Bespoke sensor solutions based on low power impulse radar can provide valuable insights into material conversion processes in a range of industries.
Process industries are driven by the need to deliver high-efficiency material conversion with minimal waste. Processes for producing materials in large volumes often have ‘multi-phase’ characteristics, contain living organisms or exhibit complex rheology. In such applications, value can be unlocked by having a better real-time view of the state of the process, but standard sensors for pressure, temperature and flow only provide limited insight to process operators and control systems.
Impulse radar is a powerful, low-cost, low-power technology that can be used in wide range of sensing applications, from process monitoring to non-destructive sensing, sub-surface imaging and material characterisation, for example via dielectric property analysis of liquids in the bio-sciences. Combined with bespoke signal processing, impulse radar can deliver meaningful insights for a wide range of industries.
Impulse radar is based on the transmission of very short electromagnetic (EM) pulses (otherwise known as ultra-wideband) which are passed into the media of interest via a free space or guided wave antenna. Reflections of the EM signal are demodulated asynchronously to capture a representation of the time-domain response. The signal is subsequently processed to extract information about the sensed media for use in the application.
In some applications, multiple impulse radar sensors can be used in an array configuration for 2D and 3D imaging applications. In such systems, the repetitive pulses are sent out in a pseudo-random sequence to ensure multiple systems can co-exist and operate without interfering with each other, as well as providing compliance with EMC regulations.
A candidate application for guided wave impulse radar is in the oil and gas industry which faces the challenge of monitoring and controlling multiphase fluids for separation. Conventional sensing solutions are normally built from gamma radiation sources combined with scintillator detectors arranged into an array and fixed to the outside of the tank. This is a high-cost implementation and carries attendant radiation source exposure risks.
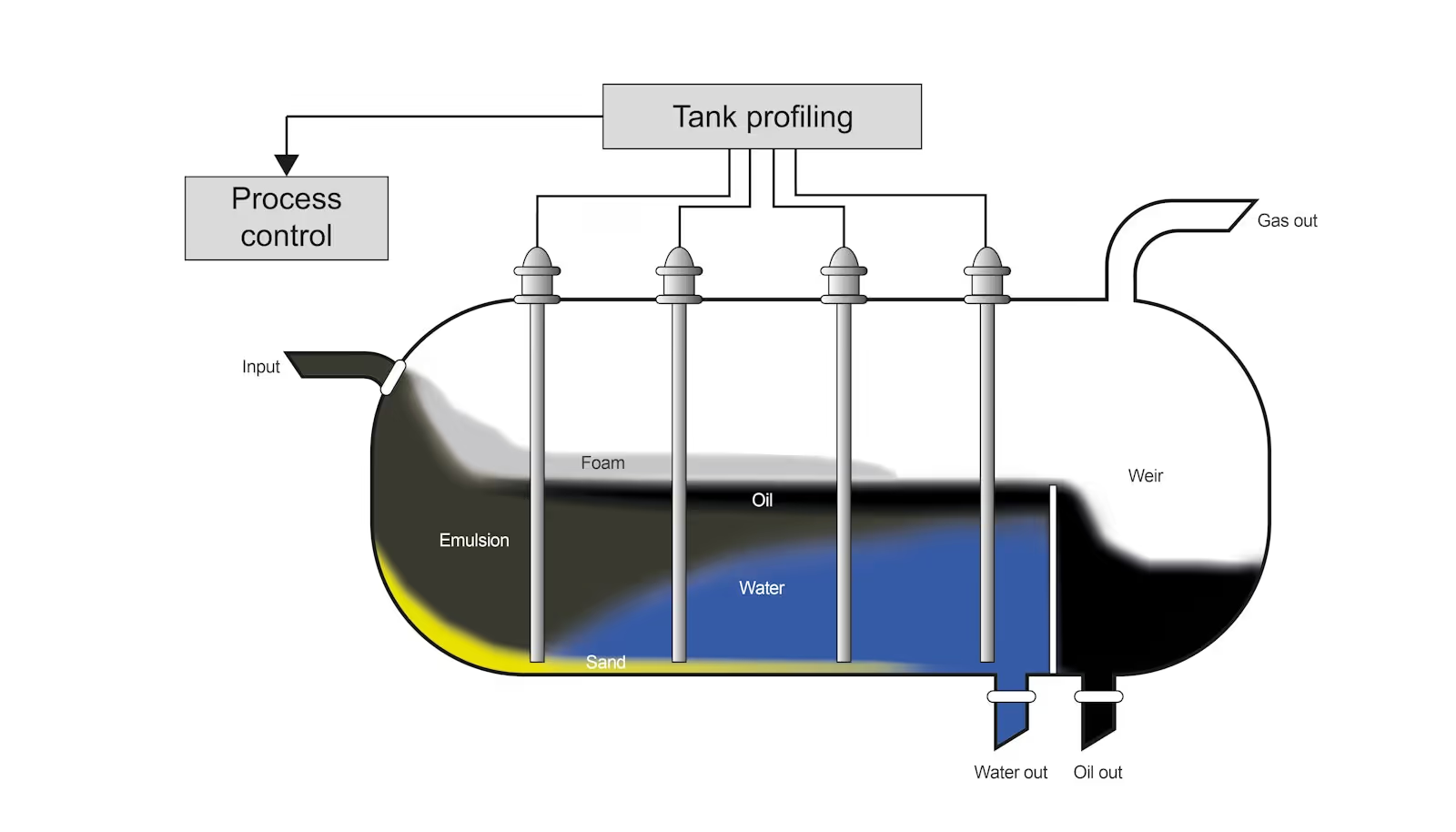
Impulse radar is significantly cheaper and safer, to the point that multiple sensors can be deployed along the length of the separator tank, providing continuous measurement of the gas, foam, oil, emulsion and water levels as the separating emulsion flows from one end to the other. Feedback from the sensor can then be used to optimise the separation process and improve oil recovery.
The images below show examples of measurements taken by a low power impulse radar system being developed at TTP. We are exploring applications for this technology and developing the algorithms to help interpret the signals generated by this type of sensor.
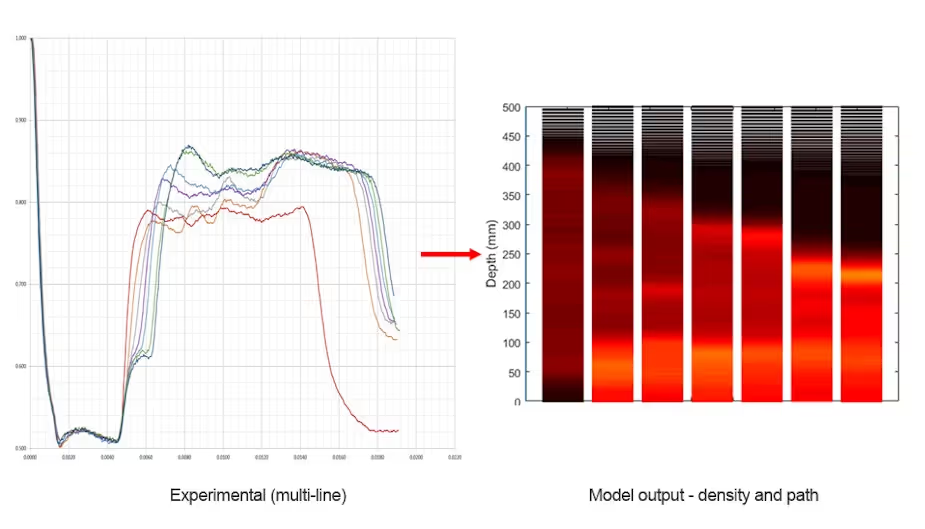
With now very low cost of high-speed embedded computing, the opportunity for impulse radar to deliver meaningful insights is considerable. For more information about TTP's work in this exciting field of metrology, please contact us.