Nium worked with TTP to scale up their green ammonia catalyst technology to tackle the 420 MtCO2 p.a. produced by the Haber-Bosch process and reduce global emissions.
Context:
Nium is on a mission to scale up its innovative nanotechnology to produce green ammonia without the use of fossil fuels. To keep up the pace, the company needed scaled up reactor technology to demonstrate the performance of its catalyst technology.
Solution:
To close the gap in process equipment available for green chemistry scale up, TTP designed and built a bespoke ammonia reactor and PLC (programmable logic controller)-controlled test stand for Nium, expediting the development by making innovative use of pre-certified components.
Result:
The “Minion” Mk2 reactor, a 1000X scaled up reactor enabled Nium to demonstrate the performance of their nanotechnology and to capture the data they need to take it to the industrial scale.
TTP became an extension of the team and very quickly understood what we were trying to do, by asking us the right questions they helped us to get to the right outcome quickly. The research was detailed and added value beyond the knowledge we held in the team. They enabled us to move from lab scale to a scale that demonstrated the ammonia production using full process kinetics, all within a tight timescale.
Phil Hunter
COO, Nium
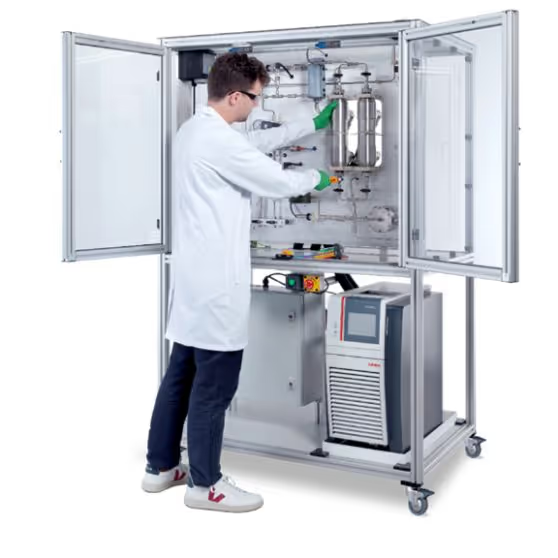
Nium’s mission
Around half of the world’s population depends on food produced using fertilisers derived from ammonia produced via the Haber-Bosch process, which currently accounts for 2% of global CO2 emissions.
Nium is on a mission to decarbonise ammonia production by creating a greener alternative to the Haber-Bosch process using an innovative nanotechnology.
Like other power-to-x companies looking to scale up green ammonia production and green chemicals, Nium found that there was a dearth of suitable process equipment to allow them to move at pace.
Rapid Solution
TTP’s technology consultants went to work fast, translating Nium’s strategic needs into a reactor design that could work safely with hydrogen and manage the ammonia produced. One question we answered for Nium was: What reactor size can realistically be achieved in the time available?
From there on, every aspect of TTP’s technology development programme was geared to allow Nium to keep up the pace. One example is how we identified and integrated pre-certified components and steered clear of the lead times associated with bespoke componentry.
Designed for productivity
The scaled up reactor is supported by a PLC-controlled test stand. The PLC is an off-the-shelf solution for industrial process automation that allows Nium to monitor and control the process remotely and to automatically capture data to explore and optimise the performance of its core technology.
Another example of how we accelerated this project for Nium is that the electrical controls and chemical processing hardware were developed by TTP teams working in parallel, using system modelling to increase the certainty of the design working as intended first time.

Designed for safety
As safety must be key in any process that generates heat and explosive gases, TTP’s reactor design for Nium includes an integrated temperature management system in the reactor and test stand. We also carried out a Failure Modes and Effects Analysis (FMEA), risk assessments, and incorporated sensors and alarms needed for safe operation.
Supporting Rapid Scale up
The Nium “Minion” Mk2 reactor grew from TTP’s concept to onsite installation at Nium’s facility in just four months. Together with the PLC-controlled test stand, it enables Nium to produce insight to support the scale up of their green ammonia production technology to the industrial scale.
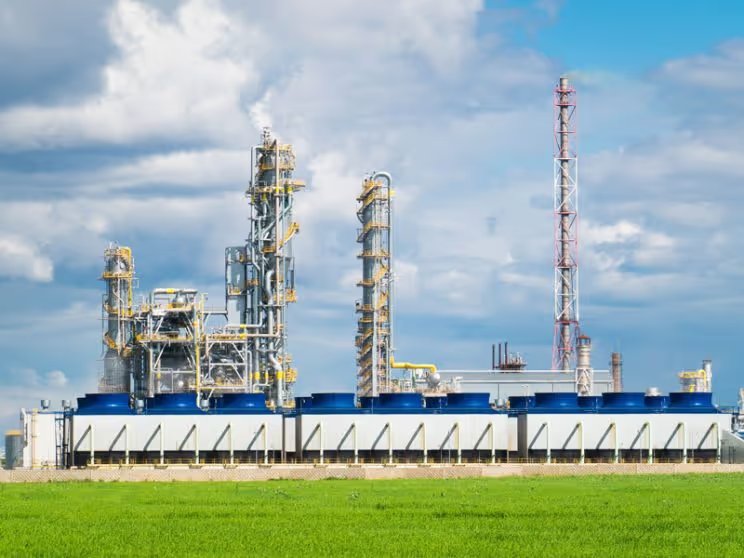