Multiple industries are working hard to scale up the production and use of hydrogen as a low-carbon energy vector, with the hope that its wider adoption will contribute ten per cent of the reduction in annual global greenhouse gas emissions needed to reach net zero [1].
However, this wider adoption faces many technical challenges, not least related to storage and transportation. As the lightest and smallest molecule in the universe, hydrogen is liable to escape, creating a significant risk of serious explosions, not to mention economic loss. In a world where hydrogen is generated from limited renewable energy sources, we can ill afford to allow it to escape, and if it does escape, we need to know about it.
Moreover, recent research suggests that hydrogen is a stronger indirect greenhouse gas than previously thought. This suggests that leak detection and monitoring may also be necessary to ensure that industrial leakage is well-controlled, and leakage monitoring may be mandated by future regulation [2, 3].
Industry is already served with a variety of low cost sensors, from catalytic combustion detectors to electrochemical and advanced solid state sensors, but none of them quite yet fit the bill for the expanding role of hydrogen in the energy landscape.
Hydrogen gas sensing for leak detection and process control
Numerous gas sensing technologies have been developed to detect escaping gas before the lower flammable limit (LFL) in air is reached. For hydrogen that’s 4%, and the working range of many available hydrogen gas sensors is limited to 0–4%.
With the expanding role of hydrogen in the energy landscape, the requirements for detection and sensing are rapidly evolving to help manage risks associated with leaks or to provide feedback for process control.
The hydrogen value chain begins with production via electrolytic, pyrolytic and reforming processes. Of these, electrolytic methods are gaining prominence, as they offer green hydrogen manufactured directly from renewable sources of electricity. In such systems, crossover of hydrogen and oxygen can give to rise to efficiency losses and, at the anode, explosive gas mixtures of hydrogen in oxygen can be formed. Accurate control enabled by hydrogen sensing could lead to gains in efficiency and safety.
Further down the value chain, hydrogen may then be processed or converted for distribution. As an example, hydrogen compression and liquefaction for transport requires a lot of energy, costly plant, and is associated with considerable leakage or boil-off during transport [4, 5]. In mitigation, ammonia is currently finding favour as an alternative means of hydrogen transport and as a green fuel in its own right. That too presents new challenges given the need to avoid exposure to the toxic effects of ammonia.
Hydrogen may also be blended with natural gases to reduce carbon emissions from power generation and domestic heating. If hydrogen is blended into the gas grid, then there is the potential need to determine the calorific content of gas mixtures being consumed at the point of sale.
In each of these processes, sensors will be required to monitor and control the level of hydrogen (or ammonia) with the anticipation that the underlying technologies must offer flexibility to address a wider range of measurement challenges than traditional leak detection has historically required.
Existing sensing technologies offer limited measurement range and stability
Today, catalytic and electrochemical sensors are widely used for leak detection in the oil and gas industry. Many low-cost versions of these sensors offer limited measurement stability and operating life, however.
In addition, low-cost versions of these sensors, and even advanced solid-state sensors, suffer from cross-reactivity with other gases or poor measurement stability when exposed to hydrogen.
Although better versions of all these technologies will surely be developed, many only work in the presence of oxygen, reflecting their provenance in safety applications. As such, they are unsuitable for process applications where hydrogen is mixed with other gases.
SonicSense can enable leakage monitoring, process control and gas metering
At TTP, we have developed a small, low-cost sensor that determines the composition of a mixture of gases by means of a physical measurement: the speed of sound in a small cavity.
The sensor is highly resistant to chemical attack and unaffected by many of the gases that throw off chemical sensors. The device also offers excellent measurement stability as well as measurement range, combined with low power consumption and a long operating life when compared to other available technologies. With further development, it offers an important ‘fit and forget’ solution which shouldn’t require recalibration during its lifetime, minimising OPEX costs.
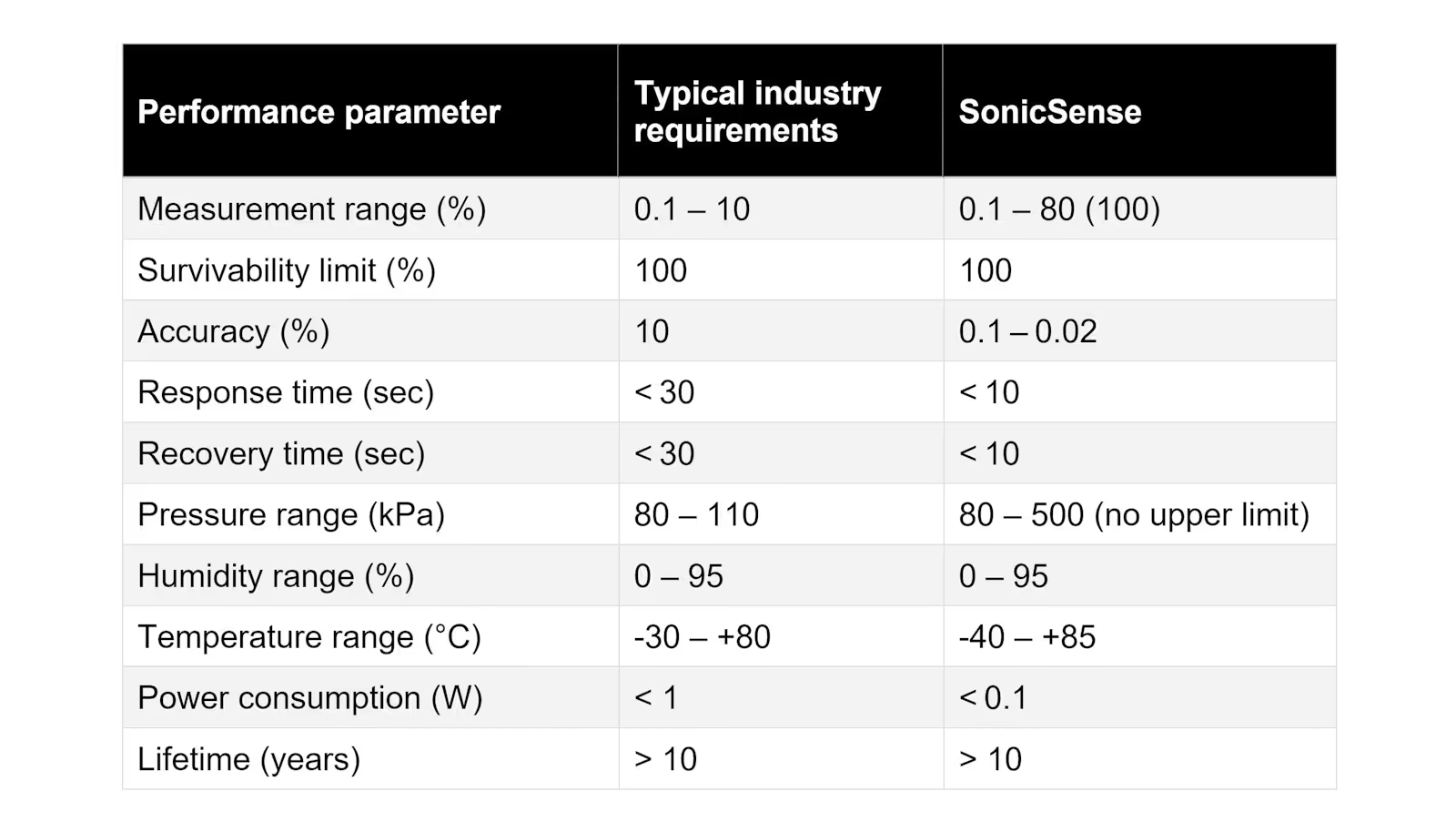
In contrast to many existing hydrogen sensors, our device can accurately measure hydrogen in any other gas from 0.1% to 100% hydrogen. Interestingly, over this range, the accuracy of speed of sound measurement increases.
This means that our sensing platform is suitable for leak detection and leakage monitoring (below the LFL) but also intrinsically well-suited to measuring the composition of mixtures with other gases when the hydrogen content is much greater. Besides, the wide window of flammability of hydrogen implies that a wider measurement range is relevant even for safety sensors.
The sensor could be used to control and monitor the blending of hydrogen in the natural gas grid, to determine the calorific value of gas mixtures at the point of sale in conjunction with other measurements, or to measure ammonia and air mixtures to detect ammonia leaks or control future climate-friendly ammonia engines. It also offers potential to detect hydrogen off-gassing from faulty lithium batteries.
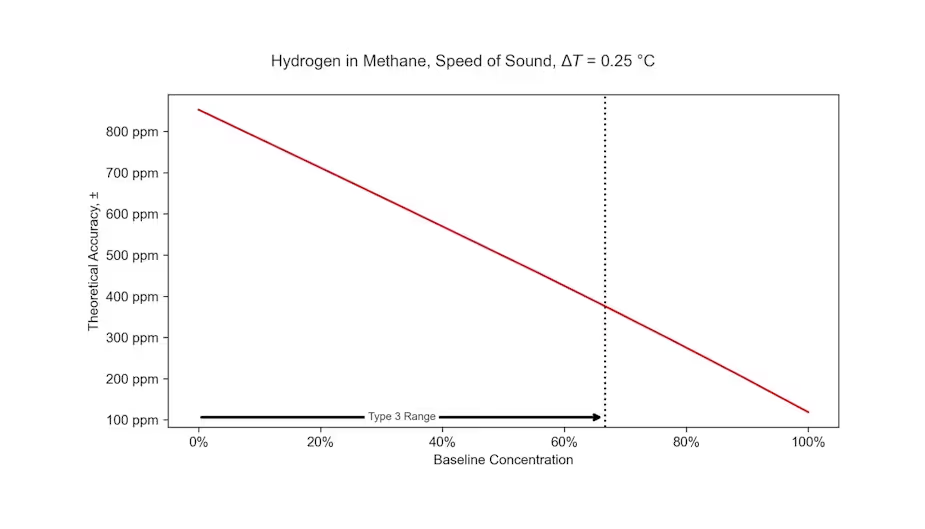
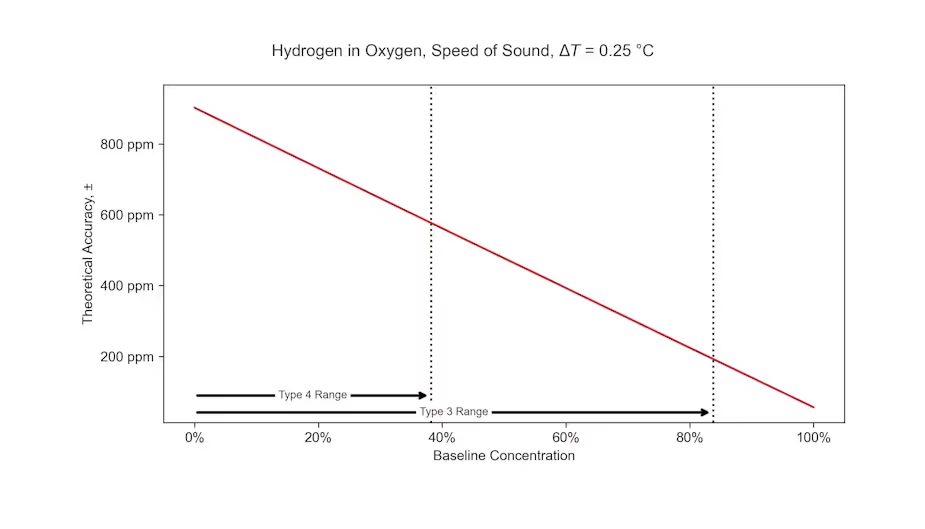
Over several generations of prototypes, we have progressively miniaturised the technology. This, together with a long operating life, now provides a technology that can be further developed and integrated into industrial equipment without the need for recalibration or sensor replacement. In static safety applications, a low-power device could provide the first line of defence that wakes up other sensors as soon as hydrogen is detected.
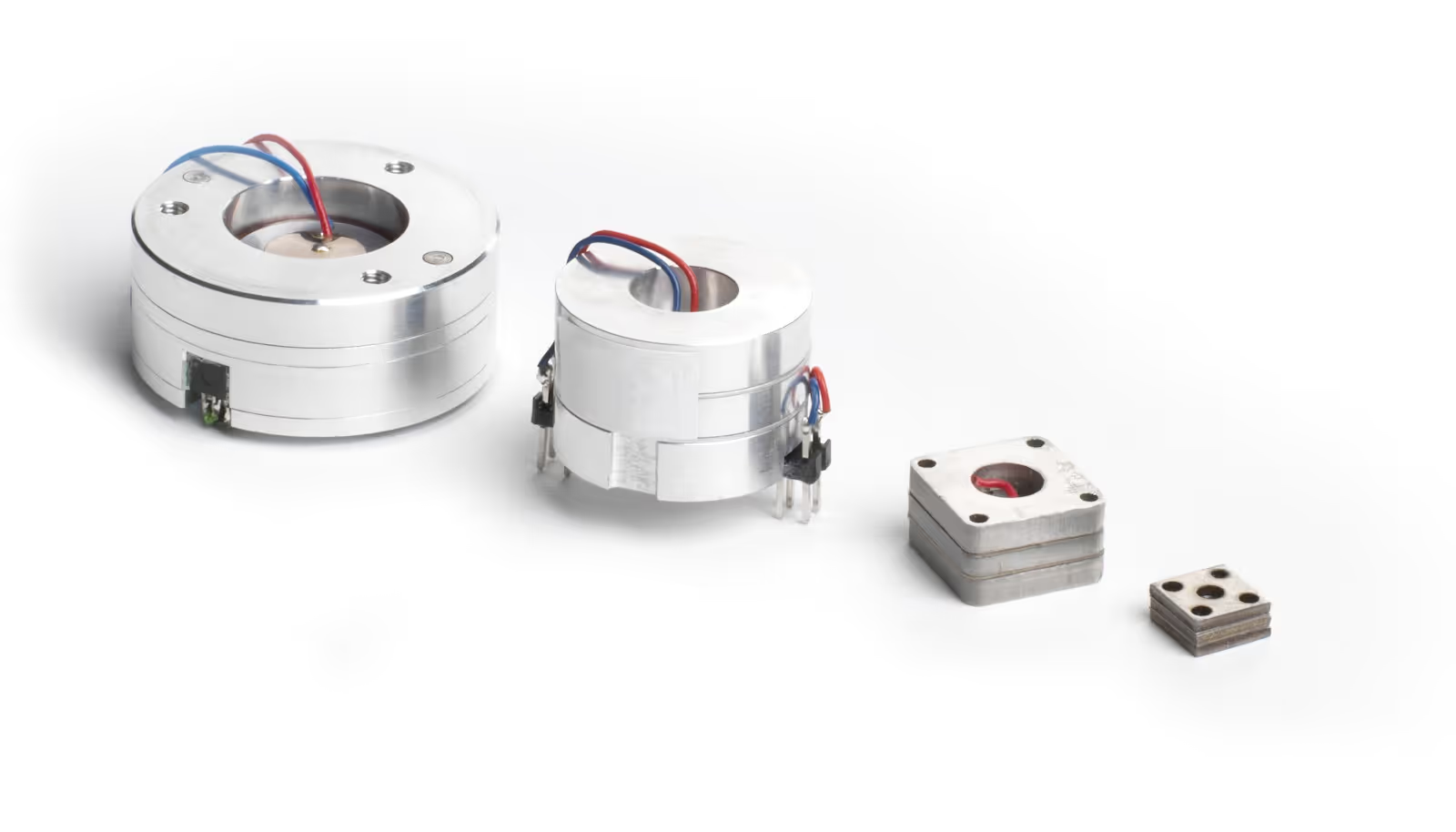
Previously, we have supported Philips Respironics in integrating our SonicSense platform into a sensor for measuring the purity of oxygen delivered to the patient by a medical device.
SonicSense is a flexible gas sensing platform that can be developed to meet specifications for a range of process and safety applications. A SonicSense evaluation kit can be supplied on request. Please reach out to TTP if you would like to learn more.
Find out more about our capabilities in Hydrogen, Energy and Industrial Safety.
References
01. Green gases can help in the shift from fossil fuels to electricity, The Economist
02. Siemens Energy to build ‘multi-gigawatt’ hydrogen electrolyser factory in Berlin. Recharge
03. Enapter eyes 83% cost reduction for its unique AEM hydrogen electrolysers by 2025, Recharge