Achilles Therapeutics asked TTP to help scale up the manufacturing of their transformative autologous cell therapy in order to treat more patients with cancer.
Context
Achilles Therapeutics is a revolutionary company pioneering the development of autologous cell therapies for the treatment of solid cancers. To deliver its therapies to more patients, Achilles Therapeutics needed a scalable manufacturing system that extends all the way from tumour sample collection in the operating room to therapy manufacturing in the GMP (good manufacturing practice) facility.
Solution
To make this happen, TTP brought together medical device and human factors experts with specialists in advanced therapy manufacturing. We developed a novel tumour sample collection device and base station, the NeoPOD®, that work together to provide integrated tissue processing and transfer to downstream manufacture while maintaining a closed system throughout.
Result
Implementing the NeoPOD® device in clinical trials will reduce manufacturing costs whilst making Achilles Therapeutics’ life-changing cell therapies more scalable and thus improve accessibility for many more cancer patients.
The patented NeoPOD® platform solution is also designed to be adaptable to Achilles Therapeutics’ future needs and differing requirements for multiple therapeutic indications.
TTP has been an incredible partner, complementing our expertise and delivering designs from whiteboard to moulded functional prototypes. With TTP’s support, Achilles Therapeutics is scaling its manufacturing process and bringing transformative therapies from bench to bedside. The TTP team has shown the same level of excitement as us in getting these therapies to the people who need them.
Ed Samuel
EVP Technical Operations, Achilles Therapeutics
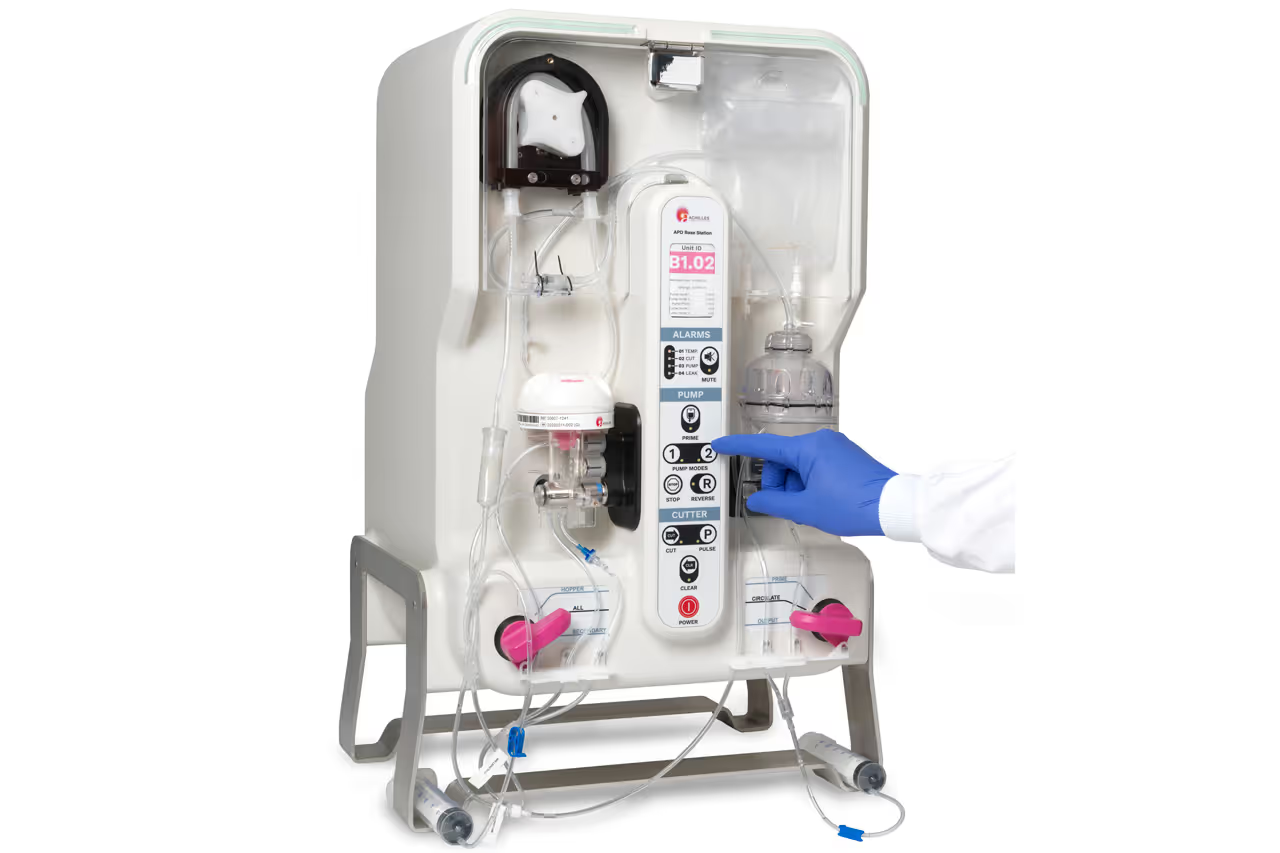
To bring their advanced personalised therapies to cancer patients, cell therapy companies need scalable manufacturing solutions.
Typically, a viable sample of the patient's blood or tissue needs to be transported to a facility where the personalised therapy is manufactured. Once these products obtain regulatory approval, sample management can become a major obstacle for scaling manufacture for thousands of patients.
For Achilles Therapeutics’ therapies, manual preparation of a single tumour sample can take in excess of 60 minutes in a cleanroom. Manual processing also introduces variability and makes manufacturing expensive to scale.
A scalable solution
TTP's Drug Delivery consulting team worked with Achilles Therapeutics to develop an integrated manufacturing system comprising a sample collection device that docks into a benchtop base station for sample processing. From the moment the lid is placed on this device, it becomes part of a closed manufacturing process until the patient receives their personalised therapy.
Making the collection device simple to integrate with the base station is key to enabling manufacturing scale-up in a GMP setting. Armed with end user insights from Achilles Therapeutics’ GMP team, TTP designed a streamlined tubeset connection workflow and a simple, intuitive docking arrangement.
The closed system architecture was validated to ensure best-in-class usability, simplicity and GMP compliance. This rigorous approach was part of a larger programme including development of the tissue sample processing technology, feasibility and verification testing.
Designed for reliability
By protecting precious tumour tissue samples and enabling automated tissue processing, the NeoPOD® system seamlessly integrates with GMP manufacturing and eliminates the variability inherent in manual sample prep.
The base station of the NeoPOD® manufacturing system needs to automate and standardise tumour sample processing to meet the specific requirements for Achilles Therapeutics’ therapies.
To this end, TTP’s engineering team developed a novel tissue disaggregation technology to accommodate broad variation in the physical properties of tumour tissue, maintain the viability of Tumour Infiltrating Lymphocytes (TIL) embedded in the tissue and to be configurable for different solid tumour indications.
TTP used its biomechanics and fluidics expertise to design modular elements that achieved these challenging objectives: by limiting the shear forces imparted on cells, controlling the minimum tissue fragment size and separating the preferred tissue compartments that are relatively high in viable cells from unwanted tissue.
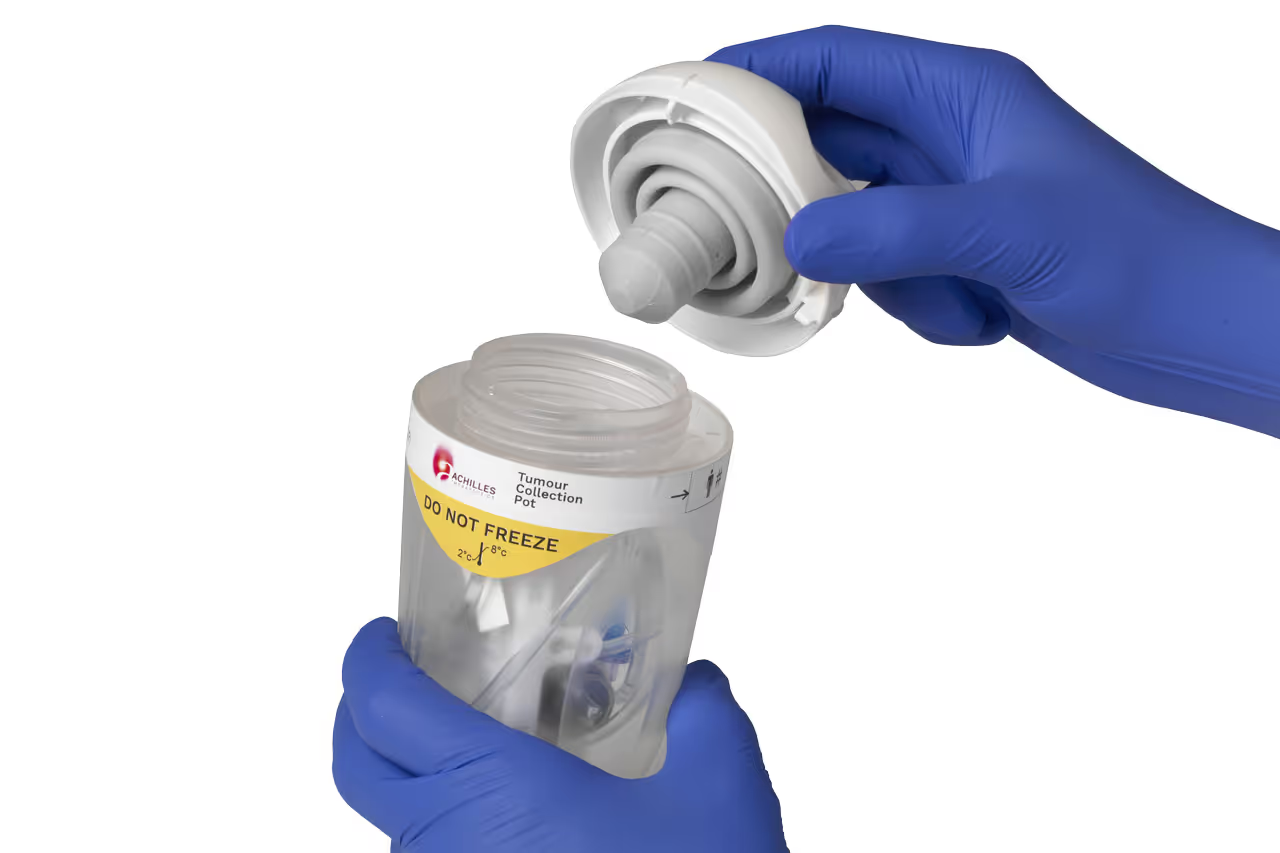
Designed for usability
For most clinical users, the collection of tumour samples to manufacture autologous cell therapy will be a new and unfamiliar procedure. Any mistake in handling the sample risks the survival of the cells and, ultimately, the patient.
TTP’s Human Factors team assessed the clinical workflow to discover the needs of surgeons and nurses who harvest the tissue in the Operating Room and despatch it to the GMP manufacturing site.
Understanding the needs and expectations of clinical users was fundamental to designing a sample collection device that mitigates against common use errors and clinical risks through its physical design.
Design development was guided through formative inputs from simulated use testing with HCPs. User testing also provided objective evidence of safety, effectiveness, and ease of use to support the manufacturer’s IEC 62366 Usability Engineering File.
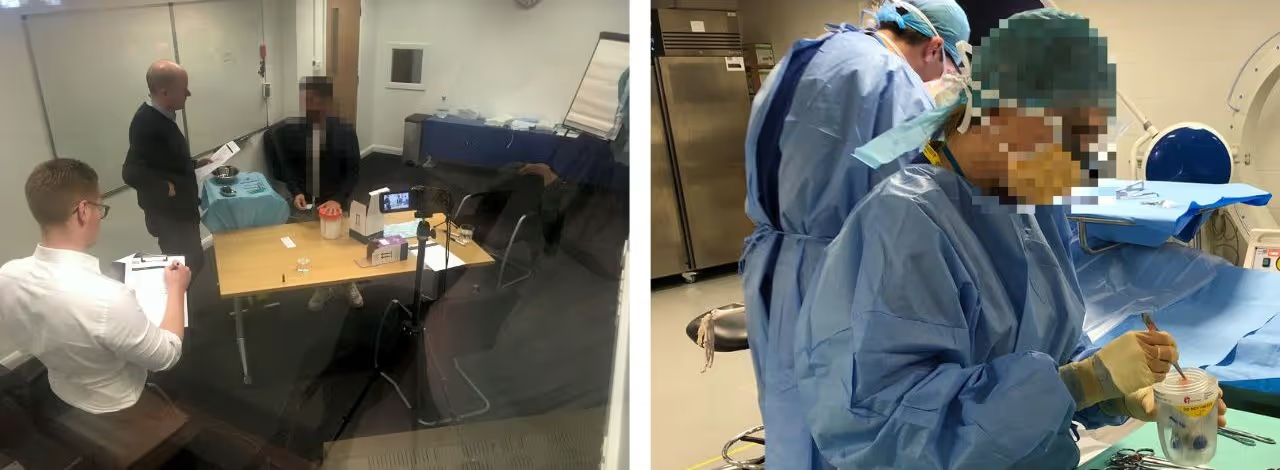
Communicating Achilles Therapeutics' mission
The NeoPOD® manufacturing system is also designed to be recognised for what it is: “a trustable, innovative manufacturing system for Achilles Therapeutics’ transformative therapies.”
TTP’s Industrial Design team developed a brand language to create a harmonious and meaningful design that conveyed this message across the products associated with the system. The result is a hardware design that not only functions brilliantly but communicates its technical elegance and therapeutic sophistication on first appearance.
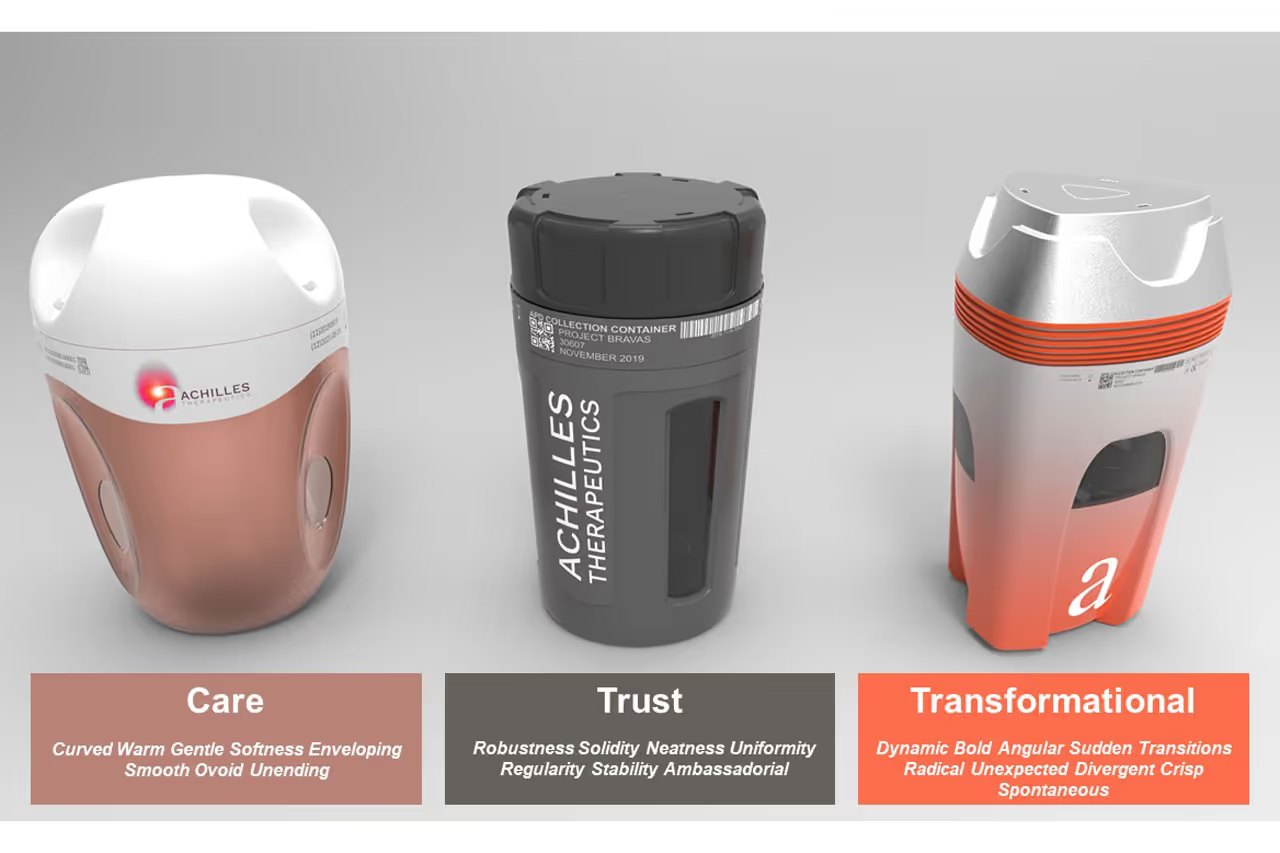
Better access to advanced cell therapies
TTP’s expertise in medical device design and development and advanced therapy manufacture enabled Achilles Therapeutics to develop an innovative system that reduces manufacturing cost whilst improving reliability (repeatability) and scalability, making personalised life-changing therapies accessible to many more cancer patients.
The platform technology developed by TTP allows Achilles Therapeutics to modify and adapt the system to accommodate different tissue processing requirements whilst enabling further automation of the manufacturing setup, as Achilles Therapeutics progresses from clinical trials to commercialisation.
TTP continues to support Achilles Therapeutics in its future developments.
About TTP's Drug Delivery consulting team
From blank sheet to clinical reality, TTP's Drug Delivery Design and Development team creates ground-breaking solutions to solve the toughest drug delivery challenges. With deep engineering, human factors, and scientific expertise, we guide you through every stage of drug delivery device development - from early exploration to manufacturing and final launch. Backed by an extensive track record we expertly navigate constraints to develop robust, efficient, scalable devices - enabling the delivery of transformative therapies and enhanced patient experiences.
Find out how we can help you with your drug delivery consulting needs.
TTP's Drug Delivery team is part of our broader Medical Device Consulting team, consisting of 300+ engineers, scientists, and human factors specialists. For nearly four decades we've partnered with clients to develop impactful solutions, helping them achieve commercial success.