Small Robot Company partnered with TTP to develop a multimodal sensor system for obstacle detection, reducing the need for human supervision in challenging off-road environments while ensuring safety and compliance.
Context:
Small Robot Company (SRC) are using ruggedised robots and AI to remove humans from harm in challenging off-road environments. To optimise fleet economics, SRC wanted to reduce reliance on human supervisors to monitor their robotic fleet’s safety. They sought automated technology that wouldn’t sacrifice reliability or risk non-compliance with essential regulations around safety.
Solution:
TTP developed a prototype multimodal sensor system for obstacle detection. Using classical algorithms and leveraging sensor fusion, this could reliably detect obstacles and prevent collisions while maintaining efficiency.
Result:
TTP delivered a radar-camera fusion system that can reliably detect a range of obstacles even under difficult operating conditions, providing the basis for an ISO-compliant safety system.
The challenge: Steering agricultural robots off the beaten track
Agricultural robots might seem to operate in lower-risk environments than their urban counterparts, but arable fields are dynamic environments which require robust safety measures. Any pre-planned route assigned to a farming robot would be subject to disruptions—whether a farm worker, dogs being walked, or a closed gate that should have been left open. For this reason, ISO 18496 stipulates that agricultural robots must be able to detect and avoid both static and moving obstacles—including those obscured by crops, dust, fog, snow and rain. This poses a challenge for companies developing agricultural robotics, and often leads to a reliance on extensive human monitoring.
SRC wanted to address this issue by equipping their robots with a safety system for obstacle detection. However, no off-the-shelf solutions currently exist. This led SRC to seek TTP’s expertise in sensing and autonomous systems to try and find a solution. Together, we set out to develop a bespoke system for their platform that, through a combination of sensors, compute and software, would reliably detect obstacles under a wide range of conditions, and direct the robot accordingly.
Autonomous operation is a critical factor in SRC’s market advantage. If one operator can manage a fleet of two, or three… or five robots, then that is a massive benefit to the productivity of the platform and the economics of the business. Autonomy that enables remote oversight with minimal human supervision re-quires safety systems that can ensure collision avoidance in all conditions.
The work we’re doing with TTP is therefore crucial not just for the safety case but also the business case.
Laura Parnell
COO, Small Robot Company
How we did it
In close collaboration with SRC, our team developed a prototype multi-sensor system that uses classical algorithms to detect potential obstacles. Having been pre-emptively optimised to the farming robots’ needs, we were able to install and integrate the package in SRC’s robot in under a day.
Sensor Fusion
It was decided to combine stereo camera and radar sensors to overcome the limitations faced by any single technology. Cameras are important to provide detailed information under well-lit conditions. Meanwhile, radar sensors can determine distance – whether light or dark – and penetrate dust or fog.
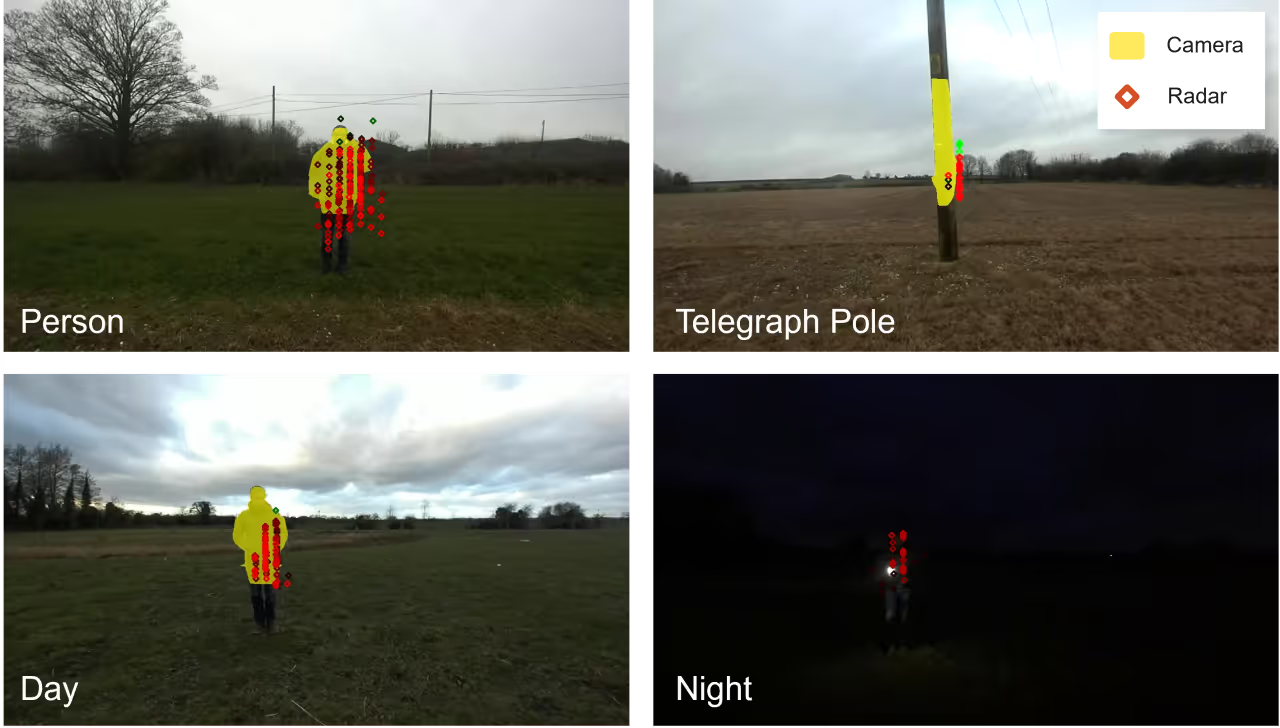
Non-artificial Autonomation
Subsequently, we developed algorithms to interpret the sensor data. Evaluating changes in this data allowed the nature and severity of any obstruction to be deciphered, and its threat to operations quantified. Because ISO 18496 stipulates that algorithms must follow clear processes that humans can understand, our system depends on classical algorithms instead of neural networks.
Sensor fusion technologies allowed us to combine data from both sensor feeds, thereby enabling the robot to reconcile the two inputs to clarify its surroundings. This permitted action to be taken accordingly: to stop for a genuine obstacle; or to ignore the peripheral interruption.
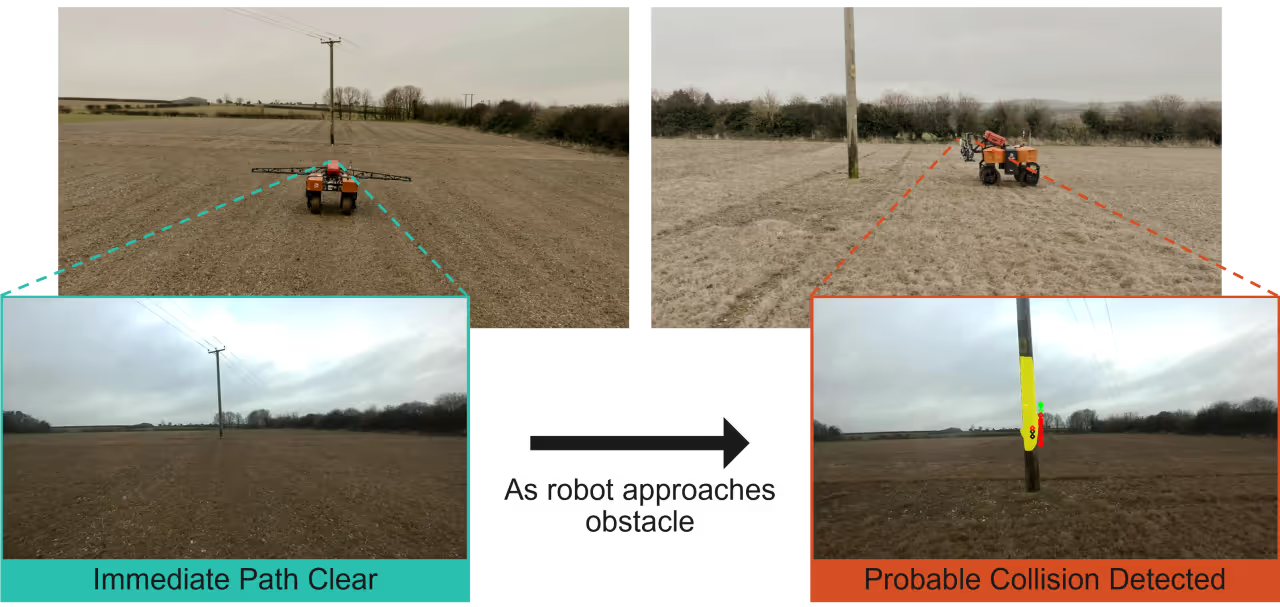
Detect and avoid
Our sensor package can detect and monitor an obstacle’s position long before it becomes a danger, allowing an automated decision to be made to stop the robot only when a collision is likely. This ability to assess and monitor obstacles before they become dangerous is crucial. It allows the robot to ignore things like birds flying in front of the sensors, allows for time for animals and people to move out of the way, and reduces the impact of false detections. This ensures that the robot can safely evade obstacles, while minimising unnecessary interruptions.
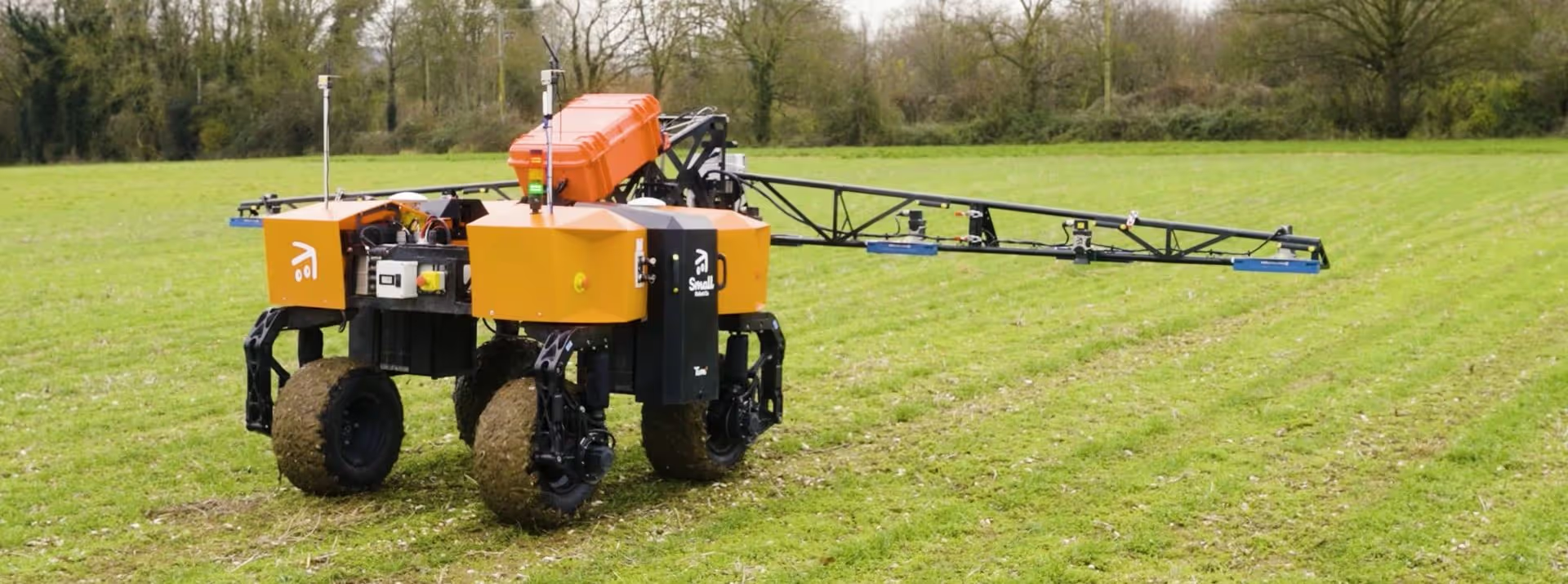
Farming the future
Our safety system is also equipped for the future. As testing continues, our system will improve confidence that agricultural robots can operate under diverse circumstances with minimal human intervention. This could vastly broaden the horizons of agricultural robotics, enabling larger fleets to operate for longer durations at lower cost. Capable of expanding into an ISO-compliant safety system, our technology likewise offers valuable learning insight from which other autonomous safety systems can emerge.
Revolutionising agriculture, therefore, is just the beginning for this technology. The same principles could enable autonomy in other sectors where vehicles must react quickly to changes in their environment—such as mining and airport logistics.