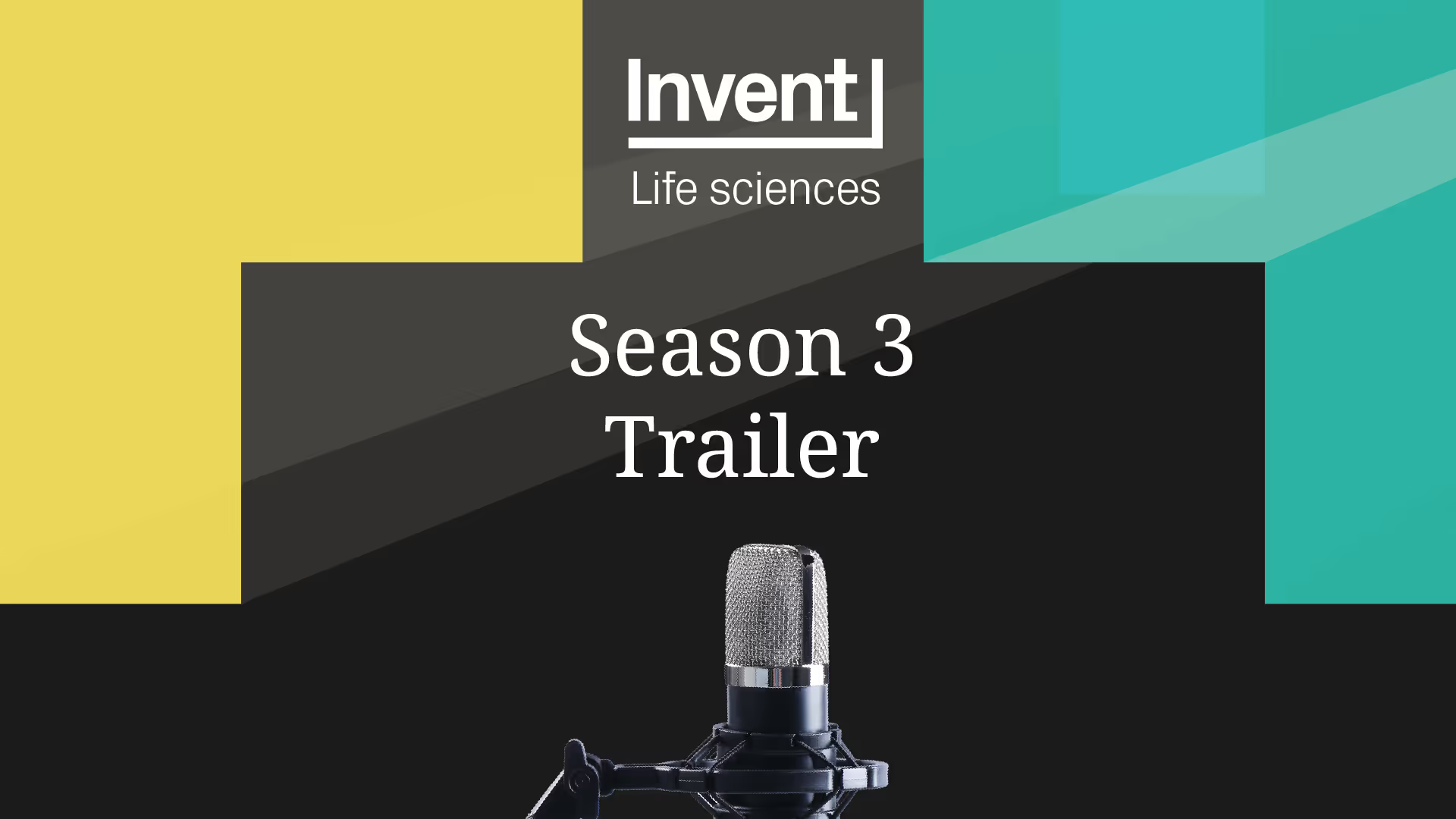
Invent: Life Science Podcast
Now back for its third season, TTP’s Invent: Life Science podcast uncovers the scientific and commercial insights behind cutting-edge developments within the Life Sciences industry. This season we’re throwing the spotlight on the remarkable potential of the cell and gene therapy industry.
With approvals for advanced therapies on the rise and ambitions to reach larger patient populations, it's the perfect time to take stock of the progress we've made so far and ask ‘what’s next?’. In our latest series, we'll discover the people, processes, and partnerships needed to build the future of this industry and deliver the best outcomes for the greatest number of patients.
How we can help
Close and automate labour intensive processes
There's a need for specialist equipment designed to reduce labour-intensive processes in the production of therapies during clinical trials.
We specialise in developing systems that enable closed processes, allowing them to be operated in lower-grade facilities while also reducing hands-on time. This frees up resources and helps reduce labour costs.
Our competencies span human factors engineering, industrial design, single-use consumable design, fluidics, electronics, control software, and facility layout.
Scale up and scale out
A lack of suitable manufacturing equipment complicates the transfer from process development to manufacturing, impacting timelines, costs, compliance, and the integrity of clinical trials.
We bridge this gap by designing scalable solutions from the start, avoiding hard-to-scale elements, and balancing trade-offs between scaling up and scaling out.
We excel in consumable design, test plans for GMP-compliant equipment, and in-house prototyping which supports rigorous testing and seamless transfer to contract manufacturers for large-scale production.
Technology evaluation and selection
Each therapy has unique production needs, making it hard to find ready-made systems for large-scale output.
We assess automation potential to identify subprocesses most suitable for automation, whether through off-the-shelf equipment, adaptation of our proprietary IP, or de novo bioprocess automation development. This approach allows early automation benefits without heavy upfront investment.
Our capabilities span, first-principles modelling, test rig development, biophysics assessments, industrial design, single-use consumable design, fluidics, electronics, software, and facility layout.
Process analytical technology (PAT)
Ensuring product quality requires equipment with sophisticated analytical tools for detailed characterisation data.
As regulations demand more data for IND submissions and the use of automation increases, integrating advanced analytics into automated systems is increasingly important. This may involve adapting existing sensors, developing new assays, or utilising AI-driven data analysis.
We apply expertise from diverse industries, covering sensor design, biochemistry, optics, electronics, machine learning, fluidics, consumable design, prototyping, manufacturing, and technology landscaping for sensor assessment and evaluation.
Close and automate labour intensive processes
There's a need for specialist equipment designed to reduce labour-intensive processes in the production of therapies during clinical trials.
We specialise in developing systems that enable closed processes, allowing them to be operated in lower-grade facilities while also reducing hands-on time. This frees up resources and helps reduce labour costs.
Our competencies span human factors engineering, industrial design, single-use consumable design, fluidics, electronics, control software, and facility layout.
Scale up and scale out
A lack of suitable manufacturing equipment complicates the transfer from process development to manufacturing, impacting timelines, costs, compliance, and the integrity of clinical trials.
We bridge this gap by designing scalable solutions from the start, avoiding hard-to-scale elements, and balancing trade-offs between scaling up and scaling out.
We excel in consumable design, test plans for GMP-compliant equipment, and in-house prototyping which supports rigorous testing and seamless transfer to contract manufacturers for large-scale production.
Technology evaluation and selection
Each therapy has unique production needs, making it hard to find ready-made systems for large-scale output.
We assess automation potential to identify subprocesses most suitable for automation, whether through off-the-shelf equipment, adaptation of our proprietary IP, or de novo bioprocess automation development. This approach allows early automation benefits without heavy upfront investment.
Our capabilities span, first-principles modelling, test rig development, biophysics assessments, industrial design, single-use consumable design, fluidics, electronics, software, and facility layout.
Process analytical technology (PAT)
Ensuring product quality requires equipment with sophisticated analytical tools for detailed characterisation data.
As regulations demand more data for IND submissions and the use of automation increases, integrating advanced analytics into automated systems is increasingly important. This may involve adapting existing sensors, developing new assays, or utilising AI-driven data analysis.
We apply expertise from diverse industries, covering sensor design, biochemistry, optics, electronics, machine learning, fluidics, consumable design, prototyping, manufacturing, and technology landscaping for sensor assessment and evaluation.
Our approach and capabilities
We deliver across the entire life of a project, from opportunity discovery to production engineering. Discover how our interdisciplinary teams of experts collaborate to tackle the toughest product development challenges.
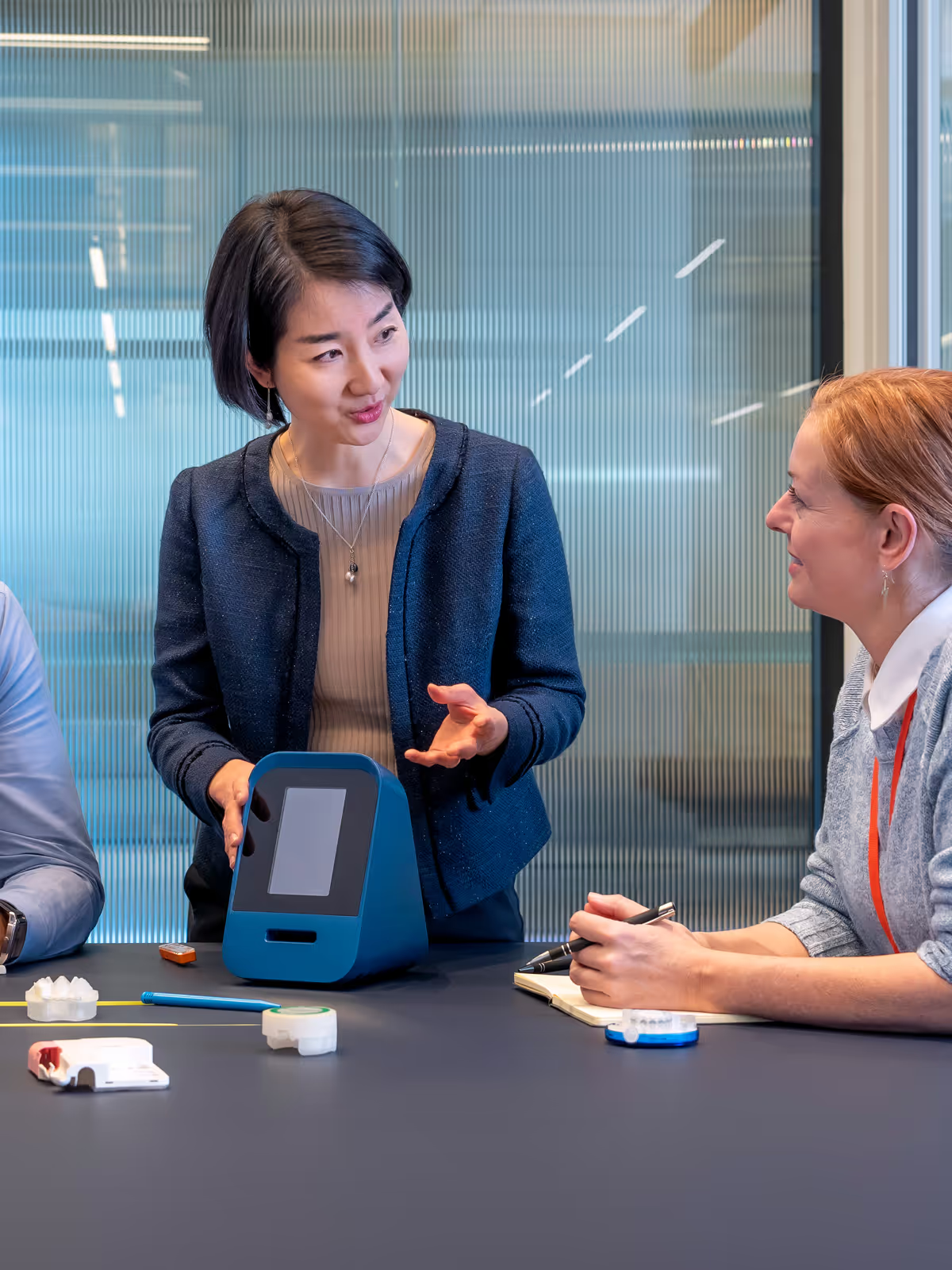
Our campus and facilities
Our award-winning campus has been designed with a clear vision. To create a space which can support our people and our clients as we develop and deliver the very best technology solutions.
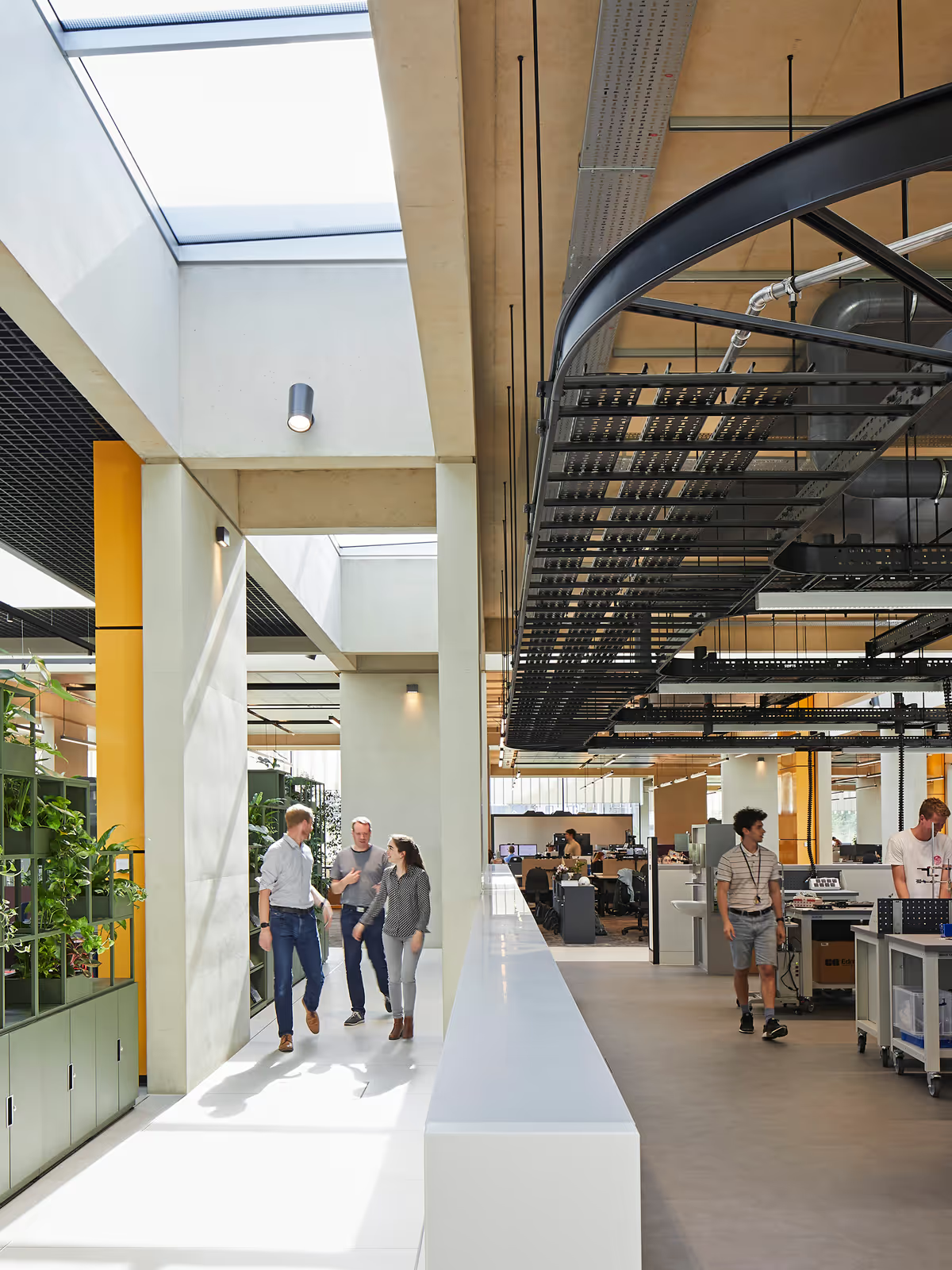
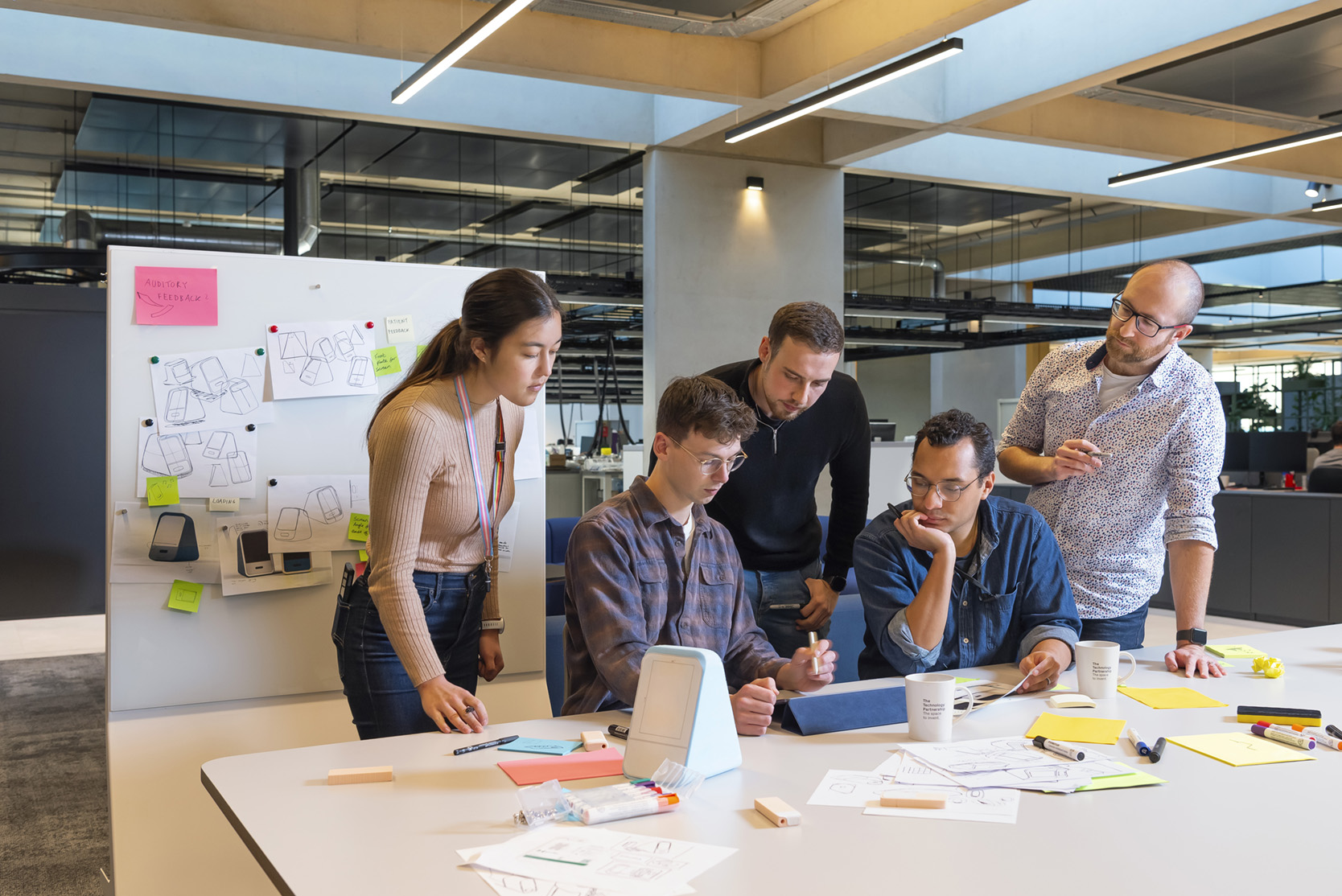
Software capability at TTP
Engaged in all stages of software and product development, our software capability at TTP covers the full spectrum—from in-depth analysis and system architecture to prototype design, implementation, and test development.
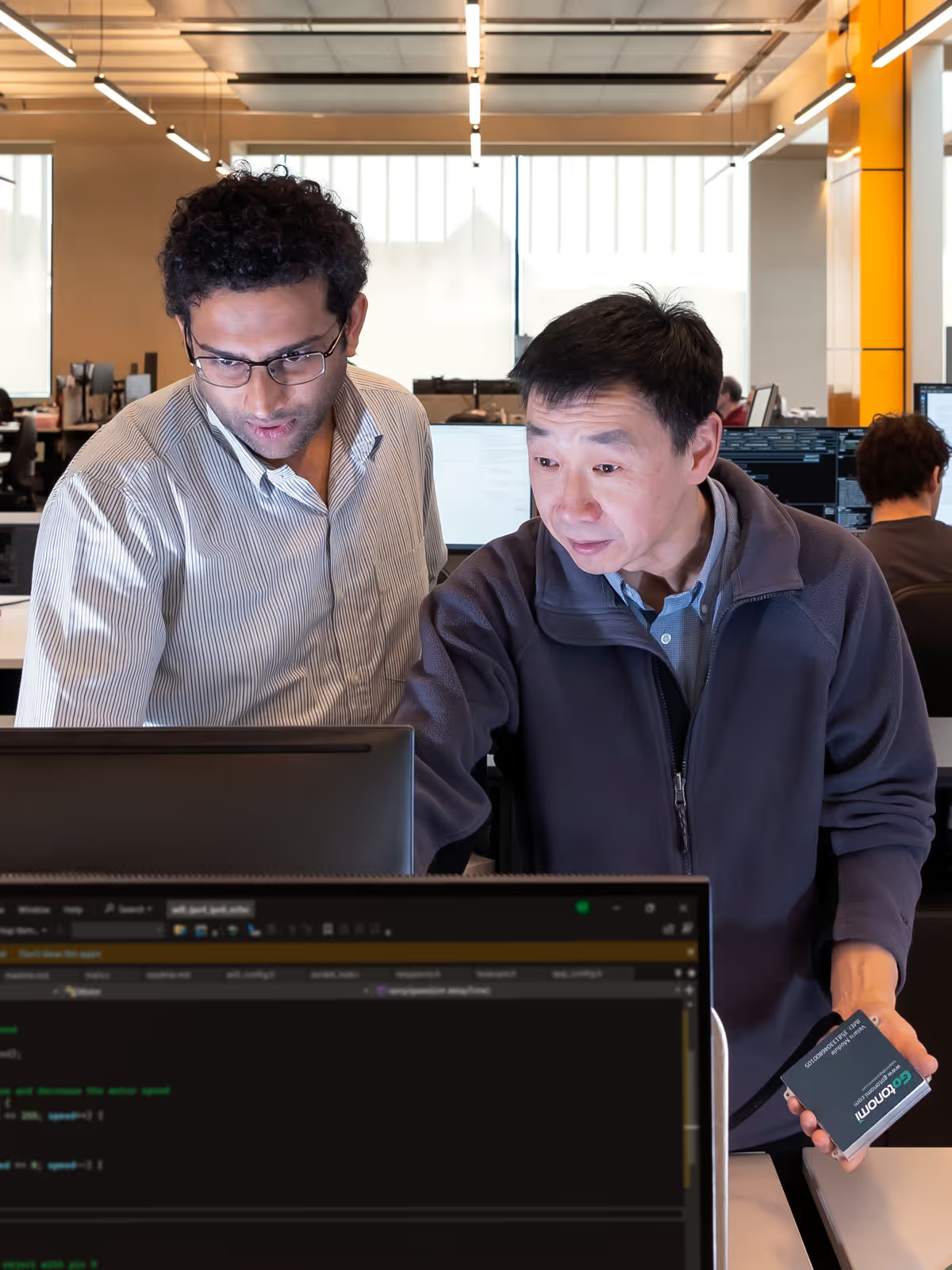
Manufacturing capability at TTP
Working seamlessly with our development teams, we take clients' products through prototype builds, clinical trials, pilot manufacture and more. Using TTP Manufacturing reduces uncertainty, risk and time to market for our clients.
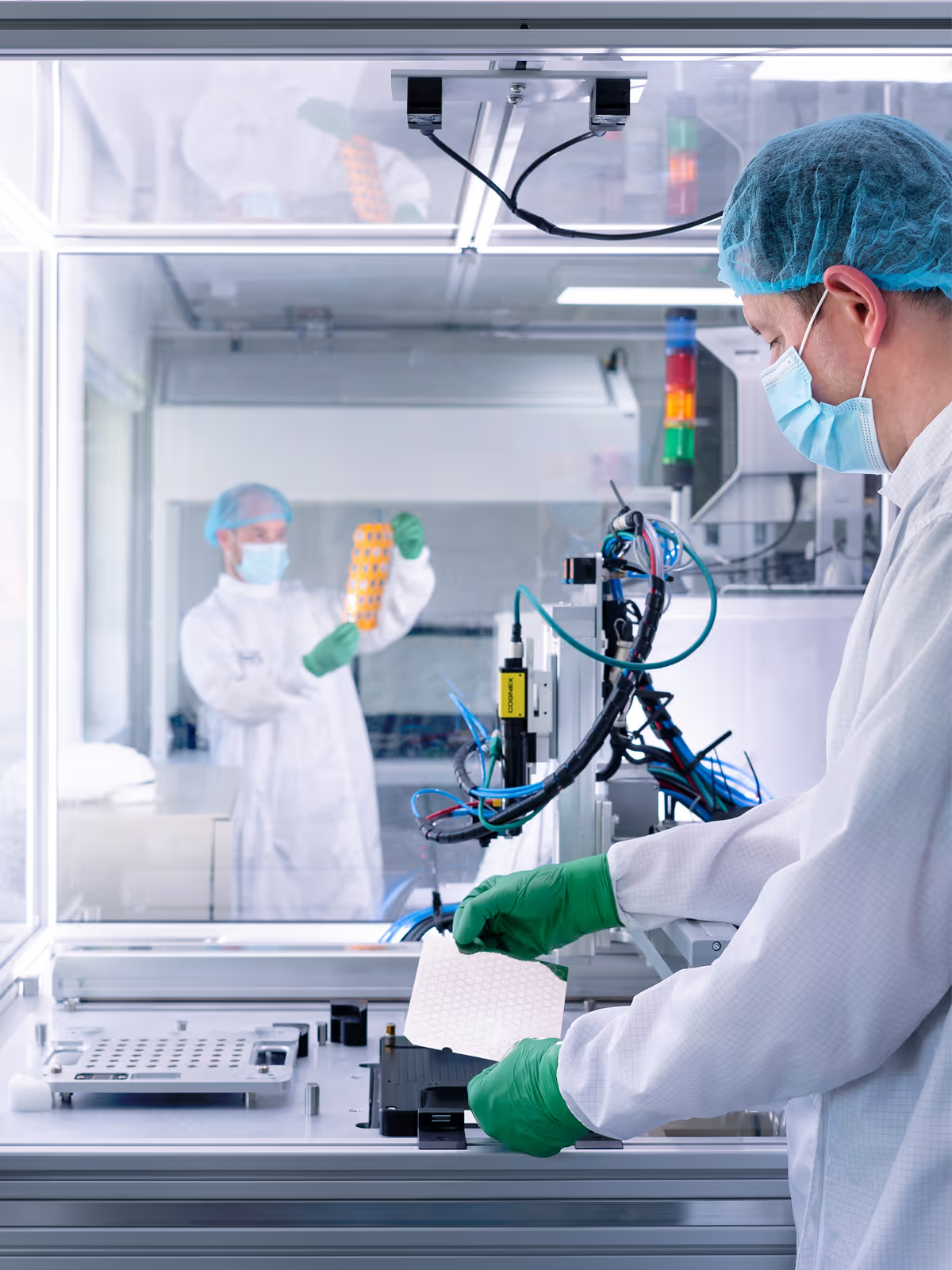
Meet some of the team
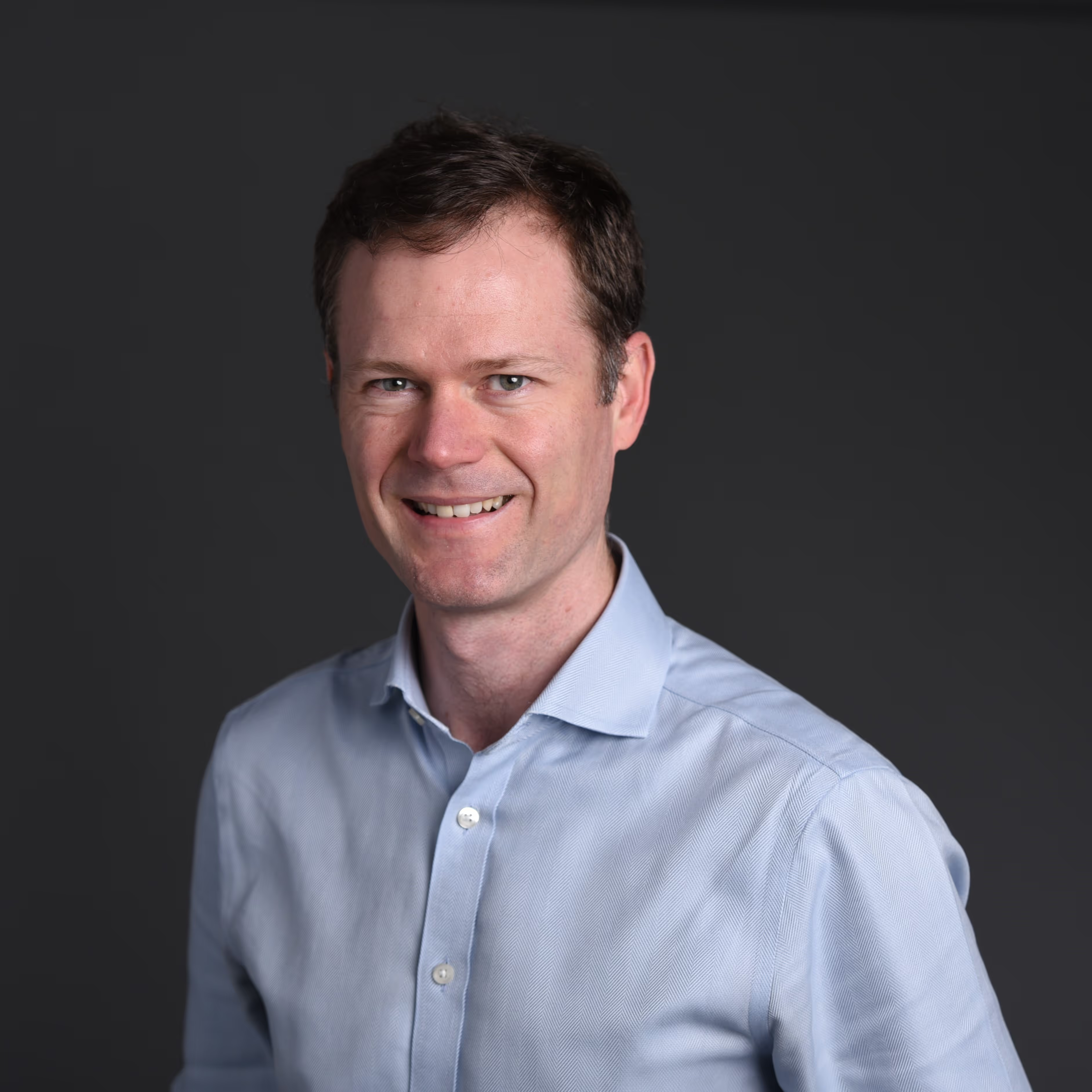
Stuart Lowe
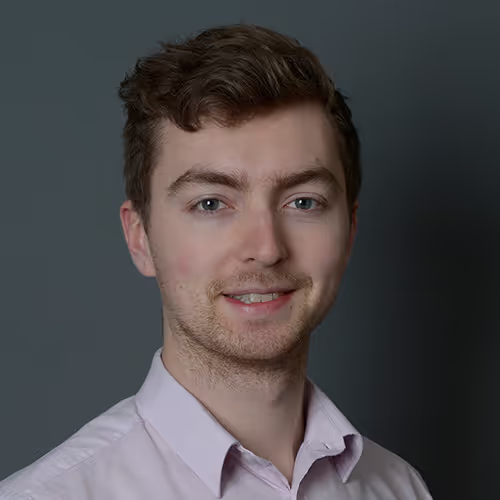
Tom Broughton
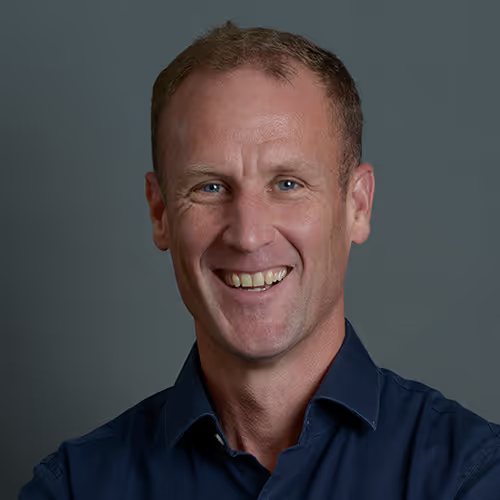
Douglas Bradshaw
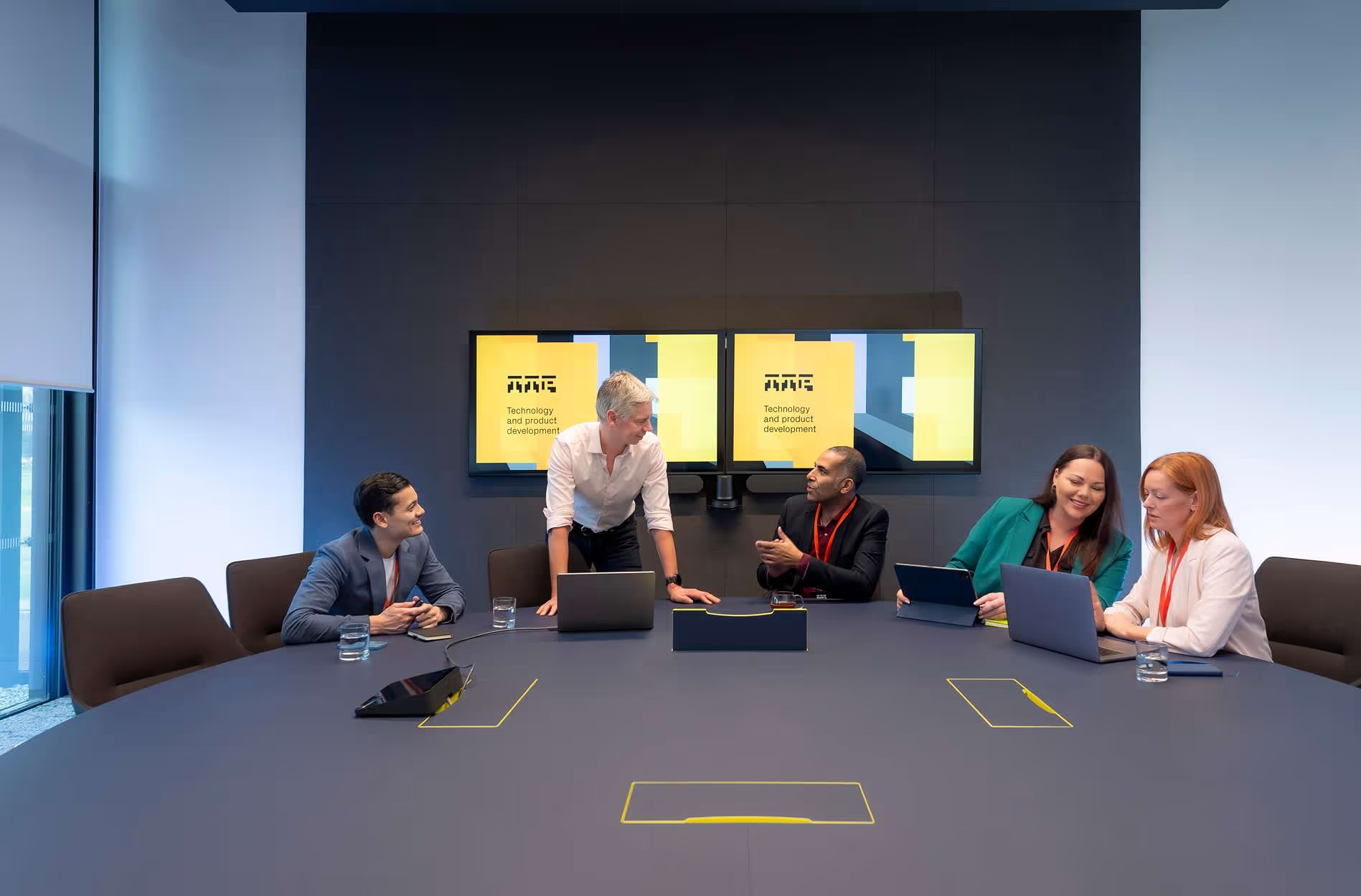