Causes of the component shortage
Whilst Covid-related manufacturing shutdowns have been a major contributor, they were certainly not the only cause of the supply crunch. 2020 also saw Taiwan, home to one of two major semiconductor manufacturers, suffer from the worst drought in over 50 years, thus impinging on the supply of the vast quantities of water required in semiconductor manufacture. The blockage of the Suez Canal also wreaked havoc on global logistics.
The above factors, coupled with a substantial increase in demand for electronics items driven by a combination of technology required for home working and entertainment, have resulted in a perfect storm with lead times of previously common components stretching to a year or more.
In the case of generic components available from multiple manufacturers the impact may be minimal. More complicated components such as microprocessors and RF chips tend only to be available from a single source and are often at the centre of a product’s functionality. Lack of availability of these critical devices will at best delay production and at worst require a near total redesign of a product.
Action #1 – Speak to your component supplier
For both generic and single-source components, the first port of call should be speak to the manufacturer to find out the actual lead time for the component. In our experience, component suppliers are often cautious with information they publish because component availability is currently so volatile. When you speak to them, they may be able to significantly improve upon published lead times.
Generic components
If this doesn’t bring resolution, in the case of generic components it may be possible to identify an alternative manufacturer that can provide equivalently specified components in the required timeframe. But if a direct alternative is not available, things become more interesting.
As a next step, we have found it helpful to look for areas where the specification of the component can be relaxed. For instance, a 5% tolerance part may offer negligible benefit over a more widely available 10% tolerance part. Alternatively, accepting the price increase of a higher specification device can also provide a temporary solution. Generally, sourcing drop-in replacements for generic components is possible with a minimal amount of work.
Single source components
Single source components such as microprocessors present a much bigger challenge. Your first port of call should be to identify compatible devices from the same device family. We have found that these plug-in alternatives sometimes include features that are not required and therefore slightly increase cost. However, specifying such a device is still likely to be more cost-effective than a PCB redesign. Again, varying the specification can also yield dividends. The industrial version of a processor may be pin and code compatible, so changes are at a BoM level only.
If a compatible device cannot be sourced, it may be tempting to resort to so-called ‘grey market’ suppliers for the component that is holding up your product. These companies stockpile popular ICs and then offer them for resale at, let’s say, inflated prices. With unofficial suppliers, it is difficult to be sure, however, that the components have been stored correctly or are even the genuine article. As such, it is difficult to recommend this option – except possibly for limited-run prototype builds that will not be issued to customers.
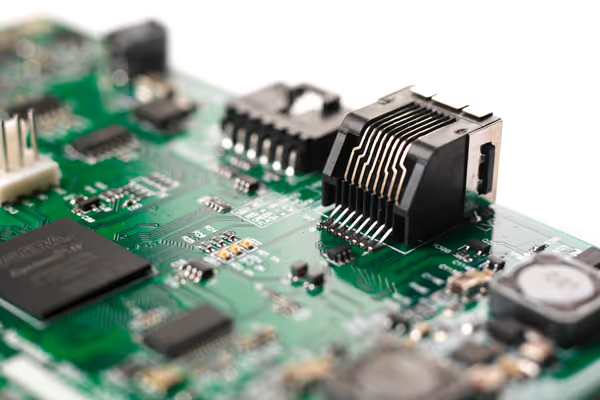
Action #2 – Redesign the electronics of your product
If you have tried the above approaches to no avail, a redesign of your product’s electronics will be required. In terms of hardware, when choosing a replacement device attention should be paid to power supply and physical size requirements. A larger or more power-hungry device will necessitate further design changes in the rest of the system. If the chosen replacement has a similar footprint to the incumbent and similar power requirements, these can be avoided.
A major element of switching to a new processor design is porting the existing software to the new target. Even when the processor core is the same (for example ARM devices from different semiconductor manufacturers) they often have different operating quirks that can trip you up. Good firmware design will include a well-defined Hardware Abstraction Layer (HAL) to make porting to a new target easier. If this is not the case, then the porting process presents a good opportunity for you to add future-proofing to the firmware by using this approach.
Whilst designing in a new processor represents a significant overhead for your engineering team, it can also deliver benefits. At the end of your design update, you potentially have two manufacturable product designs giving you diversity of supply, something which purchasing departments love because it can provide some isolation from future supply issues.
The other benefit of an unplanned redesign is that you can take advantage of advances in processor technology that have occurred since the original product was released. A recent redesign of an IoT product prompted by the component shortage also yielded a significant reduction in power consumption thanks to advances in processor design. Whilst battery life may not be critical in your application, other ‘bonus’ features such as supporting a new radio standard or faster processing may now be possible without an increase in product cost.
In summary, once you have recognised that your design is likely to be affected by the component shortage the key is to quickly decide on a course of action and engage with suppliers – Action #1 identified in this post. In more extreme cases, you have some work to do to redesign the component – Action #2 identified in this post – but you may come out the other side with an improved product and a more robust supply chain.
TTP offers highly agile multi-disciplinary engineering teams to solve product and technology development challenges. In the past 12 months, we have addressed component shortages for several of our clients. If you want to discuss the contents of this article, please get in touch.