Zellweger wanted to update its products in gas detection in line with the latest industry standards. The company determined that outsourcing the development would offer the quickest return on its investment and selected TTP for the development.
Context
Health and safety legislation requires the installation of gas detection equipment where there is a risk of a gas leak or where gases may accumulate at levels that would pose an unacceptable level of danger.
Solution
Exploiting economies of scale and modular design, TTP translated a set of high-level market requirements into a new suite of products for the certified and uncertified gas detection markets.
Result
The development was completed within two years, including manufacturing transfer to the Far East with final assembly in the UK.
We translated a set of high-level market requirements into a suite of new products that would serve the certified and uncertified gas detection markets. The new product line utilised economies of scale, enabling many new products by taking advantage of modular elements, including in software, electronics and mechanical components.
A further requirement was to ensure that the products were developed in accordance with a product lifecycle management standard, specifically IEC61508.
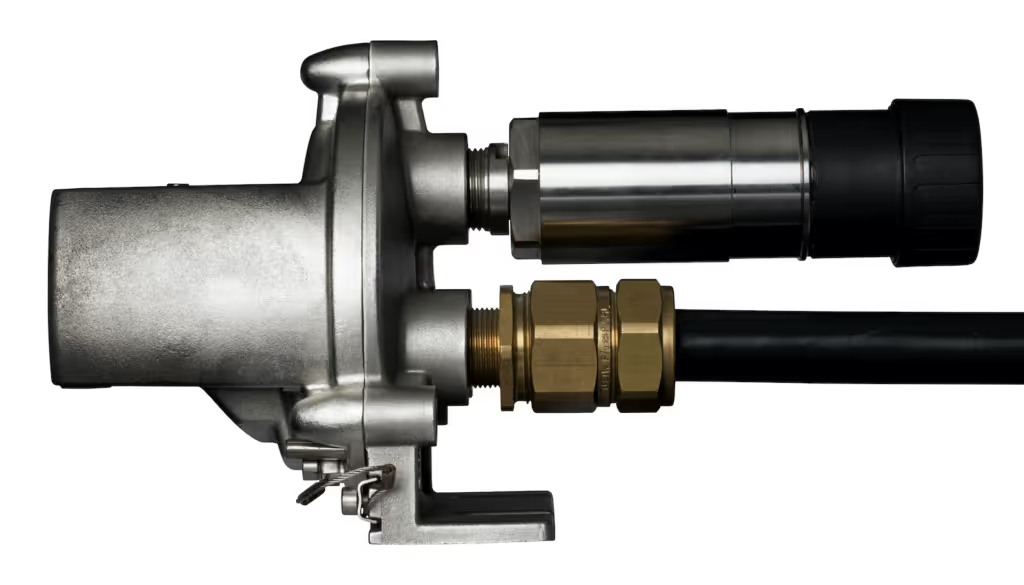
Zellweger’s revamped product line-up offered many new and innovative features, including improved user interface, hot-swappable sensors, high-integrity field-bus communications, as well as certification to a range of internationally recognised standards.
TTP has since developed other products requiring hazardous area approval, including portable gas detectors and gas distribution equipment.