From Tanzania to Scotland, demonstration missions have shown that UAVs can provide vital services by delivering medical supplies and aid in regions without roads, enabling faster on-demand delivery to remote areas.
But although UAVs are capable of automated flight to reach their destination, regulators only allow beyond visual line of sight (BVLOS) operations with specific permissions along particular corridors.
In all other circumstances, the risk of mid-air collisions causes aviation safety rules to forbid autonomous operation, effectively forcing new business models that depend on autonomous UAV flight at scale for delivery, inspection and people transport into a holding pattern until the technology is ready.
To satisfy aviation authorities that BVLOS operations are not a risk to other airspace users or those on the ground, the industry needs reliable sensor-based “detect and avoid” (DAA) technologies.
Of course, additional sensors add weight, power consumption and cost, with every extra gram and Watt reducing the operating time and range of the aircraft. The challenge, then, is to develop DAA technology that is effective enough to de-risk BVLOS operations within an acceptable budget of Size, Weight, Power and Cost (SwaP-C).
To help move the industry forward and speed up the development of DAA sensor packages that will enable BVLOS operations, we undertook a study into the detection limits of different sensor types, data processing methods, and the UAV industry’s needs for SWaP-C.
How can UAVs detect other aircraft?
To detect other aircraft, UAVs can use vision-based systems (like human pilots), acoustic methods (like animals that hunt at night), or radar (like commercial aircraft). For the time being, lidar sensors are not yet small and powerful enough to meet the requirements of a DAA system.
Other airspace users that need detecting take a variety of forms. Many will be conventional crewed aircraft and other UAVS, but there will also be less conventional airspace users such as hang gliders or hot-air balloons. This poses additional challenges as they will have different cross-sections and are nearly silent.
Safe UAV flight requires that all threats are detected in time for the sensor data to be processed and avoidance manoeuvres to be initiated. We used ASTM International’s collision avoidance standards for small aircraft (ACAS-sXu) to determine how capable a detection system needs to be to match the safety of conventional aircraft [1].
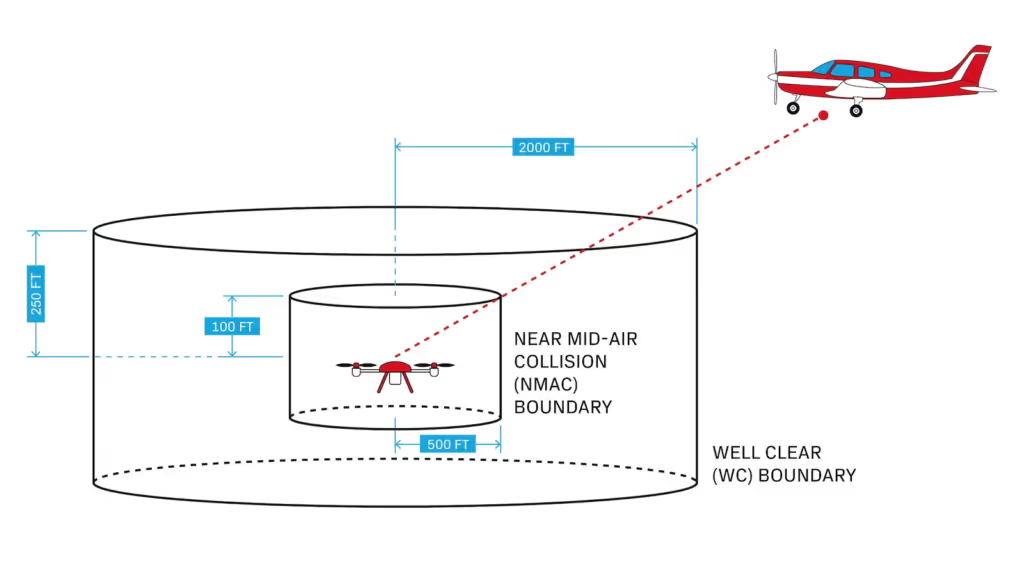
What does the industry need?
We asked stakeholders across the industry what SWAP-C budget they regard as acceptable for the UAVs they are developing. Unsurprisingly, the shopping list for SWAP-C requirements breaks down by maximum take-off weight (MTOW).
At the lower end of MTOW – corresponding to UAVs for facility inspection and small cargo delivery – industry stakeholders were sensitive to size, weight and power and cost. Developers of larger, cargo-carrying UAVs and air taxis whilst also sensitive to cost and size were less so to weight.
The toughest technology challenge is undoubtedly an onboard DAA solution for low MTOW aircraft. So based on our conversations, we set ourselves a target detection range of greater than 1 km at an aggressive SWAP-C budget of 500g, BoM $1000, 10W of power.
We then went back to first principles to work out the minimal required capability of the above sensors, by asking questions like, what is the minimum number of visual pixels, or the minimum acoustic link budget needed to identify other airspaces users in good time.
We then fed different minimal architectures of the above sensors with real or simulated data, applied different data processing techniques, and asked whether we can hit our SWAP-C budget.
Industry SWAP-C budgets are achievable, but sensor fusion will be key
The results again fell out differently across high and low MTOW.
Cost was the main challenge in meeting our SWAP-C and performance targets for large, fast-flying drones, whilst hitting the weight target was the main challenge for smaller drones.
Different flight and mission characteristics also favour different primary sensors, or combinations of primary and secondary sensors, as the basis of the detection system. For example, visual detection may be good as a primary sensing system for UAVs operating under conditions of low closing speeds with other aircraft, while longer-range radar may be the primary sensor of choice at high closing speeds.
Secondary sensors could be crucial UAV safety when the primary sensing system is impaired due to environmental conditions or sensing artefacts. When this happens, secondary sensors can provide minimal fallback performance for DAA – perhaps to keep the drone safe until the primary sensors are restored, or until the UAV has landed safely.
Secondary sensor systems, some of which come ‘cheap’ in terms of SWAP-C, can also improve the fidelity of the overall detection system or provide a ‘tip and cue’ function for the primary sensors. Some UAV manufacturers are already integrating multiple sensor offerings into their airframes, but in the future tighter integration of complementary sensor systems for DAA will be key.
Find out more
If you want to find out more about our results, how close we came to our SWAP-C budget with advanced data processing, and how we see the road to certification, please download our whitepaper.
References
01. Standard Specification for Detect and Avoid System Performance Requirements (astm.org)
02. Graphic adapted from ACAS-sXu specification