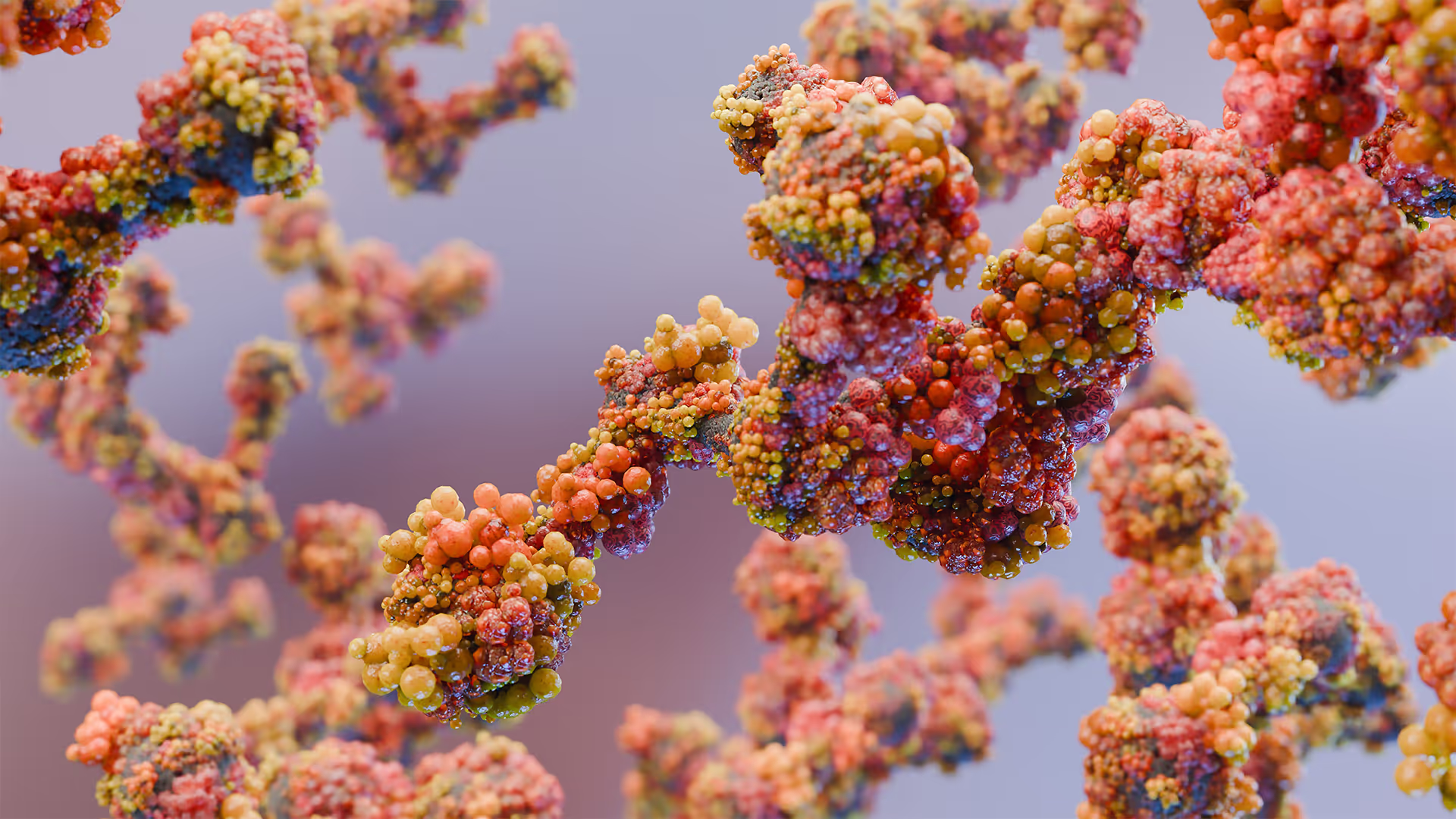
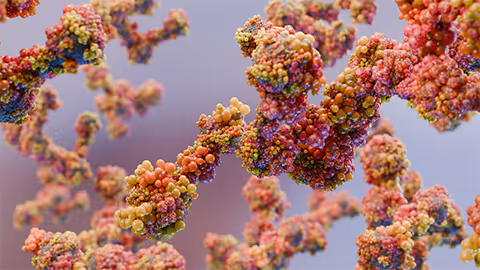
We can help you accelerate innovation and unlock your competitive advantage in a changing world.
As an independent technology and product development consultancy, we’ve spent nearly 40 years helping our clients solve complex challenges and deliver commercially grounded solutions.
Because having the right team on your side makes all the difference. Let’s talk.
Human tissue makes consistent connectivity in implants a formidable engineering challenge. Qing Liu explains how we're combining anatomical modelling, predictive simulation and in-house RF testing, to tackle the issue.
We want releaze™ to be the most user-friendly drainage solution for recurrent pleural effusion, transforming the patient experience in the process. TTP’s proven expertise in medical device development gave us confidence from the outset. Their experience with complex electromechanical systems and taking devices through to market meant they could develop the drainage hub quickly, reliably, and with real efficiency. TTP were flexible in their approach and collaborated early with our manufacturing partner, Phillips-Medisize, to ensure the design was manufacturable from day one. The resulting hub design perfectly complements the simplicity of our catheter system. It is intuitive to use, reassures users and gives patients invaluable independence.
Tim Jones
CEO, SymPhysis
Developing the Sat Companion required groundbreaking innovation in antenna design. TTP engineered a high-gain antenna system that not only enables direct-to-mobile 5G NTN connectivity but also meets the most stringent SAR regulations, ensuring both performance and user safety. This achievement marks a significant step forward in making seamless global communication a reality.
Serge Legris, Eng.
CTO, Terrestar Solutions Inc.
The microFlex system accelerates time to market by enabling translation of existing immunoassay chemistries with minimal development. It mimics a central-lab workflow, automating vacuum tube-to-plasma processing with an integrated centrifuge, supports customisable workflows in a sealed cartridge to deliver central-lab quality assays, and has robust IP protection with a range of granted and pending patents on key technologies, including its centrifuge and vacuum-tube handling.
Ben Metcalf
Project Leader, TTP
We deliver state-of-the-art solutions for companies across a broad range of sectors, explore our areas of focus below.
Lorem ipsum dolor sit amet, consectetur adipiscing elit, sed do eiusmod tempor incididunt ut labore et dolore magna aliqua. Ut enim ad minim veniam, quis nostrud exercitation ullamco laboris nisi ut aliquip ex ea commodo consequat. Duis aute irure dolor in reprehenderit in voluptate velit esse cillum dolore eu fugiat nulla pariatur.
Lorem ipsum dolor sit amet, consectetur adipiscing elit, sed do eiusmod tempor incididunt ut labore et dolore magna aliqua. Ut enim ad minim veniam, quis nostrud exercitation ullamco laboris nisi ut aliquip ex ea commodo consequat. Duis aute irure dolor in reprehenderit in voluptate velit esse cillum dolore eu fugiat nulla pariatur.
Lorem ipsum dolor sit amet, consectetur adipiscing elit, sed do eiusmod tempor incididunt ut labore et dolore magna aliqua. Ut enim ad minim veniam, quis nostrud exercitation ullamco laboris nisi ut aliquip ex ea commodo consequat. Duis aute irure dolor in reprehenderit in voluptate velit esse cillum dolore eu fugiat nulla pariatur.
Lorem ipsum dolor sit amet, consectetur adipiscing elit, sed do eiusmod tempor incididunt ut labore et dolore magna aliqua. Ut enim ad minim veniam, quis nostrud exercitation ullamco laboris nisi ut aliquip ex ea commodo consequat. Duis aute irure dolor in reprehenderit in voluptate velit esse cillum dolore eu fugiat nulla pariatur.
Lorem ipsum dolor sit amet, consectetur adipiscing elit, sed do eiusmod tempor incididunt ut labore et dolore magna aliqua. Ut enim ad minim veniam, quis nostrud exercitation ullamco laboris nisi ut aliquip ex ea commodo consequat. Duis aute irure dolor in reprehenderit in voluptate velit esse cillum dolore eu fugiat nulla pariatur.
Lorem ipsum dolor sit amet, consectetur adipiscing elit, sed do eiusmod tempor incididunt ut labore et dolore magna aliqua. Ut enim ad minim veniam, quis nostrud exercitation ullamco laboris nisi ut aliquip ex ea commodo consequat. Duis aute irure dolor in reprehenderit in voluptate velit esse cillum dolore eu fugiat nulla pariatur.
You’ll learn from the specialists around you. Because our project teams are made up of scientists and engineers from different disciplines, you’ll never stop learning from those around you (and they’ll keep learning from you).
And within our collaborative client-focused projects, with the support of the team around you, you’ll develop the client-facing and commercial skills to sell your ideas.
Our campus has been designed with a clear vision. To create a space which can support our people and our clients as we develop and deliver the very best technology solutions.